Unveiling the Intricacies of Brushless Motors: A Complete Guide to Understanding
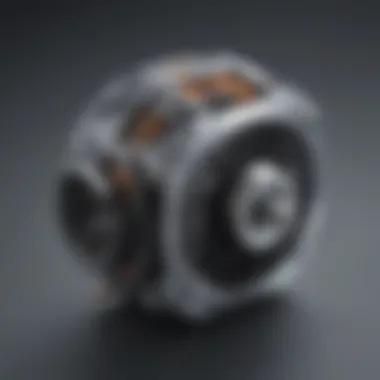
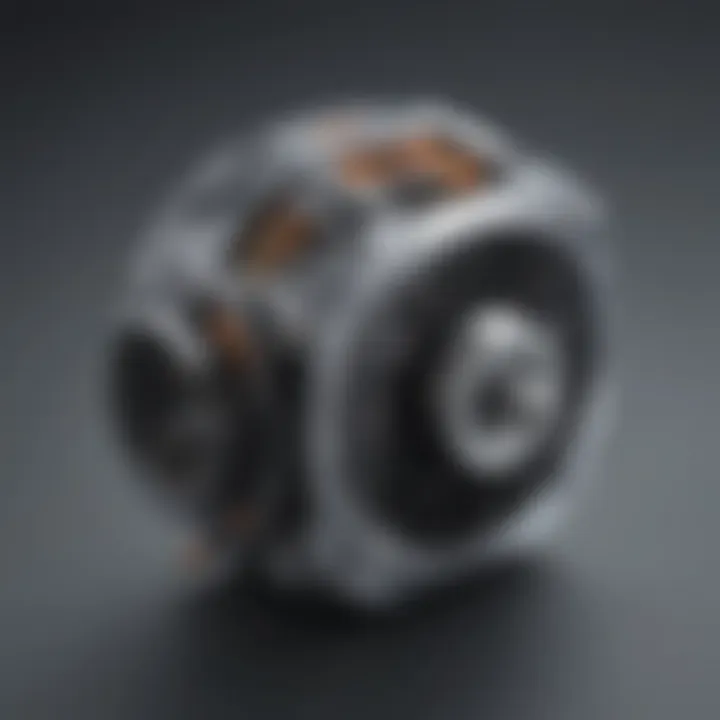
Overview of Brushless Motors
Brushless motors are a critical component in modern tech devices, offering efficiency and versatility. Understanding their inner workings is essential for anyone delving into the realm of technology. This section will provide an introduction to the main concept of brushless motors, emphasizing their scope and significance in the tech industry. Additionally, a brief history and evolution of these motors will be explored to trace their development over time.
Fundamentals of Brushless Motors
Delving into the fundamentals, this section will uncover the core principles and theories related to brushless motors. Key terminology and definitions integral to grasping the essence of these motors will be elucidated. Basic concepts and foundational knowledge will be discussed to provide a solid understanding of how these motors operate.
Practical Applications of Brushless Motors
Real-world case studies and applications of brushless motors will be highlighted in this section. Demonstrations and hands-on projects will be showcased to illustrate how these motors are utilized in various technological applications. Moreover, code snippets and implementation guidelines will be shared to offer practical insights into incorporating brushless motors.
Advanced Topics and Latest Trends in Brushless Motors
Exploring cutting-edge developments in the field, this section will delve into advanced techniques and methodologies associated with brushless motors. Future prospects and upcoming trends will be discussed to provide a comprehensive view of where the technology is heading in the coming years.
Tips and Resources for Further Learning
For those seeking to deepen their understanding of brushless motors, this section will recommend books, courses, and online resources for further exploration. Tools and software essential for practical usage of brushless motors will also be provided, equipping readers with the necessary resources to delve deeper into this domain.
Introduction to Brushless Motors
Brushless motors are a crucial component in various technological devices, playing a significant role in ensuring efficient operation. Understanding the fundamentals of brushless motors is essential for anyone working with technology or interested in the intricate details of modern machinery. This section will provide a detailed overview of brushless motors, highlighting their importance, benefits, and practical considerations.
Overview of Brushless Motors
Definition of Brushless Motors
Brushless motors are electromechanical devices that convert electrical energy into mechanical energy without the need for physical commutation. This innovative design eliminates the use of brushes found in traditional brushed motors, leading to improved efficiency and reduced wear and tear.
Distinction from Brushed Motors
The primary feature that sets brushless motors apart from brushed motors is the absence of physical commutators and brushes. This distinction results in smoother operation, higher reliability, and enhanced longevity for brushless motors, making them a popular choice in modern technological applications.
Basic Operating Principle
The basic operating principle of brushless motors involves the interaction between the rotor and stator through electronic commutation. By using sensors and an electronic speed controller (ESC) to control the motor's phases, brushless motors can achieve precise and efficient operation, making them ideal for a wide range of industrial and consumer applications.
Advantages of Brushless Motors
Higher Efficiency
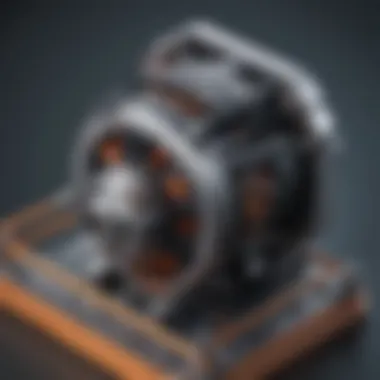
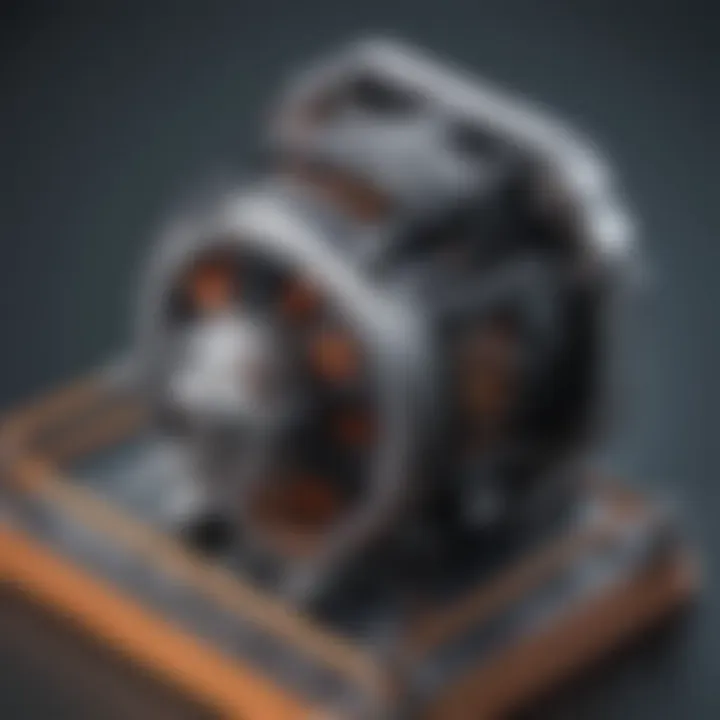
One of the key advantages of brushless motors is their higher efficiency compared to brushed motors. The streamlined design of brushless motors results in lower energy losses, reduced heat generation, and increased overall performance in various operating conditions.
Reduced Maintenance Needs
Due to the absence of brushes and physical commutators, brushless motors require minimal maintenance compared to their brushed counterparts. This reduced maintenance need translates to lower operational costs and extended lifespan, making brushless motors a cost-effective and reliable choice for many applications.
Enhanced Durability
Brushless motors exhibit enhanced durability due to their solid-state design and reduced mechanical components. This durability leads to fewer chances of mechanical failures, increased resistance to environmental factors, and prolonged operational life, making brushless motors a resilient and long-lasting option for critical applications.
Common Applications
Aerospace Industry
In the aerospace industry, brushless motors are utilized in various critical systems, including actuators, pumps, and control surfaces. Their high efficiency, precise control, and reliability make them essential components in achieving optimal performance and safety in aerospace applications.
Electric Vehicles
The use of brushless motors in electric vehicles has revolutionized the automotive industry by providing efficient and eco-friendly propulsion systems. The high torque, rapid response, and energy efficiency of brushless motors contribute to the success of electric vehicles in reducing carbon emissions and dependency on fossil fuels.
Industrial Automation
In industrial automation, brushless motors play a vital role in powering machinery, robotics, and automated systems. Their ability to deliver consistent performance, precise positioning, and adaptive control makes them ideal for enhancing productivity, quality, and efficiency in manufacturing and production processes.
Key Components of Brushless Motor
Brushless motors are intricate machines composed of several essential components crucial to their efficient operation. Understanding these key components is paramount when delving into the world of brushless motors. The rotor and stator form the fundamental structure of a brushless motor, with each playing a vital role in its functionality. The electronic speed controller (ESC) acts as the brain of the motor, governing its speed and performance. Hall effect sensors, on the other hand, aid in detecting rotor position, ensuring smooth operation and facilitating integration with the ESC. Each component interacts harmoniously, contributing to the overall efficacy and reliability of brushless motors.
Rotor and Stator
The rotor and stator are integral components of a brushless motor, essential for its operation. The rotor, typically the moving part of the motor, rotates within the stationary stator. This motion generates the electromagnetic field necessary for propulsion. The stator, with its fixed position, provides the magnetic field against which the rotor operates, inducing motion. The interaction between the rotor and stator is crucial for the motor's efficiency and power output. While the rotor facilitates movement, the stator's magnetic field ensures stability and direction, creating a balanced system for optimal performance.
Electronic Speed Controller (ESC)
The electronic speed controller (ESC) is a pivotal component in brushless motors, responsible for regulating motor speed and performance. By receiving signals from the main control unit, the ESC controls the electric current delivered to the motor to adjust its speed as required. Additionally, the ESC incorporates feedback mechanisms to ensure precision and stability in motor operation. While ESCs enhance motor performance and efficiency, improper calibration or malfunction can adversely affect motor functionality, emphasizing the importance of quality ESCs in brushless motor systems.
Hall Effect Sensors
Hall effect sensors play a critical role in brushless motors by detecting rotor position and facilitating seamless operation. By monitoring the magnetic field variations produced by the rotor, these sensors enable precise control over motor functions. Ensuring smooth operation, Hall effect sensors contribute to the motor's overall performance reliability. Moreover, their integration with the ESC enhances motor system efficiency, optimizing power utilization and enhancing response times. Despite their benefits, challenges may arise in sensor calibration and positioning, requiring meticulous attention to detail for optimal sensor functionality and motor performance.
Working Principle of Brushless Motors
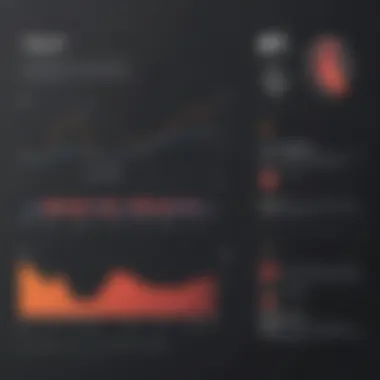
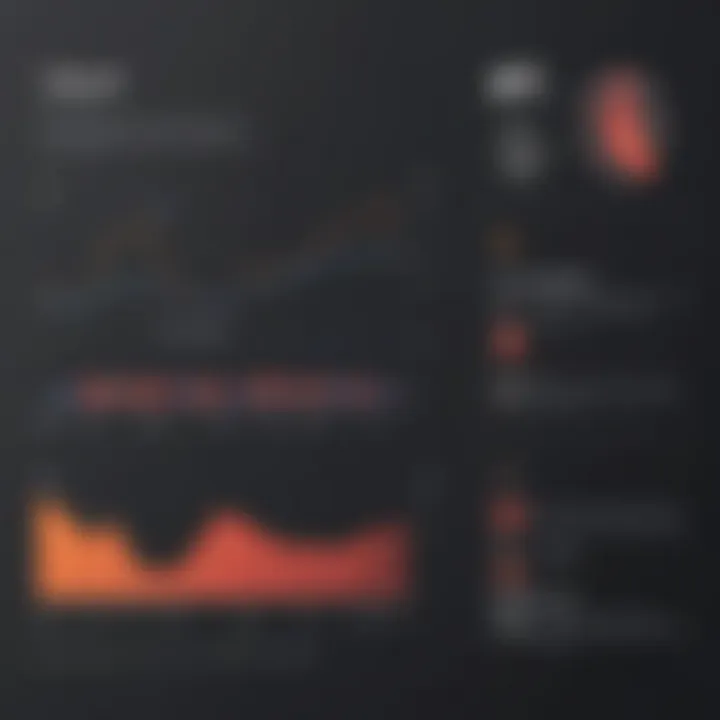
In the realm of brushless motors, the working principle stands as a fundamental pillar, dictating their efficiency and functionality within various technological applications. These motors operate based on electronic commutation rather than the physical brushes that are present in their brushed counterparts. This shift in operating principle allows brushless motors to exhibit higher efficiency, reduced maintenance requirements, and an extended lifespan. Understanding the working principle of brushless motors is crucial for grasping their versatile nature and exploring the advancements they bring to industries such as aerospace, electric vehicles, and industrial automation.
Electric Commutation
Role of Commutation
The role of commutation in brushless motors is to facilitate the switching of current direction in the motor windings at precise moments, ensuring continuous rotational motion. This process is essential for maintaining the optimal performance and efficiency of the motor, as it aligns the magnetic field produced by the stator with the rotor's position. Efficient commutation leads to smooth operation, minimal energy loss, and precise control of motor speed, making it a preferred choice for high-performance applications where accuracy is paramount.
Phases of Commutation
Phases of commutation in brushless motors refer to the sequence in which current is supplied to different motor phases to induce rotation. This coordinated phase energization ensures seamless torque production and smooth motor operation. By judiciously timing the currents in the motor phases, the rotational speed can be accurately controlled, contributing to the overall efficiency and effectiveness of the motor.
Timing Sequence
The timing sequence in brushless motors dictates when the commutation events occur during each electrical cycle, synchronizing the current flow with the rotor position. This precision timing is crucial for maintaining optimal motor performance, minimizing energy wastage, and preventing efficiency losses. The correct timing sequence ensures that the magnetic fields interact effectively between the rotor and stator, enabling efficient conversion of electrical energy into mechanical motion.
Comparison with Brushed Motors
In contrast to brushed motors, brushless motors offer superior efficiency, reduced maintenance needs, and an extended operational lifespan. The absence of physical brushes in brushless motors eliminates the source of friction and wear, leading to enhanced durability and reliability. The efficiency of brushless motors stems from their electronic commutation, which minimizes energy losses and maximizes power output, making them a preferred choice for applications requiring high performance and precision.
Brushless vs. Brushed: Maintenance
When comparing maintenance requirements, brushless motors outshine brushed motors due to their simplified design and reduced wear components. The absence of brushes eliminates the need for frequent replacement and maintenance, resulting in cost savings and heightened operational efficiency. Brushless motors offer a low-maintenance solution for continuous operation across various industries, contributing to their widespread adoption and acclaim.
Brushless vs. Brushed: Lifespan
The lifespan of brushless motors surpasses that of brushed motors significantly, owing to their design that minimizes mechanical wear and tear. With fewer moving parts and reduced frictional losses, brushless motors demonstrate exceptional longevity and reliability. This extended lifespan translates to improved operational sustainability and reduced downtime, making brushless motors an attractive choice for applications demanding robust performance and endurance.
Sensored vs. Sensorless Operation
The operation of brushless motors can be categorized into sensored and sensorless systems, each offering distinct advantages and considerations based on the application requirements and operational conditions. Sensors play a crucial role in detecting rotor position and enabling precise commutation, ensuring smooth motor operation and enhanced efficiency.
Use of Sensors in Brushless Motors
Sensored brushless motors utilize position sensors to determine the rotor's position and enable accurate commutation. This sensor feedback enhances motor control, reduces torque ripple, and improves overall operational stability. By incorporating sensors, brushless motors can achieve precise speed regulation and torque delivery, making them ideal for applications demanding high performance and accuracy.
Advantages of Sensorless Systems
Sensorless brushless motor systems offer simplified designs and lower costs by eliminating the need for external sensors. Through advanced algorithms and predictive modeling, sensorless systems can estimate rotor position and perform commutation without relying on physical sensors. This approach reduces complexity, increases system reliability, and enhances motor efficiency by optimizing control algorithms and responsiveness.
Challenges in Sensorless Operation
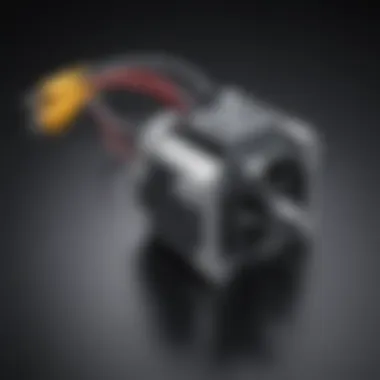
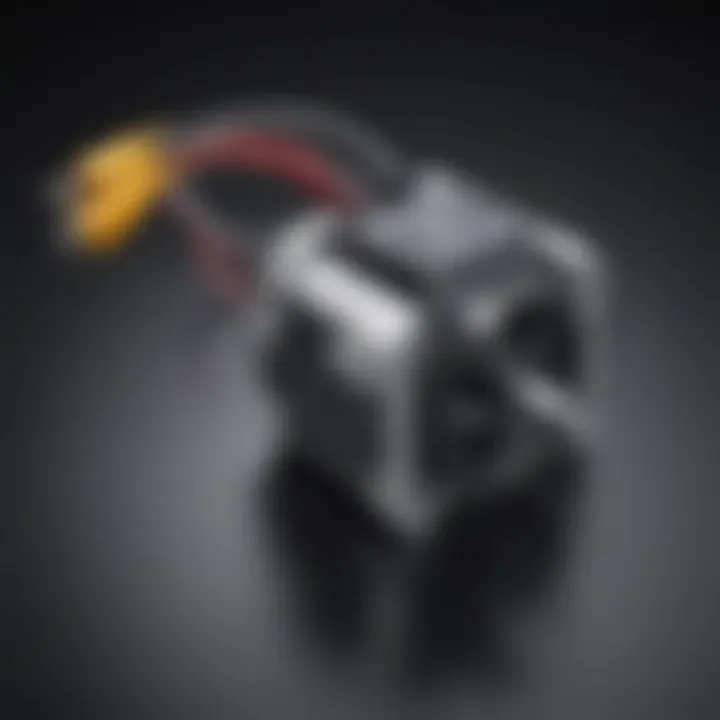
Despite their advantages, sensorless brushless motor systems face challenges in accurately determining rotor position in dynamic operating conditions. Variations in load torque, speed fluctuations, and environmental factors can impact the sensorless operation, affecting motor performance and efficiency. Developers continuously research and innovate sensorless control strategies to overcome these challenges and improve the robustness and reliability of sensorless brushless motor systems.
Performance Optimization Techniques
In the realm of brushless motors, performance optimization techniques play a pivotal role in enhancing the efficiency and functionality of these motors. By delving into advanced strategies, engineers and researchers can unlock the full potential of brushless motors in various applications. These optimization techniques focus on maximizing motor output, minimizing energy loss, and ensuring smooth operation, all crucial elements in improving overall performance.
Field-Oriented Control (FOC)
Principles of FOC
Field-Oriented Control (FOC) lies at the heart of optimizing brushless motor performance. It involves aligning the motor's electromagnetic field with a reference axis to achieve precise control over torque and speed. This method enhances efficiency by minimizing energy waste and improving dynamic response. The key characteristic of FOC is its ability to provide accurate control even at high speeds, making it a popular choice for applications requiring precise motor operation. Despite its advantages, FOC may introduce complexities in the control system, demanding careful tuning for optimal performance.
Enhancing Motor Efficiency
Enhancing motor efficiency is a critical aspect of performance optimization in brushless motors. By reducing losses through improved design and control algorithms, motor efficiency can be significantly boosted, leading to energy savings and enhanced overall system performance. The key characteristic of efficiency enhancement is the focus on reducing heat generation and mechanical frictions, resulting in a more sustainable and reliable motor operation. However, increasing efficiency may require sophisticated control strategies and advanced materials, adding complexity to the motor design process.
Implementation in Brushless Motors
The implementation of performance optimization techniques in brushless motors is essential for maximizing their capabilities. Integrating FOC and efficiency enhancement strategies into motor controllers allows for seamless operation and improved performance across various load conditions. The key characteristic of this implementation is the seamless integration of control algorithms and hardware components to achieve optimal motor output. While this integration enables superior efficiency and control, it also demands robust design practices and thorough testing to ensure reliable operation in real-world applications.
Pulse Width Modulation (PWM)
Regulating Motor Speed
Pulse Width Modulation (PWM) is a key technique in controlling motor speed in brushless motors. By modulating the width of electrical pulses to the motor, PWM systems can adjust the average voltage and control the rotational speed with precision. The key characteristic of PWM is its ability to deliver variable power to the motor, enabling smooth speed regulation and improved dynamic response. However, PWM may introduce voltage harmonics and increase electromagnetic interference, requiring proper filtering and shielding for reliable operation.
Efficiency Improvement
Efficiency improvement through PWM in brushless motors focuses on optimizing power distribution and reducing energy losses during operation. By synchronizing PWM signals with motor requirements, efficiency can be enhanced by minimizing idle currents and maximizing power delivery during active operation. The key characteristic of efficiency improvement is the fine-tuning of PWM parameters to match specific load demands, ensuring optimal energy utilization and overall system performance. Nevertheless, optimizing PWM for efficiency can be a challenging task, requiring in-depth knowledge of motor characteristics and control principles.
Effects on Motor Heat Generation
PWM systems influence motor heat generation by regulating the power input and controlling current flow. Efficient PWM strategies can minimize heat buildup by maintaining stable operating temperatures within the motor, prolonging its lifespan and improving reliability. The key characteristic of managing motor heat generation is to balance performance requirements with thermal management, ensuring optimal efficiency without compromising motor integrity. However, improper PWM implementation can lead to overheating and thermal stress, necessitating effective cooling mechanisms and thermal protection to safeguard the motor components.
Regenerative Braking
Energy Recovery Mechanism
Regenerative braking in brushless motors enables the recovery of energy during deceleration or braking actions. By converting kinetic energy into electrical energy, regenerative braking systems can reduce power consumption and increase overall system efficiency. The key characteristic of this mechanism is its ability to store and reuse braking energy, providing sustainability and cost-saving benefits in electric vehicle applications. However, implementing regenerative braking requires sophisticated control algorithms and energy management systems to optimize energy recovery and ensure seamless operation.
Impact on Battery Life
Regenerative braking systems have a significant impact on battery life in electric vehicles by reducing overall energy consumption and extending driving range. By capturing and storing energy during braking events, battery usage is optimized, leading to prolonged battery lifespan and improved vehicle efficiency. The key characteristic of this impact is the balance between energy regeneration and battery charging, ensuring efficient use of stored energy while maintaining battery health. Nonetheless, regenerative braking systems involve complex control strategies and battery management protocols to mitigate potential risks and optimize performance.
Implementation in Electric Vehicles
The implementation of regenerative braking in electric vehicles revolutionizes energy management and efficiency in transportation systems. By integrating regenerative braking systems with electric propulsion, vehicle manufacturers can enhance overall efficiency, reduce environmental impact, and improve driving dynamics. The key characteristic of this implementation is the harmonization of braking energy recovery with vehicle control systems, optimizing performance without compromising safety or comfort. However, integrating regenerative braking requires careful system design and calibration to achieve seamless operation and maximize the benefits of energy regeneration in electric vehicles.

