Mastering Preventive Maintenance: A Comprehensive Guide
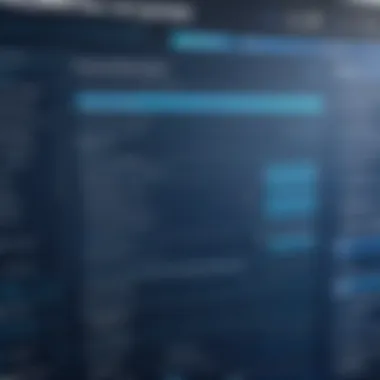
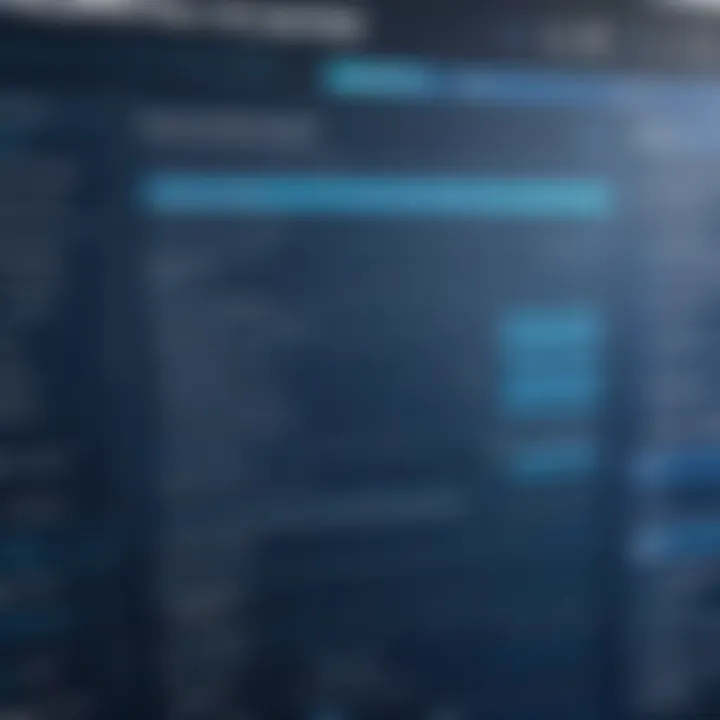
Overview of Topic
Prolusion to the main concept covered
Preventive maintenance is a strategic approach that focuses on preventing equipment failure through regular upkeep and careful inspection. This method involves scheduling maintenance before problems arise, ensuring that systems operate efficiently and minimizing unexpected downtime.
Scope and significance in the tech industry
In the technology sector, preventive maintenance is crucial. As systems become more complex, relying on reactive practices can lead to high costs and inefficient operations. For instance, regular updates and maintenance of software can extend its lifespan and enhance its performance. Moreover, the integration of IoT devices in various infrastructures allows for real-time tracking of equipment health, emphasizing the importance of a preventive maintenance program.
Brief history and evolution
Initially, maintenance practices were predominantly reactive in nature. Over time, industries recognized the need for more systematic approaches. The advent of lean manufacturing principles in the late 20th century brought attention to preventive measures within manufacturing sectors. Today, with advancements in technology and data analytics, preventive maintenance has evolved significantly, incorporating predictive insights for more effective management.
Fundamentals Explained
Core principles and theories related to the topic
Preventive maintenance relies on several fundamental principles. These include:
- Scheduled inspections: Regular checks are essential for identifying potential issues early.
- Data analysis: Collecting and analyzing data to foresee problems before they escalate.
- Standard procedures: Establishing clear protocols for maintenance tasks enhances consistency and quality control.
Key terminology and definitions
Understanding key terms improves clarity regarding preventive maintenance practices. Important terms include: -Downtime: Periods when a system is not operational due to failures or maintenance.
- Asset management: Comprehensive management service for organization assets to maximize value, including preventive measures.
- Lifecycle costs: Total cost of ownership over a product's lifespan, encouraging preventive practices to reduce costs.
Basic concepts and foundational knowledge
The principles of reliability engineering often inform preventive maintenance, pushing users to prioritize durability and functionality of equipment. The Goal is to ensure that machinery and systems maintain their performance while extending their usable life.
Practical Applications and Examples
Real-world case studies and applications
Numerous industries have benefitted from effective preventive maintenance strategies. For example, in the aviation field, airlines employ stringent maintenance protocols to comply with safety regulations, but it also aids in reducing unexpected issues, lowering repair costs, and ensuring passenger satisfaction.
Prevention is more effective than responding to failures. Establishing comprehensive preventive maintenance techniques results in performance improvements and flow efficiencies outcomes.
Demonstrations and hands-on projects
In the manufacturing sector, implementing a computerized maintenance management system (CMMS) can digitize maintenance schedules, assign tasks, and track progress effectively, thus simplifying the process of preventive maintenance. Furthermore, participating in workshops focusing on lean manufacturing principles offers opportunities to explore practical applications in various workplaces.
Advanced Topics and Latest Trends
Cutting-edge developments in the field
As technology advances, preventive maintenance incorporates more sophisticated tools. Artificial Intelligence and machine learning contribute to strategies that predict failures accurately through analysis of historical data, allowing for intelligent scheduling and improved resource allocation.
Advanced techniques and methodologies
Emerging methodologies include condition-based maintenance, wherein maintenance is performed based on observed conditions rather than a rigid timetable. This optimizes maintenance efforts and costs more efficiently.
Future prospects and upcoming trends
Going forward, the integration of augmented reality in trainings for technicians offers exciting prospects. This technology allows professionals to visualize systems and potential issues, thereby enhancing their understanding and implementation of preventive strategies. Increasing reliance on cloud-based maintenance systems will also solidify consistent access to data and analytics.
Tips and Resources for Further Learning
Recommended books, courses, and online resources
For those looking to expand their knowledge:
- โMaintenance Planning and Scheduling Handbookโ by Judy Freundeberg
- Online courses on platforms like Coursera or Udemy covering concepts of predictive and preventive maintenance methodologies.
Tools and software for practical usage
Consider utilizing software like IBM Maximo or UpKeep to manage your preventive maintenance activities more effectively. These tools streamline processes, providing alerts and enforcing efficient practices. Resources noted in platforms such as Wikipedia and Britannica can help deepen understanding of foundational principles.
Visit sites like Reddit for pertinent forums on maintenance strategies and problem-solving in various industries.
Understanding Preventive Maintenance
Preventive maintenance is often described but not always fully understood. To grasp its significance, one must look beyond mere terminology. Understanding preventive maintenance involves acknowledging its multifaceted nature and recognizing the roles it plays across different contexts. Basic concepts must be delineated from practical implications. This section dissects what preventive maintenance is, its crucial importance, and the industries it influences.
Definition of Preventive Maintenance
Preventive maintenance refers to the proactive approach in maintaining systems or equipment to reduce the probability of failure. In simpler terms, it is about conducting regular checks, servicing, and necessary repairs before equipment experiences a malfunction. This practice aims to ensure reliability and performance longevity without waiting for breakdowns. Details of this definition expand as one considers various organizations and contexts where maintenance occurs. Safe operating conditions in factories, technology setups, and facility management benefit profoundly from this strategy. Each context highlights a symbol of diligence, framing preventive maintenance not merely as a choice but as an intrinsic component for smooth operations.
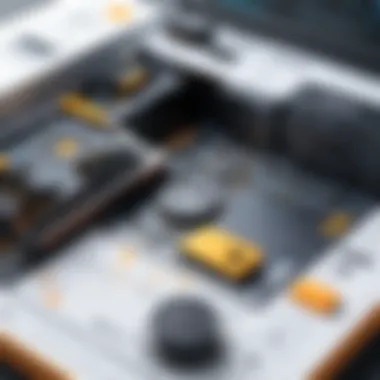
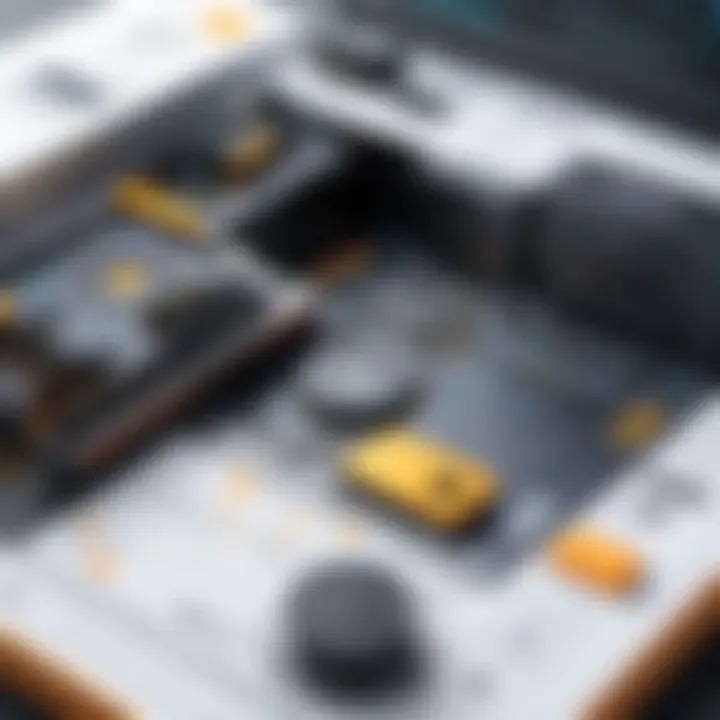
Importance of Preventive Maintenance
The significance of preventive maintenance can hardly be overstated. Apart from extending equipment life, it serves several critical purposes, such as:
- Risk Mitigation: Regular checks can uncover potential issues before they escalate, minimizing hazards to employees and assets.
- Cost Efficiency: By preventing major failures, organizations can avoid expensive repairs and unanticipated downtime.
- Enhanced Efficiency: Equipment running optimally is less likely to encounter disruptive issues, ensuring production aligns with timelines and expectations.
- Sustainability Initiatives: Being proactive often aligns with environmentally friendly practices, as timely maintenance can lower energy consumption.
Many professionals soon recognize that the cost of neglecting preventive measures outweighs investments on slight maintenance tasks. It is essential for workers to truly internalize the long-term vision of cost-effectiveness that effective maintenance brings.
Industries Benefiting from Preventive Maintenance
Multiple sectors gain from preventive maintenance strategies. Its reach spans broad territories, including:
- Manufacturing: Factories heavily depend on highly efficient machinery. Regular maintenance ensures these operations run seamlessly.
- Information Technology: Systems can function improperly without consistent maintenance checks. IT infrastructure management involves its own rigors of scheduled upkeep to facilitate smooth digital environments.
- Building Management: From HVAC systems to elevators, preventing issues in these vital areas contributes significantly to tenant satisfaction and safety.
- Transportation: Vehicles must undergo routine inspections for reliability and safety, reflecting the sheer importance of effective maintenance.
Overall, embracing preventive maintenance enables industries to optimize operations, longevity, and environmental goals, shaping a more reliable future no matter the area of application.
Key Components of Preventive Maintenance
Preventive maintenance is a comprehensive approach. Its success relies on several vital components. These are scheduled inspections, routine maintenance tasks, and effective resource allocation. Understanding each of these components critically enhances operational efficiency and extends the lifespan of equipment and resources.
Scheduled Inspections
Scheduled inspections form the backbone of any preventive maintenance plan. They are designed to regularly assess equipment's condition, identify potential issues, and promote timely actions. Structured inspection schedules help organizations maintain a proactive stance, diffusing the chances of unexpected failures.
Benefits of Scheduled Inspections
- Identify Issues Early: Regular assessments can unveil minor issues before they escalate into significant problems.
- Organized Workflow: Clearly defined schedules facilitate efficient tracking of maintenance activities and streamline workflow.
- Maximized Uptime: By knowing the status of equipment regularly, organizations can plan maintenance activities that minimize disruption to operations.
Engaging outputs from structured inspections can greatly impact resource allocation and task prioritization across teams. Overall, it promotes a healthier maintenance culture where decisions are made based on principles of engineering and operational data.
Routine Maintenance Tasks
Routine maintenance tasks translate the findings from inspections into actionable activities. These tasks may involve simple procedures like lubrication, cleaning, tightening connections, or more extensive undertakings based on specific machinery needs.
Importance of Routine Maintenance Tasks
- Consistency Matters: Regularly carried out routine tasks maintain operational efficiency. They ensure systems work as intended, reducing the risks of outages.
- Cost-Effective: Routine tasks often cost less than repairing or replacing equipment failures resulting from neglect.
- Employee Morale: An organization that prioritizes routine tasks sends a clear signal to staff about its commitment to operational stability.
Routine tasks must be documented and scheduled regularly to create a culture of accountability and transparency in maintenance operations.
Resource Allocation
Efficient resource allocation intersects with both inspection and maintenance activities. Proper deployment of people, tools, and materials enhances the effectiveness of preventive maintenance efforts. Understanding what is needed when and how is crucial for organizations aiming for maximum operational reliability.
Key Considerations in Resource Allocation
- Labor: Skilled technicians must be available to perform tasks. Assessing workforce capabilities is key to assigning the right personnel to tasks effectively.
- Tools and Supplies: Determining which tools, spare parts, or technology will be necessary ahead of time avoids delays during maintenance operations.
- Budgeting: Proper financial planning is crucial in supporting preventive maintenance actions. Investing in resources ensures continuous improvement in operational patterns.
A coherent approach to resource allocation consolidates every aspect of preventive maintenance practices. Optimally using resources leads to consistent performance and minimizes risks associated with reactive maintenance.
By focusing on these key components, organizations can develop a structured framework for preventive maintenance. This leads to optimized operations and enhanced long-term sustainability.
Crafting a Preventive Maintenance Plan
Crafting a preventive maintenance plan is essential for maximizing the efficacy of maintenance efforts. This plan serves as a structured approach to maintaining equipment and facilities, ultimately improving their reliability and functionality. A well-thought-out preventitve maintenance plan enables organizations to operate efficiently while minimizing unexpected breakdowns and extending asset lifespans.
Setting Maintenance Objectives
Establishing clear maintenance objectives lays the foundation for effective preventive maintenance. Organizations should identify goals that are aligned with overall business objectives. This might include increasing equipment uptime, reducing operational costs, and enhancing safety standards.
- Align with Business Goals: Ensure that maintenance objectives support key organizational targets. For instance, if a company aims to increase production quality, maintenance objectives should focus on equipment reliability and precision.
- Measurable KPIs: Define key performance indicators that help gauge success. Objectives can include metrics like mean time between failures (MTBF) and socio-economic benefits from reduced downtimes.
- Flexible Adaptations: The maintenance objectives must be adaptable to changing business environments and technologies. As businesses grow or technological innovations become available, revisiting these objectives is crucial.
Assessing Current Infrastructure
Assessing the current infrastructure is a vital step in crafting a preventive maintenance plan. This involves evaluating existing assets including equipment, facilities, and current maintenance procedures. Understanding the state of infrastructure aids in effective planning.
- Inventory and Condition Monitoring: Conduct a thorough inventory and evaluate the condition of each asset in your facility. Utilizing tools to monitor performance can supply valuable data for asset management.
- Weakness Identification: Pinpoint areas that require improvements. Identifying frequently problematic equipment highlights what needs special attention during maintenance.
- Regulatory Compliance Assessments: Be aware of compliance standards in the industry. Regular evaluations ensure that the infrastructure meets necessary environmental and safety standards, avoiding costly penalties.
Developing a Maintenance Schedule
A well-structured maintenance schedule fosters regular maintenance activities and ensures that equipment is serviced promptly. This schedule is critical in maximizing efficiency and minimizing unexpected failures.
- When to Schedule tasks: Tasks should be scheduled based on manufacturers' recommendations, historical performance data, and usage cycles.
- Allocation of Resources: Build a realistic schedule that takes into account available workforce and tools necessary for maintenance tasks.
- Flexibility is Key: Allow for modifications in the schedule as new information about equipment performance comes to light. Flexibility empowers a quick response to equipment modifications or technological advancements.
Crafting an effective maintenance plan requires continuous assessment, flexibility, and clear communication among all involved parties.
By focusing on these elements, organizations can create tailored preventive maintenance plans that support sustainable operational practices.
Tools and Technologies for Preventive Maintenance
Preventive maintenance relies on various tools and technologies that streamline and optimize maintenance processes. Employing the right technology can enhance operational efficiency, reduce downtime, and ensure longevity of assets. There's a multitude of tools available that cater specifically to preventive maintenance needs, apropriating different sectors like manufacturing, IT, and facilities management. Proper integration of these technologies not only enhances control over maintenance tasks but also mitigates risks associated with asset failure.
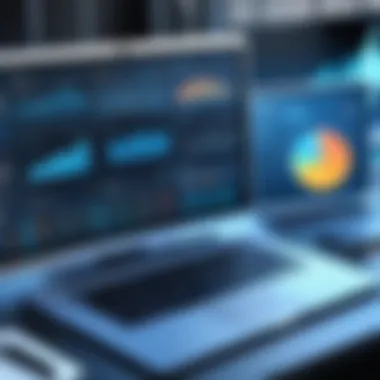
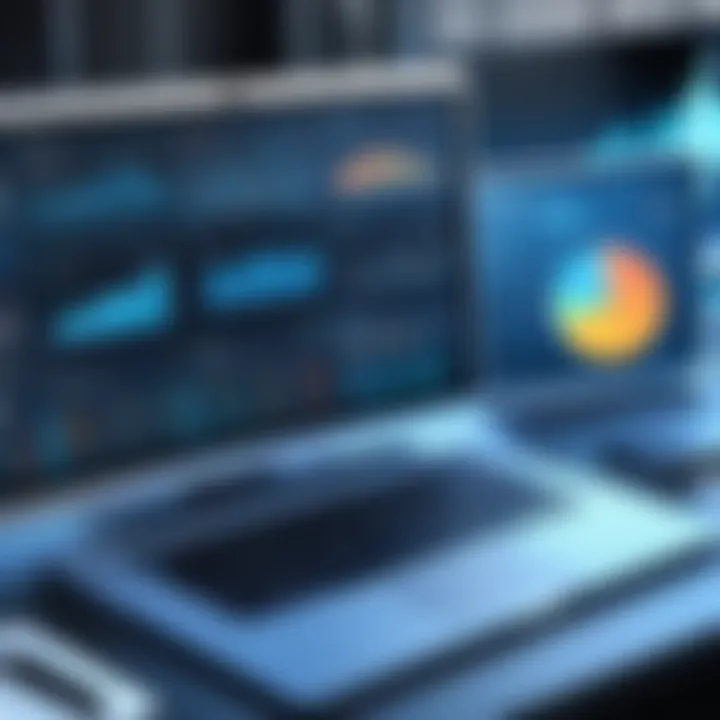
CMMS Software Overview
Computerized Maintenance Management Systems (CMMS) play a pivotal role in the orchestration of preventive maintenance tasks. This software mitigates manual logging and increases the efficiency of maintenance teams. Centralizing information within a CMMS allows organizations to access maintenance logs, schedules, and inventory easy.
Key features of CMMS include:
- Work Order Management: Assign, track, and close work orders efficiently.
- Asset Management: Have a clear overview of asset life cycles and maintenance histories.
- Reports and Analytics: Generate reports that provide insights into maintenance operations.
With a CMMS in place, user can foresee equipment failure through established maintenance tracking. This brings faster response times for repairs are planned ahead of time. Implementing CMMS forms the backbone of a structured preventive maintenance program.
Utilizing IoT in Maintenance
The Internet of Things (IoT) presents revolutionary opportunities in preventive maintenance by connecting devices and sensors across facilities. This technology facilitates real-time monitoring which significantly improves maintenance decision-making processes. Using IoT devices, it is possible to:
- Gather Data: Collect valuable operational data from equipment and machinery.
- Detect Anomalies: Identify performance anomalies before they lead to failures.
- Predict Maintenance Needs: Deploy predictive maintenance plans based on data analysis.
For example, vibrations or temperature anomalies can trigger alerts to maintenance personnel. This leads to precise adjustments instead of reactive measures.
Data Analytics for Predictive Insights
Using data analytics enhances the preventive maintenance landscape. By studying complex datasets around asset performance, organizations can extract meaningful patterns and trends. Predictive analytics assists in
- Identifying Trends: Allows forecasting potential breakdowns by analyzing past performance data.
- Improving Reliability: Regular insights lead to improved planning and less downtime.
- Cost Reduction: Discovering insights often unearths areas for cost savings.
In the current maintenance environment, the significance of predictive analytics grows as organizations seek efficiency in resources. Robust data analytics not only underpins maintenance efforts but also aligns with overall strategic goals.
In summary, the integration of tools such as CMMS, IoT devices, and advanced data analytics empowers companies to make determinations decisively. Through thoughtful application of these technologies, preventive maintenance can thrive in any industry, avoiding hasty fixes and fostering long-term operational success.
Executing Preventive Maintenance Tasks
Executing preventive maintenance tasks is crucial for maintaining operational efficiency and ensuring longevity of equipment and systems. These tasks encompass a wide range of duties that must be carried out systematically to avoid unexpected failures, thus reducing downtime and preserving resources.
Training Personnel
To ensure effective execution of these maintenance tasks, thorough training of personnel is essential. Workers must fully understand processes and procedures tied to equipment maintenance. Proper training can include:
- Hands-on workshops to familiarize personnel with equipment operation.
- Safety protocols to minimize accidents due to improper handling or negligence.
- Regular refreshers to keep skills sharp and up-to-date with the latest technologies.
Limited training can lead to mistakes. Ultimately, this impacts the productivity of the tasks completed. An invested workforce is more likely to embrace preventive maintenance as a norm, resulting in improved operational efficiency and goal achievement.
Tracking Maintenance Progress
Monitoring the progress of maintenance tasks is another key component in executing these responsibilities successfully. It enables organizations to:_
- Measure the effectiveness of the strategies implemented.
- Identify bottlenecks that may impede timely repairs.
- Maintain an accurate schedule of upcoming tasks.
Modern tools like computerized maintenance management systems (CMMS) provide detailed insights into what tasks have been completed and the their current status. By regularly reviewing these records, teams can adjust strategies for maximum efficiency. Furthermore, engaging in consistent progress tracking nurtures accountability among workers and fosters a culture of responsibility.
Documentation and Reporting
Proper documentation and reporting cannot be overlooked in the realm of preventive maintenance. Keeping detailed and updated records about performed maintenance provides several distinct benefits:
- Assurance that every task is performed correctly and comprehensively.
- Facilitation of audits and compliance with industry standards.
- Support for future planning based on historical data and trends.
Routine documentation activities should include:
- Creating service reports post-inspection or repair.
- Keeping logs of equipment performance and any changes noted.
- Compiling inventories of spare or replacement parts.
Additionally, establishing regular reporting structures ensures that all involved parties remain informed of maintenance status and issues, promoting transparency. Such practices even contribute to recognizing opportunities for improvements in maintenance strategies, supporting an continuous evaluative cycle that directly benefits overall operational goals.
Regular and rigorous documentation bolsters an organization's operational stability by solidifying knowledge transfer across teams.
Evaluating Preventive Maintenance Effectiveness
Evaluating the effectiveness of preventive maintenance is a crucial aspect of ensuring that maintenance strategies are achieving desired outcomes. This evaluation not only influences operational efficiency but also can impact overall productivity and cost savings. The process requires a systematic approach to measuring the impact of preventive maintenance initiatives.
When organizations evaluate preventive maintenance effectiveness, they can identify specific areas where improvements are necessary. This step helps to strengthen the maintenance framework and further contributes to achieving business goals.
Key Performance Indicators (KPIs)
In evaluating the effectiveness of preventive maintenance, Key Performance Indicators (KPIs) serve as measurable values that demonstrate how effectively maintenance goals are being achieved. These indicators can provide insights into various aspects of maintenance performance. Some common KPIs include:
- Mean Time Between Failures (MTBF): Measures the average time duration between system failures. A higher MTBF indicates effective preventive maintenance strategies.
- Percent of Planned Maintenance Compliance: This reflects the ratio of completed planned maintenance tasks to scheduled tasks. High compliance rates suggest an effective preventive maintenance system.
- Maintenance Cost per Unit of Production: This KPI provides insights into the cost-effectiveness of maintenance strategies.
By tracking these indicators over time, organizations can better assess the return on investment (ROI) of preventive maintenance practices.
Regular Review Meetings
Conducting regular review meetings plays an instrumental role in evaluating effectiveness. These meetings provide a structured environment to assess performance against set goals. Participants may include maintenance teams, management, and related departments who have a stake in maintenance operations.
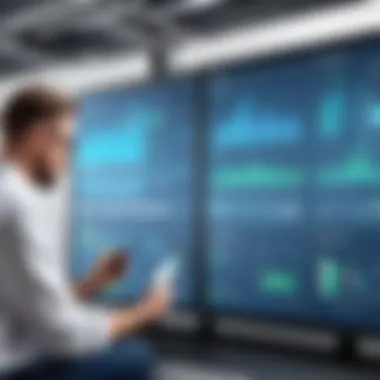
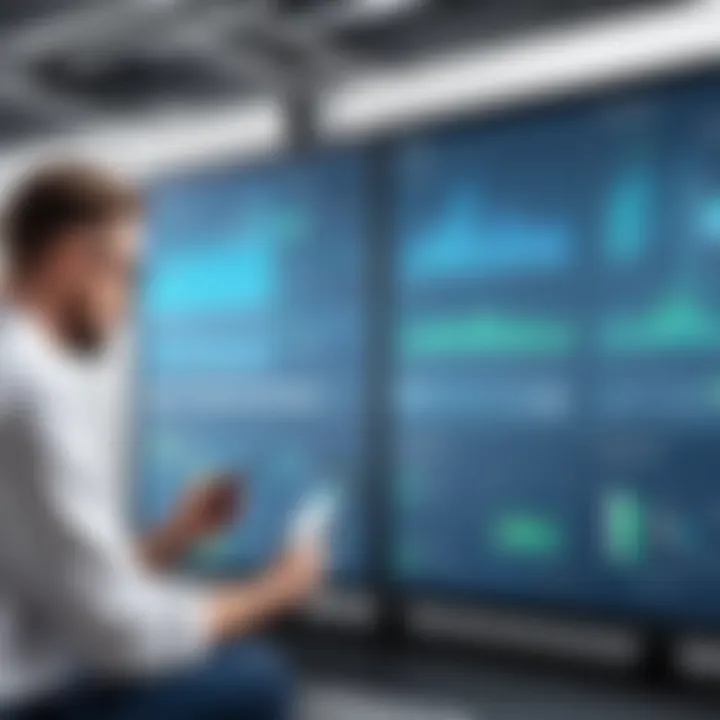
In these meetings, the discussion often centers around:
- Current performance metrics
- Challenges and barriers identified
- Areas of improvement
Meeting regularly also ensures a continuous feedback loop, allowing for agility in strategies and priorities. It fosters a culture where communication and collaboration can thrive, leading to enhanced effectiveness in preventive maintenance initiatives.
Continuous Improvement Strategies
Continuous improvement strategies are essential to adapt maintenance practices over time. Once evaluated, it becomes evident where adjustments need to be made. Techniques that organizations might employ include:
- Lean Principles: This involves streamlining processes to eliminate waste and ensure each maintenance task adds value.
- Root Cause Analysis (RCA): RCA helps identify the primary causes of failures so that maintenance can be more targeted.
- Feedback Systems: Constructing avenues for team members to provide input can unearth insights that quantifiable metrics might miss.
By focusing on continuous improvement, organizations can refine preventive maintenance strategies and perhaps discover additional benefits that were previously unnoticed. Maintaining this focus contributes to sustainability and allows for better resource allocation.
The way an organization evaluates and adapts its preventive maintenance practices will have long-lasting impacts on productivity, equipment longevity, and operational costs.
Challenges in Preventive Maintenance Implementation
Preventive maintenance is crucial for enhancing operational efficiency. However, its implementation is not without challenges. Understanding these obstacles helps organizations devise strategies to overcome them. Identifying and addressing these challenges can lead to a smoother transition into effective maintenance practices.
Resistance to Change
Resistance to change often emerges as a fundamental barrier. Employees may be accustomed to reactive maintenance approaches. Adjusting to a preventive mindset requires cultural shifts within the organization. Many may fear disruption in their workflows or doubt the necessity of new practices. To handle this, training sessions that articulate the benefits can be effective.
Choosing champions among staff to advocate for preventive maintenance can also help. These advocates should communicate the benefits clearly to their peers with concrete data on savings and efficiency improvements. Googleโs implementation of preventive practices illustrates this momentum carried through employee engagement. Organizations face competition from inertia whenever this transition occurs.
Resource Limitations
Resource limitations frequently hinder the effective rollout of preventive maintenance. Organizations may lack the necessary funds to invest in tools or hardware that facilitates maintenance. Often, budget constraints dictate how maintenance is perceived and managed.
To counter this limitation, a comprehensive analysis of expenses needs to be undertaken. Using existing resources wisely is critical. Companies should consider allocating funds to software tools like Computerized Maintenance Management Systems (CMMS), which often reduce overall operational costs long-term. Few facilities may think they cannot afford a preventive strategy, missing the big picture of cost-effectiveness.
Inadequate Training
Inadequate training is another pressing challenge in preventive maintenance. Staff must understand both the practices and technologies involved. Without this education, any initiative deployed will lack the effectiveness needed to yield results.
Creating an ongoing education program is one way to ensure employees are prepared. This program should encompass familiarity with tools, techniques, and maintenance goals. Targeted โrefresherโ training can also be instrumental as something like predictive analytics is gained by using analytics tools to anticipate equipment needs.
In summary, overcoming challenges related to resistance to change, resource limitations, and inadequate training is necessary to implement preventive maintenance successfully. Organizations can achieve long-lasting improvements and prove return on investment through thoughtful strategies. Ultimately, entirely realizing preventive maintenance's benefits involves commitment from all levels of the organization.
Future Trends in Preventive Maintenance
The landscape of preventive maintenance is changing rapidly. As technology evolves, businesses are poised to integrate sophisticated systems that refine and evolve traditional methods. The importance of staying updated with these emerging trends cannot be overstated. They promise enhanced efficiency, better resource management, and new avenues for sustainability. Understanding these trends equips organizations to maintain competitive advantage and align maintenance strategies to modern expectations.
Artificial Intelligence Applications
Artificial intelligence (AI) is transforming many sectors, and preventive maintenance is no exception. AI applications can analyze vast amounts of data to predict when equipment is likely to fail. This forecast is based on real-time metrics, identified patterns, and historical data.
- Predictive Maintenance: AI tools help shift the focus from reactive to predictive maintenance. In such models, potential system failures can be anticipated, allowing timely interventions that prevent downtime. This can result in significant cost savings and optimizes resource use.
- Automated Decision Making: Using machine learning algorithms can enhance decision-making frameworks. This ensures that alerts are provided only for critical issues, eliminating unnecessary disruptions in operations.
The integration of AI can fundamentally change maintenance work. Increased coordination and timely action based on data can lead to smoother organizational workflows.
New efficiencies not only enhance output, but also stress reducing roles, enhancing employee satisfaction.
Integration with Smart Technologies
Smart technologies, including IoT (Internet of Things), enable real-time monitoring and data collection. This technological integration is essential in crafting an efficient preventive maintenance environment.
- Connected Devices: Equipment fitted with smart sensors can communicate with management systems. This communication allows instant detection of anomalies.
- Mobile Guidance: Faced with troubleshooting tasks, workers can receive direct guidance through mobile applications from other experienced staff. Such tools increase productivity while fulfilling maintenance tasks efficiently.
Utilizing smart tech acts as a catalyst for efficient asset management. The timely data can be actionable, allowing decision-makers to frame responsive strategies.
Sustainability and Green Practices
In recent years, sustainability has gained prominence across sectors. Integrating eco-friendly practices into preventive maintenance is essential. Taking a sustainable approach helps meet not just regulatory demands but also corporate social responsibilities.
- Energy Efficiency: Implementing energy-efficient solutions during maintenance can reduce overall operational costs. This leads to waste minimization and diminishes the environmental impact.
- Material Management: Placing actions on utilizing eco-friendly materials for routine maintenance not only encourages sustainability but can also enhance safety and longevity in systems.
Integrating sustainability into maintenance practices not only shows that the organization is conscious of its footprint but also reinforces brand integrity. As consumer preferences shift towards environmentally-friendly solutions, so does the competitive edge.
Overall, staying attuned to future trends in preventive maintenance is critical. These advances drive organizational shifts, meeting the demands for efficiency, smart tech integration, and progressively sustainable practices. Businesses equipped with such practices are well-positioned for future challenges and opportunities.
Epilogue
In the realm of preventive maintenance, one must always reflect on its crucial role. This outlook enables professionals in technology, manufacturing, and facility management to grasp every aspect of preventive practices thoroughly. Each topic discussed throughout this guide not only highlights the strategies involved in maintenance but also underlines their lasting benefits.
The importance of a well-structured preventive maintenance program cannot be overstated. Consistent execution of tasks leads to enhanced operational efficiency. Moreover, systematic inspections and tasks preempt unexpected equipment failures. Less downtime translates into higher productivity. This becomes particularly critical in industries where each minute of delay can be costly.
Key elements that emerge from our discussion include:
- Cost-effectiveness: Preventive maintenance often results in lower overall operational costs. Regular and efficient maintenance limits unplanned repairs, which can be financially burdensome.
- Sustainability: Strategies adopted can also contribute to environmentally friendly practices. By extending equipment life and reducing waste, companies actively participate in promoting sustainability.
- Employee Safety: A maintained workplace inevitably aligns with a safer environment. By ensuring all equipment is functioning properly, the risk of accidents declines.
Considering the aforementioned points, industries that value long-term stability should highlight preventive maintenance in their operational strategies. Properly integrating tools, technologies, and trained personnel will yield a robust system, making maintenance repeating tasks more predictable and efficient. Continuous evaluation and improvement can lead to substantial advancements, ensuring that companies remain competitive and resilient in evolving landscapes.
As technology progresses, organizations should embrace the future trends identified, from Artificial Intelligence applications to the integration with smart technologies. Staying informed and proactive ensures not just the longevity of resources, but is, indeed, a prerequisite for future success, ultimately fostering the goal of producing highly efficient operations in any field.
Adopting a systematic preventive maintenance approach is not just an operational strategy; it is a comprehensive philosophy for sustained success.