Strategically Crafting an Optimized Warehouse Task List for Enhanced Operations
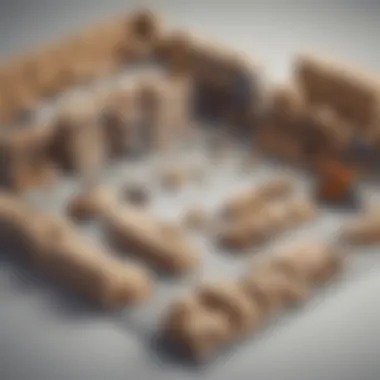
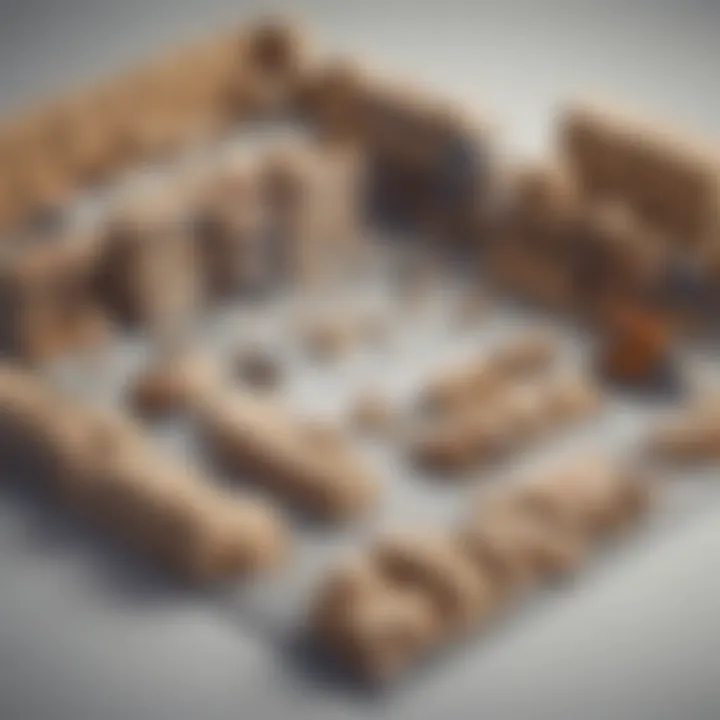
Overview of Topic
In the realm of warehouse management, one pivotal element stands out above all - the meticulous optimization of the warehouse task list. At its core, this process is indispensable for bolstering operational efficiency within any warehouse operation. By delving into the intricacies of creating a well-structured task list, organizations can revamp their daily operations, amplifying productivity and fostering seamless workflows on a day-to-day basis.
Fundamentals Explained
When embarking on the journey of warehouse task list optimization, it is imperative to grasp the foundational principles that underpin this crucial process. Key terminology like task prioritization, inventory management, and workflow optimization serve as the building blocks for a well-tailored task list. Understanding these fundamental concepts is akin to laying a sturdy foundation for the efficiency-enhancing edifice of warehouse operations.
Practical Applications and Examples
Real-world applications serve as the litmus test for the efficiency of any theory or concept. Exploring case studies where optimized task lists have revolutionized warehouse procedures sheds light on the tangible benefits of implementing such strategies. From hands-on projects to insightful demonstrations, witnessing these applications in action provides a practical blueprint for those aiming to streamline their warehouse tasks.
Advanced Topics and Latest Trends
Venturing into the cutting-edge realm of warehouse management uncovers a plethora of advanced techniques and methodologies. Examining the latest trends in task list optimization unveils futuristic prospects within the industry. By staying abreast of these developments, practitioners can position themselves at the vanguard of warehouse operational efficiency, ready to embrace the evolving landscape with acumen and innovation.
Tips and Resources for Further Learning
For individuals seeking to deepen their knowledge and proficiency in warehouse task list optimization, a treasure trove of resources awaits. From recommended books elucidating strategies for effective task prioritization to online courses offering insights into software tools tailored for practical implementation, the avenues for further learning are boundless. Equipping oneself with these resources ensures a continuous evolution towards mastering the art of operational efficiency in warehouse management.
Introduction
In the realm of warehousing operations, the significance of a well-structured and optimized task list cannot be overstated. A warehouse task list serves as the backbone of daily activities, orchestrating the movement of goods, guiding order fulfillment, and ensuring streamlined logistics processes. By comprehensively organizing tasks and establishing priorities, a warehouse task list lays the foundation for operational efficiency, productivity enhancement, and overall cost-effectiveness within the warehouse ecosystem. It acts as a directive compass, mapping out the intricate web of responsibilities that need to be executed with precision and accuracy.
Understanding the Significance of a Warehouse Task List
As we delve deeper into comprehending the importance of a warehouse task list, it becomes apparent that this fundamental tool embodies the essence of operational efficiency. A warehouse task list not only outlines the tasks to be accomplished but also elucidates the sequence and priority in which these tasks should be carried out. By delineating a clear roadmap for daily activities, a well-crafted task list minimizes downtime, reduces errors, and optimizes resource utilization. Moreover, it fosters organizational agility by enabling quick adaptability to changing demands and priorities, ensuring that the warehouse functions like a well-oiled machine.
Overview of the Article
This article embarks on a comprehensive exploration of optimizing warehouse task lists to elevate operational effectiveness and efficiency. Through a detailed analysis of essential elements, implementation of task prioritization techniques, utilization of technological advancements, and strategies for workflow enhancement, the article aims to equip readers with a holistic understanding of warehouse task optimization. By exemplifying the significance of accuracy and quality control, the article elucidates the pivotal role of a meticulously crafted task list in guaranteeing seamless operations and customer satisfaction. Readers are guided through a journey that encapsulates the essence of strategic warehouse management, with a keen focus on enhancing productivity and maximizing outcomes in a dynamic warehouse environment.
Essential Elements of a Warehouse Task List
The core of efficient warehouse operations lies in the formulation of a robust warehouse task list. This section delves into the fundamental components that constitute the backbone of a well-structured warehouse task list, crucial for maximizing operational efficiency and productivity. By encompassing essential elements such as inventory management, order processing, and logistics and shipping, this article will elucidate how these components synergize to streamline workflows and optimize task prioritization techniques.
Inventory Management
Tracking Stock Levels:
In the realm of inventory management, tracking stock levels assumes a paramount role in facilitating smooth warehouse operations. By meticulously monitoring stock levels, warehouses can ensure adequate inventory levels, prevent stockouts, and optimize storage capacity. The accuracy and timeliness of tracking stock levels enhance inventory control, enabling warehouses to meet customer demands efficiently and prevent supply chain disruptions.
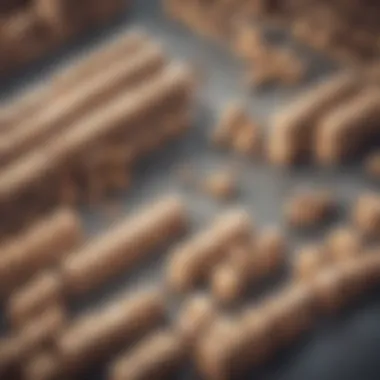
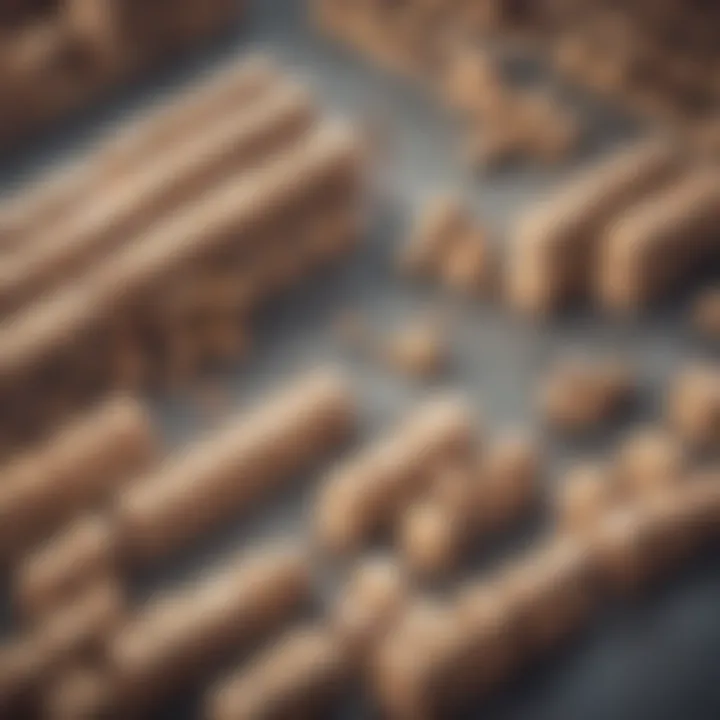
Key characteristics: Real-time visibility into stock levels, automated inventory tracking systems.
Unique feature: Just-in-Time replenishment, minimizing excess inventory costs.
Organizing Inventory:
Efficiently organizing inventory is a cornerstone of effective warehouse management. Proper inventory organization enhances accessibility, reduces picking and packing time, and minimizes errors in order fulfillment. By categorizing items based on demand, seasonality, or storage requirements, warehouses can optimize space utilization and enhance inventory turnover rates.
Key characteristics: ABC classification, SKU rationalization, efficient slotting strategies.
Unique feature: Cross-docking facilities, facilitating rapid order processing and shipment consolidation.
Order Processing
Receiving Orders:
The seamless processing of incoming orders is integral to fulfilling customer requests promptly. An efficient order receiving process involves inspecting, validating, and routing orders to ensure accuracy and expedited processing. By streamlining order intake procedures, warehouses can minimize order processing times and enhance order fulfillment efficiency.
Key characteristics: Order verification protocols, automated order capture systems.
Unique feature: Dock appointment scheduling, optimizing inbound logistics operations.
Picking Items:
Picking items from inventory shelves is a critical aspect of order fulfillment tasks. The accuracy and speed of item picking significantly impact order accuracy rates and operational efficiency. Implementing efficient picking strategies, such as zone picking or batch picking, can reduce travel distances and optimize picking processes.
Key characteristics: Pick-to-light systems, voice-directed picking technologies.
Unique feature: Pick path optimization algorithms, further enhancing picker productivity.
Packing Orders:
The final stage of order processing, packing orders, entails careful packaging of items for shipment. Well-organized packing processes ensure product safety during transit, minimize packaging wastage, and enhance brand reputation. Utilizing sustainable packaging materials and efficient packing techniques can streamline order packing operations.
Key characteristics: Packing slip verification, weight verification processes.
Unique feature: Automated packing stations, increasing packing speed and accuracy.
Logistics and Shipping
Coordinating Deliveries:
Efficient coordination of deliveries is essential for timely and cost-effective order fulfillment. Synchronizing delivery schedules, optimizing route planning, and managing carrier relationships are critical aspects of efficient logistics coordination. By minimizing delivery lead times and transportation costs, warehouses can enhance customer satisfaction and operational effectiveness.

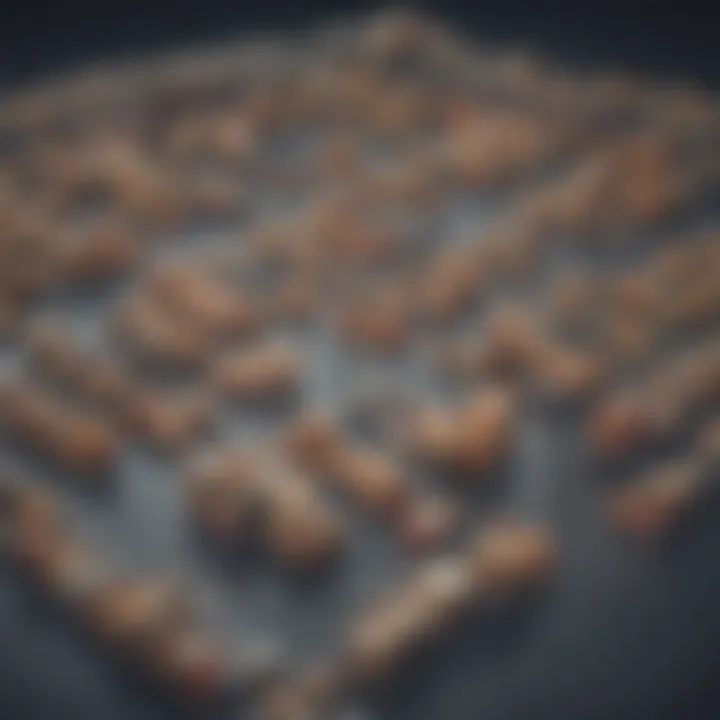
Key characteristics: Route optimization software, delivery tracking systems.
Unique feature: Dynamic routing algorithms, adapting to real-time traffic conditions for optimal delivery routes.
Shipping Products:
The culmination of the order processing cycle, shipping products involves packaging orders for shipment and coordinating outbound logistics. Optimal shipping strategies encompass selecting appropriate carriers, determining shipping modes, and verifying shipment accuracy. By integrating shipping technologies and streamlined processes, warehouses can expedite order dispatch and enhance shipping efficiency.
Key characteristics: Carrier rate comparison tools, multi-carrier shipping solutions.
Unique feature: Real-time shipment tracking, providing customers with visibility into shipment statuses for increased transparency.
Implementing Task Prioritization Techniques
In the realm of warehouse management, implementing task prioritization techniques stands out as a critical aspect that significantly impacts operational efficiency and overall performance. By delving into this area, organizations can strategically organize their workflows, optimize resource allocation, and enhance productivity levels. The process of task prioritization involves identifying key tasks, categorizing them based on importance, urgency, or other relevant factors, and allocating resources accordingly. This systematic approach helps in ensuring that essential tasks are given precedence, leading to smoother operations and better outcomes.
ABC Analysis
ABC analysis is a valuable technique within inventory management that classifies items into three categories: A, B, and C based on their contribution to overall value. Category A typically includes high-value items that contribute significantly to revenue generation, while Category C comprises low-value items with minimal impact. By conducting an ABC analysis, organizations can prioritize their inventory management efforts, focusing on the most critical items to optimize handling, storage, and replenishment processes. This method aids in streamlining operations, reducing costs, and improving overall efficiency within the warehouse environment.
Just-in-Time (JIT) Inventory Management
Just-in-Time (JIT) inventory management is a strategy that emphasizes the delivery of goods and materials exactly when they are needed in the production process. This approach seeks to minimize inventory holding costs, reduce waste, and enhance overall operational efficiency by synchronizing supply with demand. By adopting JIT principles, warehouses can enjoy improved resource utilization, shorter lead times, and a more responsive production cycle. However, JIT implementation requires close collaboration with suppliers, robust logistical support, and efficient order processing systems to ensure seamless operations.
First In, First Out (FIFO) Method
The First In, First Out (FIFO) method is a fundamental inventory management principle that dictates that the first items received or produced should be the first ones used or sold. This method is particularly crucial in industries where product expiry and obsolescence are key concerns, such as food and pharmaceutical sectors. By following the FIFO approach, warehouses can minimize the risk of product spoilage, reduce carrying costs, and maintain stock freshness. Implementing FIFO principles necessitates meticulous stock rotation, accurate tracking systems, and strict adherence to inventory policies to guarantee product quality and regulatory compliance.
Utilizing Technology for Task Optimization
In this digital era, the incorporation of technology is paramount for enhancing operational efficiency and productivity in warehouse management. When delving into the realm of Utilizing Technology for Task Optimization within the context of warehouse operations, several specific elements come into play. Firstly, the implementation of Warehouse Management Systems (WMS) revolutionizes how warehouses operate by providing real-time visibility into inventory levels, order processing, and logistics. WMS streamlines workflows, minimizes errors, and increases accuracy in managing inventory and fulfilling orders. Secondly, Automation and Robotics introduce advanced solutions that automate repetitive tasks, such as goods movement and sorting, leading to significant time and cost savings. Robotics not only accelerates process speeds but also reduces human intervention, thereby enhancing efficiency while ensuring precision in warehouse operations. Lastly, Barcode Scanning and RFID technologies offer accurate and efficient identification and tracking of inventory items. By utilizing barcodes and RFID tags, warehouses can rapidly locate products, monitor stock levels, and facilitate quick order processing, thus optimizing workflow management and boosting overall operational performance.
Warehouse Management Systems (WMS)
Within the spectrum of technology integration for warehouse optimization, Warehouse Management Systems (WMS) play a pivotal role. WMS software empowers warehouse managers with comprehensive tools to oversee inventory, orders, and shipments seamlessly. The significance of WMS lies in its ability to automate tasks, such as order processing and inventory tracking, improving accuracy and efficiency significantly. By centralizing data and operations, WMS enhances decision-making processes, optimizes inventory control, and streamlines warehouse workflows. Integration of WMS also enables real-time monitoring of inventory movements, enabling quick adjustments to inventory levels and order fulfillment procedures to meet customer demands effectively.
Automation and Robotics
Automation and Robotics represent groundbreaking technologies reshaping warehouse operations. The utilization of automation, such as automated guided vehicles (AGVs) and robotic arms, enhances the speed and precision of tasks like picking, packing, and stacking in warehouses. These technologies reduce manual errors, minimize operational downtime, and increase output capacities. The integration of Robotics in warehouse tasks ensures consistent performance levels, especially in repetitive and labor-intensive processes, leading to enhanced operational efficiency and cost savings. By automating routine tasks, warehouses can redirect human resources to more strategic functions, promoting a streamlined and agile operational environment.
Barcode Scanning and RFID
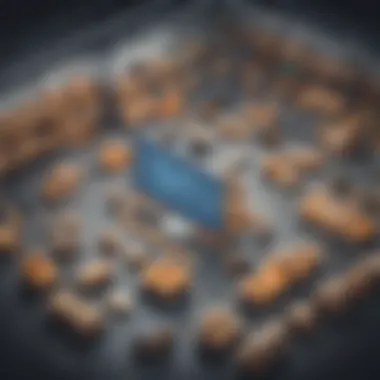
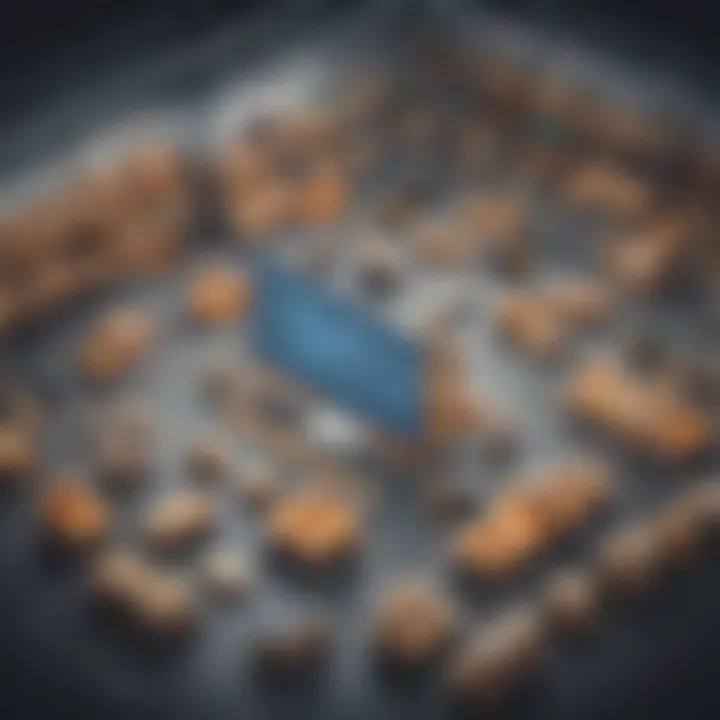
Barcoding and Radio-Frequency Identification (RFID) technologies are instrumental in improving inventory visibility and accuracy in warehouse settings. Barcode scanning allows for rapid and error-free data capture during receiving, picking, and shipping processes. The use of barcode scanners eliminates manual entry errors, expedites order processing, and enhances inventory traceability. Similarly, RFID technology enables real-time tracking of inventory movements throughout the warehouse, leading to enhanced inventory control and minimized stockouts. The integration of Barcode Scanning and RFID systems in warehouse operations optimizes inventory management, reduces operational costs, and improves overall productivity and customer service levels.
Optimizing Workflow Efficiency
Optimizing workflow efficiency is a paramount aspect in the domain of warehouse operations, where meticulous planning and execution can significantly impact productivity and resource utilization. By streamlining processes, minimizing wastage, and maximizing output, companies can enhance the overall efficiency of their operations. This section delves into the crucial strategies for optimizing workflow efficiency within a warehouse setting, shedding light on the key elements that contribute to a well-oiled operational process.
Streamlining Processes
Batching Orders
Batching orders is a strategic approach aimed at consolidating similar tasks or orders into groups, thereby streamlining the fulfillment process. By grouping together orders with similar attributes or delivery destinations, warehouses can minimize unnecessary back-and-forth movements, optimize picking routes, and reduce the overall time spent on fulfilling orders. This method is especially beneficial for warehouses dealing with a high volume of orders, as it allows for efficient handling and processing, leading to increased productivity and reduced operational costs.
Minimizing Travel Time
The strategy of minimizing travel time focuses on reducing the distance traveled by warehouse staff or automated systems during order fulfillment. By organizing storage locations based on demand frequency, implementing efficient picking paths, and utilizing technology such as conveyor belts or automated guided vehicles, warehouses can significantly cut down on the time spent moving between different points within the facility. By minimizing travel time, warehouses can boost order processing speed, decrease operational bottlenecks, and ultimately enhance overall workflow efficiency.
Employee Training and Empowerment
To ensure optimal operational performance, warehouses should invest in comprehensive training programs for their staff. By equipping employees with the necessary skills, knowledge, and confidence to execute tasks efficiently, companies can enhance operational productivity and accuracy. Empowering employees to make decisions, troubleshoot problems, and contribute ideas for process improvement fosters a culture of continuous learning and adaptation within the warehouse environment, leading to higher job satisfaction, lower error rates, and increased operational efficiency.
Continuous Improvement Strategies
Performance Monitoring
Performance monitoring involves the systematic measurement and evaluation of key performance indicators (KPIs) within the warehouse operations. By tracking metrics such as order processing times, inventory accuracy rates, and resource utilization, companies can identify areas for improvement, pinpoint operational inefficiencies, and implement targeted solutions to enhance overall performance. Regular performance monitoring enables warehouses to make data-driven decisions, adjust workflows proactively, and maintain peak efficiency levels in a dynamic operational environment.
Feedback Mechanisms
Implementing effective feedback mechanisms allows warehouses to gather insights from employees, customers, and stakeholders regarding the existing operational processes. By soliciting feedback on a regular basis, warehouses can identify pain points, discover opportunities for optimization, and address issues before they escalate. Additionally, involving employees in the feedback loop fosters a sense of ownership and accountability, encouraging continuous engagement and improvement. Feedback mechanisms serve as valuable tools for driving operational excellence, fostering a culture of innovation, and ensuring sustained efficiency within warehouse operations.
Ensuring Accuracy and Quality Control
In the realm of warehouse operations, Ensuring Accuracy and Quality Control stands as a paramount facet to guaranteeing the smooth and efficient functioning of the entire system. It is the meticulous attention to detail and strict adherence to quality standards that serve as the bedrock for operational excellence within a warehouse environment. The accuracy in inventory management, order processing, logistics, and shipping processes hinges on maintaining top-notch quality control measures. Without accurate and quality-controlled processes, warehouses run the risk of errors, delays, and customer dissatisfaction.
When delving into the essence of quality assurance checks, it becomes evident that these assessments are fundamental to intercepting any discrepancies or deviations from established standards. By conducting regular quality assurance checks throughout various stages of warehouse operations, businesses can proactively identify and rectify any potential issues before they escalate into more significant problems. Quality assurance checks encompass a range of evaluations, such as verifying inventory accuracy, inspecting the condition of stored goods, and assessing the precision of order processing procedures. These checks not only ensure compliance with set guidelines but also instill confidence in customers regarding the reliability and precision of the warehouse's operations.
Similarly, error detection and correction mechanisms play a pivotal role in fortifying the accuracy and efficiency of warehouse processes. In a dynamic warehouse setting where numerous variables come into play, errors are inevitable. However, what sets exemplary warehouses apart is their ability to swiftly detect errors and implement corrective measures seamlessly. Through the integration of advanced technological solutions like barcode scanning and RFID systems, warehouses can automate error detection, minimizing human errors and enhancing overall process accuracy. Additionally, establishing clear protocols for error correction and encouraging a culture of accountability among warehouse staff further contributes to maintaining high standards of quality control. The ability to promptly detect and rectify errors not only mitigates operational disruptions but also fosters a reputation for reliability and excellence in customer service.
Conclusion
In the labyrinthine realm of warehouse operations, the conclusion segment serves as the final cog in the intricate machinery of efficiency optimization. It encapsulates the culmination of strategies, analyses, and implementations highlighted throughout this enlightening discourse on optimizing warehouse task lists for improved operational efficacy. The significance of the conclusion cannot be overstated, as it synthesizes the core principles discussed, emphasizing the critical role of meticulous planning and strategic prioritization in achieving seamless warehouse workflows. This final section acts as a compass, guiding warehouse managers and personnel towards embracing progressive methodologies that foster productivity, accuracy, and continuous improvement.
Summary of Key Strategies
Embarking on a reflective odyssey through the galaxy of warehouse optimization strategies, we encounter a multitude of key strategies that serve as guiding stars in the vast expanse of efficient task management. These strategies, ranging from inventory management techniques to workflow streamlining processes, converge to form a cohesive roadmap towards operational excellence. Through meticulously crafted systems, such as ABC analysis and Just-in-Time inventory management, warehouses can harmonize their processes, minimize waste, and enhance productivity. The summary of key strategies illuminates the pivotal role of technology integration, employee empowerment, and quality assurance in establishing a robust foundation for optimized warehouse operations.
Future Outlook for Warehouse Task Optimization
As we gaze through the crystal ball of warehouse management, the future outlook for task optimization shines brightly with promise and innovation. Emerging trends in automation, data analytics, and artificial intelligence present boundless opportunities for revolutionizing warehouse operations towards unprecedented efficiencies. The advent of predictive analytics and machine learning algorithms is poised to redefine task prioritization, inventory forecasting, and logistics coordination. By embracing these technological marvels, warehouses can unlock new horizons of operational agility, cost-effectiveness, and customer satisfaction, propelling them into a dimension of unparalleled competitive advantage and sustainability.