Crafting an Efficient Factory Floor Plan for Maximum Productivity
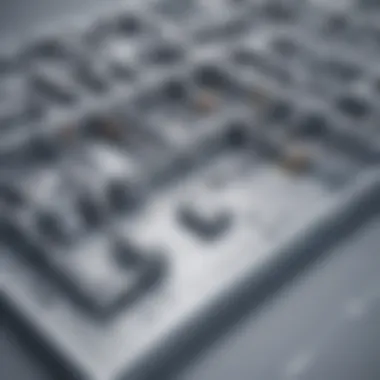
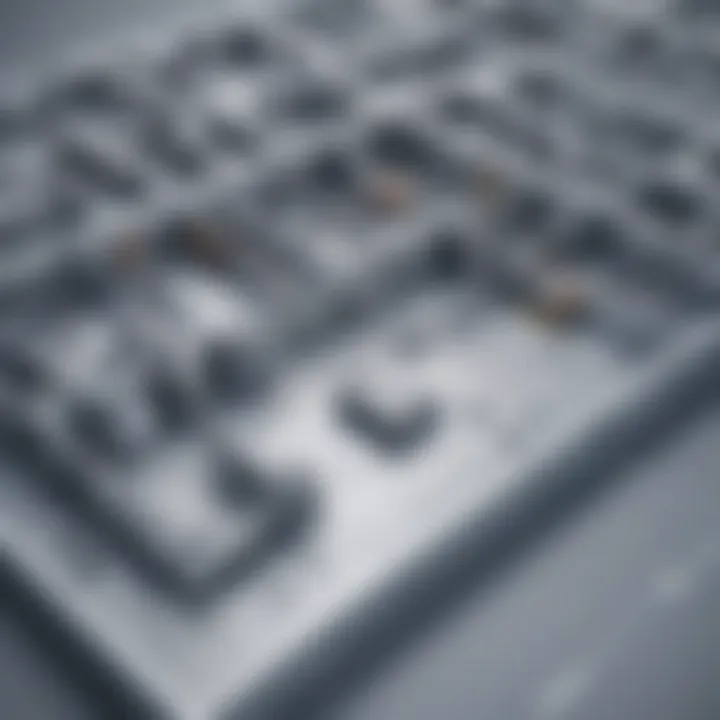
Overview of Factory Floor Plan Optimization
Understanding the significance of designing an efficient factory floor plan is crucial for enhancing productivity in manufacturing settings. As industrial processes evolve, the layout considerations and workflow optimizations play a pivotal role. Efficiently setting up a manufacturing facility demands a meticulous approach to ensure streamlined operations and increased output.
Fundamentals Explored
Key to optimizing a factory floor plan is grasping the fundamental principles and theories that underpin efficient manufacturing. Terminology such as spatial utilization, workflow mapping, and machinery placement are foundational for establishing an effective layout. By mastering these core concepts, one can lay a solid groundwork for maximizing productivity within a manufacturing environment.
Practical Applications and Illustrated Examples
Real-world case studies offer valuable insights into the practical applications of optimized factory floor plans. Examining successful implementations in various industries provides a tangible understanding of how theory translates into action. Hands-on projects, coupled with demonstrations of layout modifications enhancing workflow efficiency, allow for a tangible grasp of applying optimization techniques within manufacturing settings.
Advanced Concepts and Emerging Trends
Exploring cutting-edge developments in factory floor plan optimization unveils advanced techniques revolutionizing manufacturing processes. The integration of technology, such as AI-driven workflow analysis and IoT-enabled equipment coordination, showcases the future of efficient facility design. As innovations continue to reshape the industry, understanding these advanced concepts equips professionals with the foresight to leverage the latest trends for enhanced productivity.
Tips and Resources for Further Delving
For individuals keen on delving deeper into factory floor plan optimization, a myriad of resources exist to aid in continued learning. Recommended readings covering topics like lean manufacturing principles and Six Sigma methodologies provide in-depth knowledge for refining layout strategies. Additionally, access to software tools facilitating layout simulations and workflow visualization offers practical support for implementing optimization strategies.
Introduction
In the realm of industrial operations, designing a thoroughly optimized factory floor plan stands as a critical determinant of operational success. The essence of a well-crafted factory layout lies in its inherent ability to significantly impact the overall productivity, streamline operations, and ensure stringent safety and compliance standards. A meticulously planned floor layout not only enhances workflow efficiency but also plays a pivotal role in ensuring a seamless and productive manufacturing environment. In this comprehensive guide to optimizing factory floor plans for efficiency, we delve into the nitty-gritty details and key considerations essential for setting up a robust and functional manufacturing facility.
Understanding the Significance of a Well-Designed Factory Floor Plan
Impact on Productivity
Within the scope of factory operations, the impact of a meticulously designed floor plan on productivity cannot be overstated. A thoughtfully structured factory layout can tremendously boost productivity levels by reducing unnecessary movements, optimizing material flow, and enhancing overall operational efficiency. This strategic arrangement ensures that equipment, resources, and workstations are placed in a manner that minimizes downtime and maximizes output. By harmonizing the physical layout with operational requirements, productivity bottlenecks are effectively mitigated, leading to a more streamlined and efficient manufacturing process.
Efficiency Enhancements
Efficiency enhancements encompass a diverse array of strategies and optimizations implemented within the factory floor plan to drive productivity and performance. By incorporating lean manufacturing principles, implementing efficient workflow structures, and leveraging advanced technological solutions, an optimized floor plan can significantly enhance operational efficiency. These enhancements facilitate smoother production processes, reduce lead times, and ultimately contribute to a more agile and responsive manufacturing environment. Striving for efficiency improvements within the factory layout ensures that resources are utilized optimally, waste is minimized, and throughput is maximized.
Safety and Compliance
Safety and compliance considerations are paramount in the realm of factory operations. A well-designed floor plan prioritizes safety protocols, ensures ergonomic workstations, and adheres to regulatory standards to guarantee a secure and hazard-free working environment. By integrating safety measures seamlessly into the layout, potential risks are mitigated, accidents are prevented, and overall operational compliance is upheld. A factory floor plan that meticulously incorporates safety and compliance aspects not only safeguards the well-being of employees but also fosters a culture of operational excellence and responsibility.
Overview of the Factory Floor Planning Process
Initial Assessment
The initial assessment phase of factory floor planning plays a pivotal role in laying the foundation for an efficient and optimized layout. This evaluation involves analyzing existing floor configurations, identifying operational bottlenecks, and assessing resource utilization patterns. By conducting a comprehensive initial assessment, manufacturers can gain valuable insights into areas for improvement, strengths to leverage, and potential risks to mitigate. This phase sets the stage for informed decision-making and strategic planning, paving the way for a streamlined and effective factory floor design.
Space Utilization Analysis
Space utilization analysis is a critical component of factory floor planning, focusing on maximizing the efficiency of spatial resources within the manufacturing facility. This analysis entails optimizing layout configurations to ensure that available space is utilized judiciously, workflows are streamlined, and material flow is unhindered. By harnessing data-driven insights and spatial optimization techniques, manufacturers can enhance operational efficiency, minimize spatial inefficiencies, and create a dynamic and agile production environment. Space utilization analysis forms the backbone of a well-orchestrated factory floor plan, enabling manufacturers to make the most of their physical resources.
Workflow Mapping
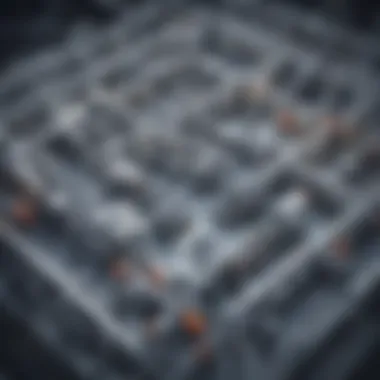
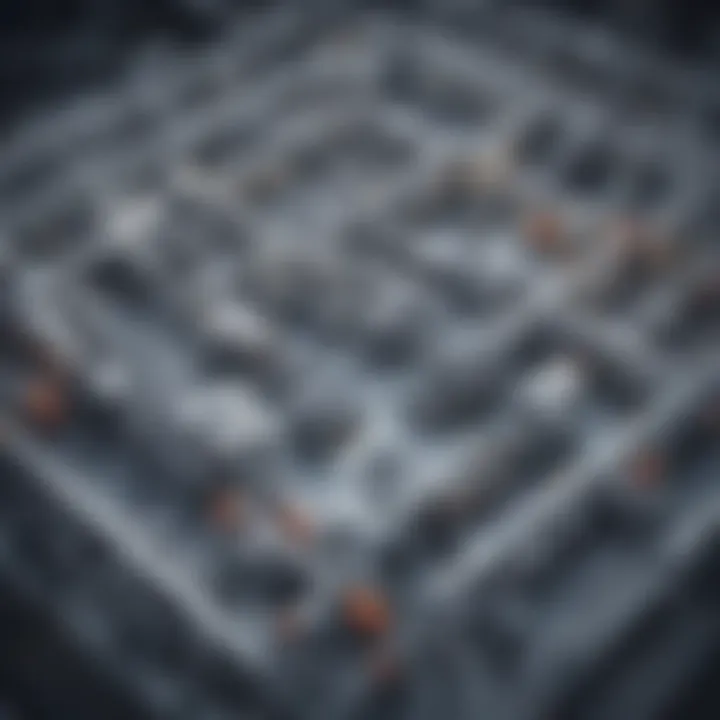
Workflow mapping delineates the intricate pathways of operational processes within the manufacturing setting, accentuating the interplay between tasks, resources, and personnel. By visually mapping out workflows and operational sequences, manufacturers can identify inefficiencies, streamline production processes, and optimize resource allocation. This meticulous planning process ensures that workflows are structured for maximum efficiency, bottlenecks are identified and resolved, and resource utilization is optimized. Workflow mapping serves as a roadmap for operational optimization, facilitating the creation of a fluid and responsive manufacturing environment.
Key Factors Influencing Floor Plan Design
Equipment Placement
Equipment placement stands as a fundamental factor influencing the design of a factory floor plan, dictating the spatial arrangement of machinery, tools, and resources. The strategic placement of equipment plays a crucial role in optimizing workflow efficiency, minimizing production downtime, and enhancing overall operational performance. By positioning equipment in a logical and ergonomic manner, manufacturers can streamline production processes, facilitate seamless material flow, and bolster productivity levels. Effective equipment placement is instrumental in creating a well-organized and efficient manufacturing setup, where operational tasks are executed seamlessly and resources are optimized for maximal output.
Material Flow
The management of material flow is a pivotal consideration in the design of a factory floor plan, encompassing the movement of raw materials, work-in-progress components, and finished products throughout the production process. By strategically orchestrating material flow pathways, manufacturers can minimize movement disruptions, reduce lead times, and enhance operational agility. Efficient material flow management ensures that resources are circulated optimally, production bottlenecks are alleviated, and operational throughput is optimized. By fine-tuning material flow dynamics within the factory layout, manufacturers can establish a synchronized and efficient production ecosystem that fosters productivity and performance.
Ergonomics
Ergonomics plays a crucial role in shaping a well-designed factory floor plan, focusing on optimizing workstations, equipment placement, and operational environments to enhance employee well-being and performance. By incorporating ergonomic principles into the layout design, manufacturers can create a safe, comfortable, and productive work environment that minimizes worker fatigue, prevents injuries, and boosts overall efficiency. Ergonomically designed workstations reduce strain on employees, enhance task visibility and accessibility, and promote a health-conscious workplace culture. Prioritizing ergonomics in floor plan design not only augments worker productivity and satisfaction but also underscores a commitment to employee welfare and operational excellence.
Layout Considerations
In the intricate realm of manufacturing efficiency, the significance of layout considerations cannot be overstated. A well-thought-out factory layout plays a pivotal role in ensuring smooth operations, optimized processes, and enhanced productivity. Whether it's about maximizing space utilization, streamlining workflows, or ensuring ergonomic design, every element of layout considerations contributes to the overall success of a manufacturing setup. By focusing on layout considerations, businesses can create an environment that fosters operational excellence and sustainable growth.
Types of Factory Layouts
Process Layout
Process layout, also known as functional layout, emphasizes grouping similar tasks together, promoting efficiency in operations. By organizing machinery, equipment, and resources based on the functions they perform, process layout minimizes movement, reduces downtime, and enhances productivity. While offering flexibility for diverse production requirements, process layout may require extensive space and increased handling time due to continuous product reorganization.
Product Layout
Product layout, or line layout, focuses on arranging workstations in a linear fashion to enable a continuous flow of products through the manufacturing process. This layout is well-suited for assembly line production, allowing for high volume output, minimal work-in-progress inventory, and efficient use of resources. However, product layout may lack flexibility for product variation and can lead to bottlenecks if not properly managed.
Fixed Position Layout
Fixed position layout is ideal for large or immovable projects where the product remains stationary, and work tasks are brought to it. Common in construction or shipbuilding industries, this layout minimizes product movement, optimizes resource utilization, and enhances on-site coordination. Despite its efficiency in certain contexts, fixed position layout may pose challenges in terms of space constraints and logistical coordination.
Combination Layout
Combination layout integrates aspects of both process and product layouts to leverage their respective advantages. By combining functional grouping with linear flow, businesses can achieve a balance between flexibility and efficiency. This layout offers the ability to cater to varying production needs, optimize resource allocation, and adapt to changing market demands. However, designing and managing a combination layout may require sophisticated planning and coordination to ensure seamless operations.
Determining Optimal Layout for Efficiency
Flow of Materials
Efficient material flow is a cornerstone of layout optimization, ensuring that raw materials, components, and finished products move seamlessly through the production facility. By minimizing transport distances, eliminating bottlenecks, and synchronizing material movement with production processes, businesses can enhance efficiency, reduce lead times, and mitigate waste. Implementing strategies such as Kanban systems and Just-in-Time inventory management can further streamline material flow and improve overall operational performance.
Equipment Accessibility
Ensuring easy access to machinery, tools, and workstations is essential for optimizing workflow efficiency. Well-planned equipment accessibility reduces waiting times, accelerates job completion, and minimizes disruptions in production. By strategically positioning equipment based on usage frequency and process dependencies, businesses can enhance operational agility, promote worker safety, and increase overall productivity. However, excessive proximity or inadequate spacing may lead to congestion, safety hazards, or efficiency bottlenecks within the manufacturing facility.
Workstation Design
The design of workstations plays a critical role in optimizing individual and collective task performance within a manufacturing environment. Ergonomically designed workstations enhance worker comfort, safety, and productivity by minimizing physical strain, fatigue, and error rates. Efficient workstation layout considers factors such as workflow sequence, tool accessibility, and operator convenience to create a productive work environment. By incorporating principles of human factors engineering and continuous improvement, businesses can achieve a balance between worker well-being and operational efficiency, ultimately driving sustainable growth and innovation.
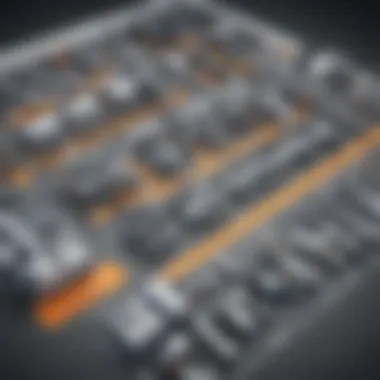
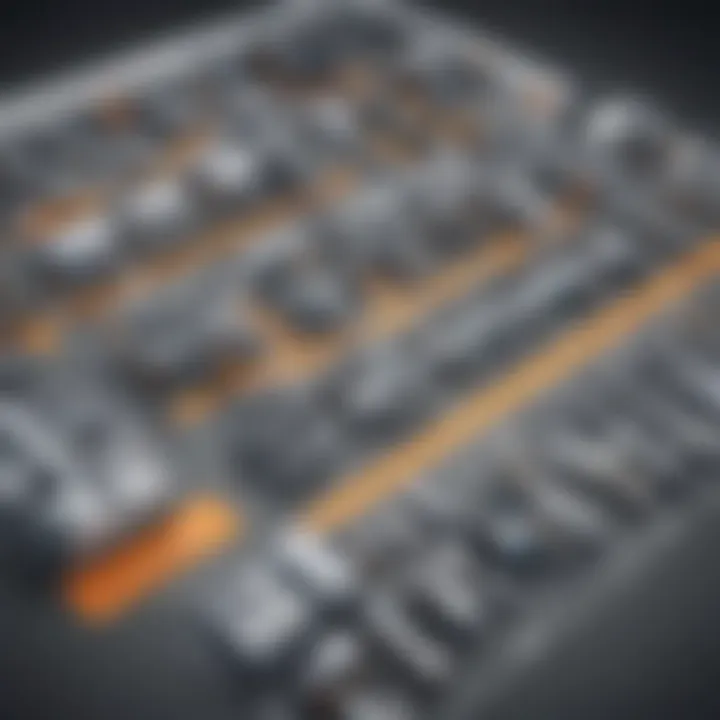
Workflow Optimization
Workflow optimization plays a critical role in enhancing the effectiveness of a factory floor plan. By streamlining production processes and minimizing inefficiencies, workflow optimization can significantly boost overall productivity. Effective workflow optimization involves carefully analyzing and restructuring the sequence of tasks and operations within the manufacturing facility. This process aims to eliminate bottlenecks, reduce idle time, and enhance the overall flow of operations. By implementing efficient workflow optimization strategies, manufacturers can achieve greater output with optimal resource utilization.
Streamlining Production Processes
Lean Manufacturing Principles
Lean manufacturing principles focus on maximizing value and minimizing waste in production processes. By emphasizing continuous improvement and eliminating non-value-added activities, lean manufacturing aims to enhance efficiency and quality. The key characteristic of lean manufacturing is its emphasis on waste reduction, whether it be in the form of overproduction, excess inventory, or defects. This approach is popular due to its ability to streamline operations, improve lead times, and boost overall competitiveness. While lean manufacturing requires a shift in mindset and organizational culture, its benefits in terms of efficiency and cost reduction make it a compelling choice for optimizing factory floor plans.
Kanban Systems
Kanban systems are visual management tools that help control the flow of materials and tasks in production. By using signals such as cards or bins to indicate when and what to produce, Kanban systems facilitate a pull-based production method. The key characteristic of Kanban systems is their ability to optimize inventory levels, minimize waste, and enhance responsiveness to demand fluctuations. This approach is beneficial as it enables just-in-time production, reduces overproduction, and improves resource allocation. However, implementing Kanban systems effectively requires proper training and alignment across all departments to ensure seamless integration into the workflow.
Batch Production Strategies
Batch production strategies involve producing goods in specific quantities or batches to optimize production efficiency. By grouping similar tasks together and minimizing setup times between batches, manufacturers can reduce idle time and enhance productivity. The key characteristic of batch production is its ability to balance efficiency with flexibility, allowing for cost-effective production of varied products. This approach is advantageous as it can increase throughput, reduce lead times, and improve resource utilization. However, batch production strategies may require more extensive planning and coordination to ensure smooth transitions between batches and avoid unnecessary delays.
Implementing Just-in-Time Practices
Inventory Management
Inventory management is a crucial aspect of just-in-time practices, focusing on maintaining optimal inventory levels to support continuous production. By carefully monitoring inventory turnover rates, minimizing excess stock, and utilizing inventory control systems, manufacturers can prevent stockouts and reduce holding costs. The key characteristic of inventory management is its role in synchronizing supply with demand, allowing for efficient production planning and reduced waste. This practice is beneficial as it enhances agility, improves cash flow, and minimizes inventory obsolescence. However, effective inventory management requires accurate forecasting, real-time tracking systems, and close collaboration with suppliers to ensure timely replenishment.
Reducing Lead Times
Reducing lead times involves minimizing the duration between order placement and product delivery, enhancing customer satisfaction and operational efficiency. By optimizing production processes, reducing setup times, and improving workflow coordination, manufacturers can shorten lead times and increase responsiveness. The key characteristic of reducing lead times is its impact on overall operational efficiency and competitiveness. This strategy is beneficial as it allows for faster order fulfillment, reduced inventory holding costs, and improved agility in responding to market demands. However, reducing lead times may require investment in automation, workflow redesign, and quality enhancement initiatives to achieve sustainable improvements.
Minimizing Waste
Minimizing waste is a fundamental principle of lean manufacturing, focusing on identifying and eliminating non-value-added activities in production. By implementing practices such as 5S organization, standardized work procedures, and mistake-proofing techniques, manufacturers can reduce waste and enhance operational efficiency. The key characteristic of minimizing waste is its emphasis on continuous improvement and employee involvement in waste reduction initiatives. This approach is beneficial as it leads to cost savings, quality improvements, and a more sustainable manufacturing operation. However, minimizing waste requires a cultural shift, effective training programs, and regular performance monitoring to ensure long-term success.
Technology Integration
In the domain of factory floor plan optimization, Technology Integration plays a pivotal role. By seamlessly incorporating technological advancements into the layout design and operational processes, manufacturing facilities can significantly enhance their efficiency and productivity. The integration of technology enables real-time monitoring, automation of tasks, and data-driven decision-making, leading to streamlined production processes and improved resource utilization. It revolutionizes traditional manufacturing practices, paving the way for smart factories that are agile, adaptive, and efficient. With the continuous advancements in technology, embracing these innovations has become imperative for staying competitive in today's rapidly evolving industrial landscape.
Role of Automation in Floor Plan Optimization
Automation, particularly Robotics and Cobots, has emerged as a game-changer in floor plan optimization. Robotics and Cobots are key components of automated manufacturing systems, offering versatility, precision, and efficiency in executing various tasks on the factory floor. Robots are adept at handling repetitive, labor-intensive operations with consistent accuracy, thereby reducing the risk of errors and enhancing production output. Cobots, on the other hand, are collaborative robots designed to work alongside human operators, augmenting productivity while ensuring safety in shared workspaces. Their flexibility and ease of reprogramming make them invaluable assets for optimizing floor plans and achieving operational excellence.
Robotics and Cobots
The integration of Robotics and Cobots brings forth numerous advantages. Their ability to operate 247 without fatigue ensures continuous and uninterrupted production cycles. The precision and speed at which these machines perform tasks lead to enhanced efficiency and output quality. Moreover, their compact design enables seamless integration into existing factory layouts, optimizing space utilization and workflow management. While Robotics and Cobots offer substantial benefits, including improved operational efficiency, reduced production time, and increased safety for workers, challenges such as high initial costs and the need for specialized training may pose constraints that require careful consideration.
IoT Applications
IoT Applications facilitate the connectivity of devices and equipment on the factory floor, enabling real-time data exchange and analysis. By harnessing IoT technologies, manufacturers can monitor operations remotely, predict maintenance requirements, and optimize resource allocation. The key characteristic of IoT Applications lies in their ability to create a network of interconnected devices, sensors, and systems, providing valuable insights for enhancing productivity and decision-making. This seamless integration of data systems fosters improved communication, collaboration, and operational efficiency, driving continuous improvements in floor plan optimization.
Data Analytics for Process Improvement
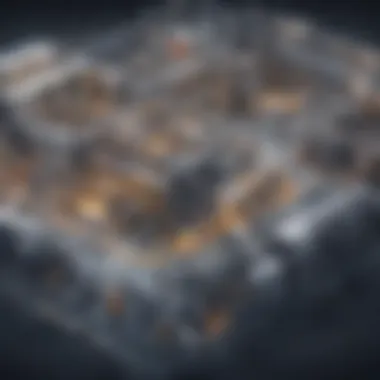
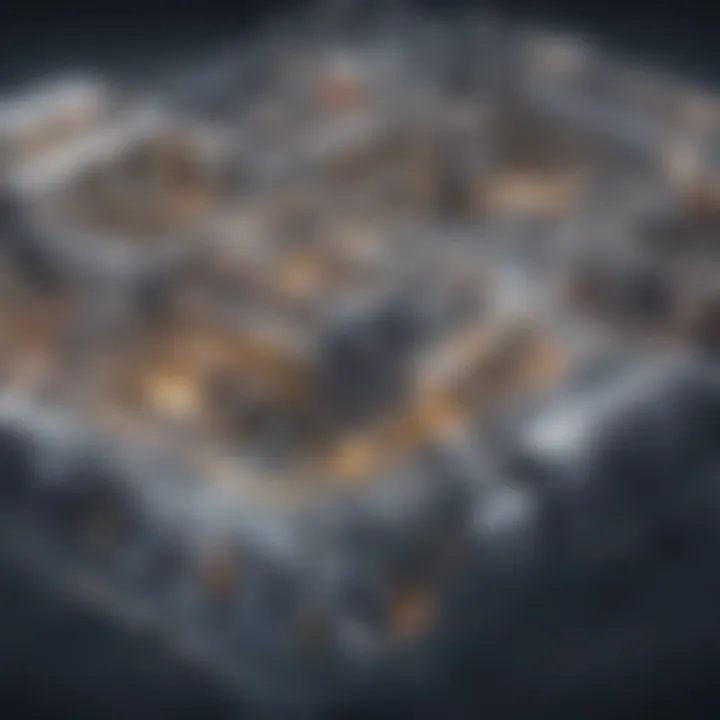
Data Analytics has redefined how manufacturers analyze and optimize their production processes. By leveraging data-driven insights, companies can identify bottlenecks, predict trends, and enhance operational performance. The key characteristic of Data Analytics lies in its capability to process and interpret vast amounts of data swiftly, enabling informed decision-making and proactive troubleshooting. The utilization of Data Analytics empowers organizations to implement targeted strategies for process improvement, resource optimization, and quality enhancement, driving overall operational excellence and competitive edge.
Utilizing CAD Software for Designing
CAD Software serves as a cornerstone in designing factory floor plans with precision and efficiency. Through CAD tools, manufacturers can create detailed layout designs, visualize spatial arrangements, and simulate operational workflows. The adoption of CAD Software streamlines the design process, reducing manual errors and enhancing collaboration among cross-functional teams. This digital tool empowers designers and engineers to iteratively refine and optimize floor plans, considering factors such as equipment placement, material flow, and ergonomics, to achieve a well-coordinated and functional factory layout.
Digital Twin Simulation
Digital Twin Simulation revolutionizes the design and development of factory floor plans by creating virtual replicas of physical assets and processes. By mirroring the operational environment in a digital space, manufacturers can conduct virtual testing, optimize layouts, and anticipate potential challenges before implementation. The key characteristic of Digital Twin Simulation is its ability to provide a digital representation of the factory floor in real-time, enabling stakeholders to visualize and analyze different scenarios for efficiency and scalability. This technology equips manufacturers with valuable insights to make informed decisions, adapt to changing dynamics, and drive continuous improvement in factory floor planning.
Virtual Reality Prototyping
Virtual Reality Prototyping offers a dynamic approach to visualize and evaluate factory floor designs in an immersive virtual environment. Through Virtual Reality (VR) simulations, stakeholders can interact with the proposed layout, assess spatial dimensions, and identify optimization opportunities. The key characteristic of Virtual Reality Prototyping is its capacity to provide a realistic and interactive experience of the factory floor, fostering better design decision-making and operational planning. This advanced tool enables stakeholders to identify potential design flaws, improve workflow efficiencies, and enhance safety measures before physical implementation, ensuring a cost-effective and optimized factory floor plan.
The integration of CAD Software with Digital Twin Simulation and Virtual Reality Prototyping empowers manufacturers to design, analyze, and refine factory floor plans with precision and foresight, leading to optimized layouts, streamlined workflows, and enhanced operational efficiencies.
Maintenance and Adaptability
In the realm of factory floor efficiency, the section focusing on maintenance and adaptability holds immense significance. Ensuring that the floor plan is not only optimized for current operations but also adaptable for future needs is vital for long-term success. Maintenance aspects cover the upkeep of equipment, ensuring that machinery functions at peak performance levels. Regular maintenance protocols also aid in preventing breakdowns and costly downtimes, contributing to uninterrupted production flow.
Ensuring Scalability in Floor Plan
Flexible Layout Designs
Embracing flexible layout designs within a factory floor plan is quintessential for accommodating evolving production requirements. The flexibility allows for swift modifications in response to changing demands or technological advancements. An imperative characteristic of flexible layouts is the modular construction, enabling easy reconfiguration of workstations and machinery placements as needed. This adaptability ensures that the factory floor remains efficient and versatile, ready to meet the dynamic needs of the industry.
Future Expansion Considerations
Deliberating on potential future expansions during the initial floor planning stages is crucial. Considering future expansion allows for seamless scalability without major disruptions to ongoing operations. Anticipating growth and incorporating expansion strategies within the layout design ensures that the factory can easily accommodate increased production capacity or new technologies. The foresight in future expansion considerations establishes a strategic foundation for sustained development.
Scheduled Maintenance Protocols
Maintaining scheduled maintenance protocols is indispensable for the operational integrity of a manufacturing facility. Employing meticulous equipment upkeep practices guarantees machinery longevity and optimal performance. Regular inspections play a pivotal role in identifying potential issues or wear-and-tear, preemptively addressing maintenance needs before they escalate. This proactive approach to equipment maintenance mitigates risks of unforeseen breakdowns, fortifying the reliability and efficiency of the factory floor.
Equipment Upkeep
Prioritizing equipment upkeep involves adhering to a structured maintenance schedule. By ensuring timely servicing, cleaning, and calibration of machinery, the efficiency and lifespan of equipment are maximized. Consistent equipment upkeep minimizes the likelihood of unexpected failures, promoting uninterrupted production processes. The proactive nature of equipment upkeep fosters a proactive maintenance culture within the manufacturing environment.
Regular Inspections
Regular inspections serve as a preventative measure against potential operational disruptions. Conducting routine inspections allows for the early detection of anomalies, wear, or deterioration in equipment. The meticulous review of machinery operations and components ensures that any issues are swiftly addressed, averting unplanned downtime. Implementing regular inspections as part of the maintenance protocols cultivates a culture of continuous improvement and operational excellence within the factory setting.
Conclusion
Key Takeaways for Optimal Factory Floor Design
Continuous Improvement Mindset
Embracing a continuous improvement mindset is imperative for fostering a culture of innovation and growth within manufacturing facilities. This approach emphasizes the importance of constantly evolving processes, implementing best practices, and seeking ways to enhance operational efficiencies over time. The key characteristic of a continuous improvement mindset lies in its proactive nature, constantly seeking ways to optimize workflows, minimize waste, and enhance productivity. By instilling a culture of continuous improvement, companies can stay ahead of the competition, adapt to changing market demands, and drive sustainable growth in the long term. Despite requiring a commitment to change and ongoing refinement, the benefits of a continuous improvement mindset in optimizing factory floor plans include increased operational efficiency, reduced costs, and improved product quality, making it a crucial strategy for achieving long-term success within the manufacturing landscape.
Adaptability to Market Dynamics
The ability to adapt to evolving market dynamics is essential for maintaining relevance and competitive advantage in the manufacturing sector. By remaining agile and responsive to market trends, companies can quickly adjust production strategies, modify product offerings, and realign operational processes to meet shifting consumer demands. The key characteristic of adaptability to market dynamics lies in its capacity to anticipate changes, pivot rapidly, and capitalize on emerging opportunities. While presenting challenges in terms of forecasting and resource allocation, the advantages of adapting to market dynamics within factory floor planning include improved customer satisfaction, increased market share, and enhanced brand reputation. By prioritizing flexibility and responsiveness, organizations can navigate complex market landscapes, seize competitive advantages, and drive sustained growth despite external uncertainties.
Investment in Employee Training
Investing in employee training is a strategic decision that yields significant benefits in optimizing factory floor design and performance. By providing employees with specialized skills, advanced technical knowledge, and opportunities for professional development, companies can enhance workforce capabilities, improve operational efficiencies, and drive innovation within the manufacturing environment. The key characteristic of investment in employee training lies in its emphasis on building a skilled and motivated workforce, capable of adapting to new technologies, embracing best practices, and contributing to organizational success. While requiring initial resource allocation and planning, the unique feature of employee training programs lies in their capacity to foster employee engagement, reduce turnover rates, and elevate overall production standards. By prioritizing continuous learning and skill development, organizations can equip their teams with the tools and knowledge needed to excel in a competitive manufacturing landscape, reinforcing the foundation for long-term success and sustainability.
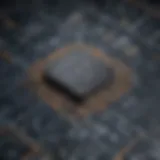
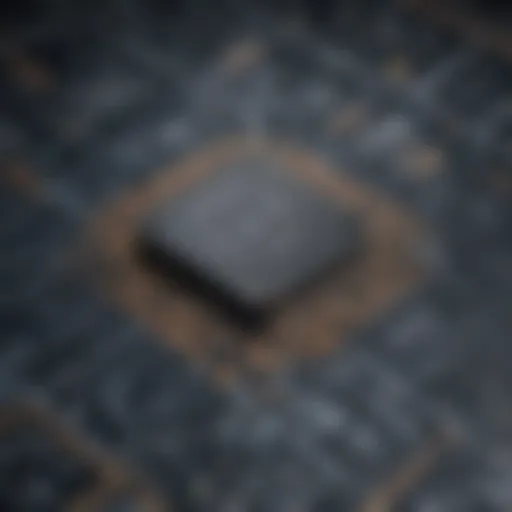