Unveiling the Diverse World of AC Motors: A Comprehensive Exploration
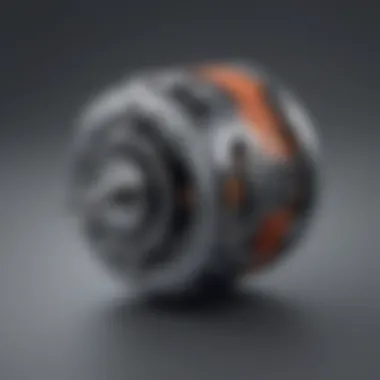
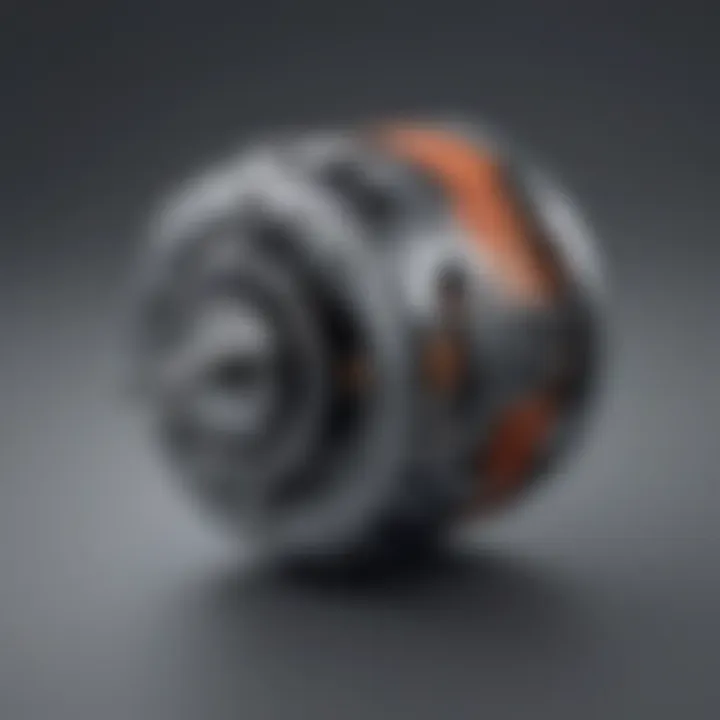
Overview of Topic
In this section, we will embark on a thorough exploration of the diverse types of AC motors. Our journey will unveil the intricate workings, applications, and advantages of these motor systems, shedding light on their critical role in various industries. Delving into the realm of induction motors to synchronous motors, we aim to provide a comprehensive understanding of the technology driving AC motor systems. By dissecting core concepts and practical applications, readers can expect to enrich their knowledge and grasp the fundamental essence of these integral components within the technological landscape.
Fundamentals Explained
The fundamentals of AC motors lay the groundwork for comprehension and in-depth analysis. From delving into the core principles and theories that underpin the functionality of these motors to unraveling key terminologies and definitions essential for grasping their intricate mechanisms, this section aims to equip readers with a solid foundational knowledge base. By breaking down basic concepts and elucidating critical aspects, individuals taking their first steps into the realm of AC motors will find themselves navigating a well-illuminated path of understanding.
Practical Applications and Examples
Real-world case studies and applications serve as guiding beacons in understanding the practical implementation of AC motors. By exploring diverse demonstrations and hands-on projects, readers can witness firsthand the seamless integration of these motors into various industries. With the inclusion of code snippets and implementation guidelines, individuals seeking to apply their theoretical knowledge in practical settings will find ample support and guidance in this section.
Advanced Topics and Latest Trends
Unlocking the realm of advanced topics and cutting-edge developments, this section elevates the discourse around AC motors. From exploring avant-garde techniques and methodologies shaping the future landscape of these motors to delving into emerging trends and future prospects, readers will find themselves at the frontier of innovation. By peering into the horizon of possibilities, this section aims to stimulate curiosity and anticipation for what lies ahead in the evolution of AC motor technologies.
Tips and Resources for Further Learning
For individuals seeking to deepen their understanding and expand their knowledge horizons, this section offers a curated selection of recommended books, courses, and online resources. By providing access to tools and software relevant to practical usage, readers can further enhance their learning journey and stay abreast of the latest developments in AC motor technology.
Introduction to AC Motors
In this insightful exploration of AC motors, we delve deep into the fundamental concepts that drive these electrical devices. Understanding AC motors is pivotal in comprehending the intricate systems that power various industrial applications. With a focus on efficiency, reliability, and versatility, delving into the realm of AC motors provides a solid foundation for grasping the technological advancements in modern machinery.
Understanding AC Motors
Basic Principles of AC Motors
The basic principles of AC motors revolve around the interaction between magnetic fields and electrical currents, resulting in rotational motion. This core principle enables the conversion of electrical energy into mechanical energy efficiently, making AC motors a popular choice across industries. The key characteristic of AC motors lies in their ability to operate on alternating current, offering a seamless energy conversion process essential for a wide range of applications. The unique feature of AC motors is their adaptability to varying operational speeds, providing flexibility in meeting diverse industrial requirements. While AC motors excel in converting electrical energy into motion, they may have limitations in high precision applications due to inherent factors like torque ripple.
Impact of Alternating Current on Motor Operation
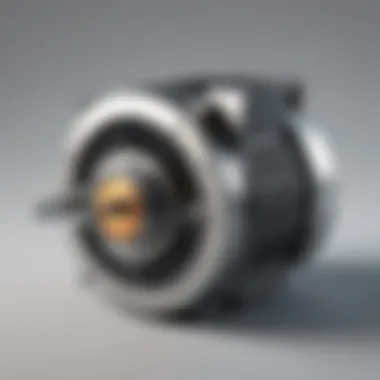
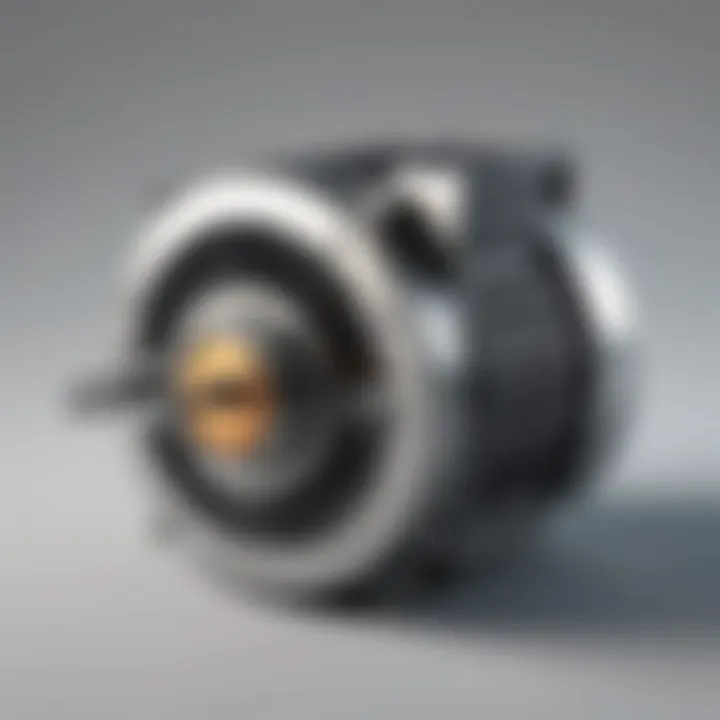
The impact of alternating current on motor operation is profound, as AC power facilitates the seamless functioning of motors across different loads and operational conditions. The key characteristic of alternating current lies in its ability to change direction cyclically, essential for sustaining continuous motion in AC motors. This feature makes AC motors ideal for applications requiring sustained rotation, such as industrial pumps and conveyor systems. The unique value of alternating current in motor operation is its energy efficiency, wherein AC motors can achieve optimal performance levels while minimizing power losses. However, the reliance on alternating current also poses challenges in terms of motor control precision, especially in scenarios demanding high accuracy and speed regulation.
Types of AC Motors
AC motors are a crucial component in various industrial and commercial applications, playing a vital role in powering machinery and processes. Understanding the different types of AC motors is essential for optimizing performance and efficiency. In this article, we will explore the characteristics, benefits, and considerations associated with induction motors, synchronous motors, brushless AC motors, servo motors, variable frequency drives (VFDs), and dual-voltage motors. Each type offers unique features and applications that cater to specific industry needs.
Induction Motors
Single-phase Induction Motors
Single-phase induction motors are widely used in applications where three-phase power is not available. Their simplicity in design and cost-effectiveness make them a popular choice for small-scale operations. Although less efficient than three-phase motors, single-phase induction motors are suitable for appliances like fans, pumps, and household equipment due to their easy installation and maintenance.
Three-phase Induction Motors
Three-phase induction motors are the workhorses of industrial settings, providing robust performance and reliability. Their ability to generate high starting torque and operate seamlessly in demanding conditions makes them ideal for heavy-duty applications such as conveyor belts, compressors, and industrial machinery. Despite their higher initial cost, three-phase induction motors deliver superior efficiency and longevity compared to single-phase counterparts.
Working Mechanism and Applications
The fundamental working principle of induction motors involves the interaction between the rotating magnetic field and rotor currents, inducing rotation. Applications spanning from manufacturing processes to conveyors and pumps demonstrate the versatility and adaptability of induction motors across various industries. However, factors such as starting current requirements and speed control limitations should be considered when deploying induction motors in specific setups.
Synchronous Motors
Differences from Induction Motors
Synchronous motors operate at a fixed speed synchronized with the supply frequency, in contrast to induction motors that run at slightly lower speeds. This synchronous operation eliminates slip, allowing precise speed control and accurate positioning in applications requiring constant speed output. Integrating synchronous motors can enhance system efficiency and performance by minimizing energy losses associated with slip.
Uses in Synchronous Applications
Synchronous motors find applications in synchronous clocks, precision instruments, and systems requiring constant speed operation. Their synchronous speed capability and inherent stability make them suitable for industries such as healthcare, telecommunications, and robotics, where timing accuracy is critical. Incorporating synchronous motors ensures reliable performance and synchronized operation in specialized equipment.
Advantages and Disadvantages
The advantages of synchronous motors lie in their efficiency, power factor correction, and synchronous speed control. Despite their advantages, synchronous motors may pose challenges in starting methods, cost considerations, and maintenance complexity compared to induction motors. Understanding the trade-offs between synchronous and induction motors is essential in selecting the most suitable option for specific application requirements.
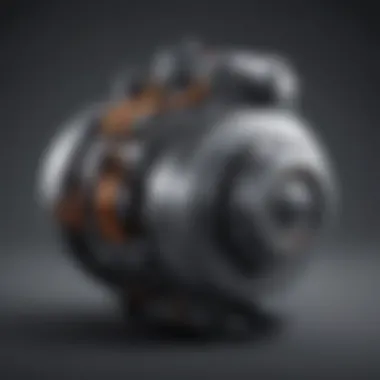
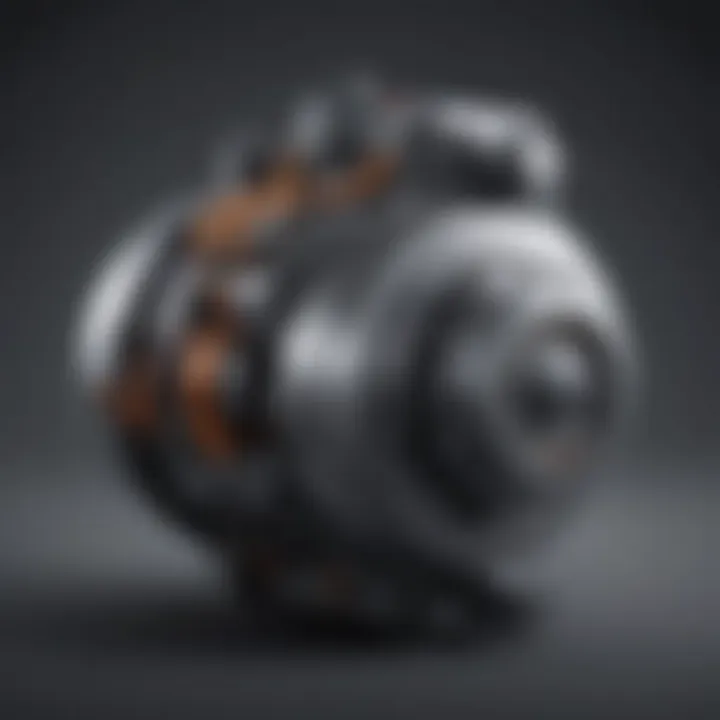
Brushless AC Motors
Design and Operation
Brushless AC motors eliminate the need for brushes, enhancing reliability and reducing maintenance requirements. The synchronous operation of brushless motors with electronic commutation ensures precise control and torque output. Their compact design and reduced electromagnetic interference make them ideal for applications demanding high efficiency and smooth operation.
Efficiency and Maintenance Benefits
The brushless design minimizes wear and tear, resulting in extended operational lifespan and reduced downtime for maintenance. The efficiency gains from brushless AC motors improve overall system performance and energy efficiency, making them a preferred choice in environments where reliability is paramount. Maintenance benefits include fewer moving parts, lower noise emissions, and enhanced durability in challenging operating conditions.
Applications in Various Industries
Brushless AC motors find applications in sectors such as automotive, aerospace, and renewable energy, where precise control and high performance are vital. The versatility of brushless motors enables their integration in electric vehicles, HVAC systems, and industrial automation, catering to diverse industry demands. Leveraging the advanced features of brushless AC motors can result in improved system efficiency and productivity across different sectors.
Servo Motors
Precise Control Capabilities
Servo motors offer unparalleled precision in velocity and position control, making them essential in automation and robotics. The closed-loop feedback mechanism ensures accurate movement and real-time adjustments, enhancing productivity and quality in manufacturing processes. The high-resolution encoders and responsive control systems of servo motors enable intricate operations requiring tight tolerances and rapid responses.
Integration with Automation Systems
Servo motors seamlessly integrate with automation systems through dedicated controllers and communication protocols. The synergy between servo motors and automation software enables synchronized motion control and programming flexibility, optimizing operational efficiency and throughput. The adaptability of servo motors to varying load conditions and motion profiles makes them suitable for dynamic applications in industrial automation and robotics.
Industrial and Robotics Applications
Servo motors drive advancements in robotics, CNC machines, and packaging equipment, offering dynamic performance and precision. Their ability to operate in high-speed, high-accuracy applications enhances productivity and quality in complex manufacturing environments. Employing servo motors in industrial and robotics applications elevates system performance, enabling agile motion control and precise task execution for diverse operational needs.
Variable Frequency Drives (VFDs)
Role in Controlling AC Motor Speed
VFDs play a pivotal role in regulating motor speed by adjusting the frequency and voltage of the supplied power. This dynamic control mechanism enables gradual acceleration and deceleration of motors, optimizing energy efficiency and reducing mechanical stress. Implementing VFDs in AC motor systems enhances operational flexibility and allows for customized speed profiles based on specific application requirements.
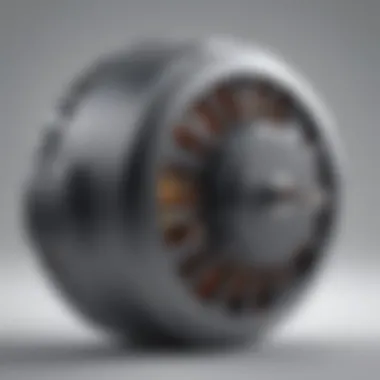
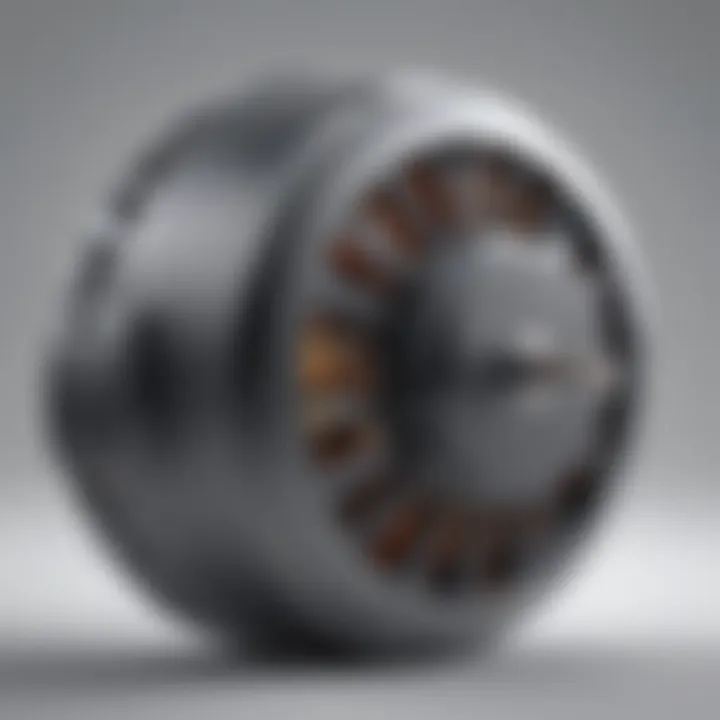
Efficiency Improvements
The use of VFDs results in significant energy savings by matching motor speed to the load requirements, reducing energy consumption during partial load conditions. These efficiency gains contribute to a greener operational footprint and cost savings in energy-intensive applications. Promoting the adoption of VFDs in industrial and commercial sectors can lead to substantial improvements in energy management and operational sustainability.
Industrial and Commercial Applications
VFDs find widespread applications in HVAC systems, water treatment plants, and material handling equipment, where variable speed control is essential. The adaptability of VFDs to diverse motor types and load variations enhances system efficiency and performance across industries. Incorporating VFDs into motor control strategies enables precise speed adjustments, fault detection capabilities, and operational fine-tuning for optimized productivity and energy conservation.
Dual-Voltage Motors
Operation on Different Voltage Levels
Dual-voltage motors offer operational flexibility by supporting multiple voltage configurations, accommodating varying power supply specifications. The capability to switch between voltage levels enables seamless integration into different electrical networks without requiring additional transformers or converters. Businesses with fluctuating voltage requirements can benefit from the versatility of dual-voltage motors in ensuring consistent motor performance and reliability.
Flexibility in Applications
The dual-voltage feature allows for versatile deployment in diverse applications, ranging from industrial machinery to commercial appliances. The dual-voltage capability enhances operational adaptability, streamlining motor integration in facilities with diverse voltage standards and grid conditions.
Considerations for Installation and Setup
When installing dual-voltage motors, factors such as proper wiring configuration, voltage selection, and safety precautions need to be meticulously managed. These considerations ensure optimal motor performance, prevent voltage-related malfunctions, and promote safe operation in varied electrical environments. Incorporating dual-voltage motors necessitates adherence to installation best practices and electrical codes to align with standard safety and operational guidelines.
Application Areas of AC Motors
In this comprehensive guide to exploring the diverse types of AC motors, understanding the application areas is crucial. The industrial sector heavily relies on AC motors for various operations, making it a ubiquitous technology in manufacturing environments. These motors play a vital role in powering manufacturing processes, conveyor systems, and pumps, and compressors. Their importance lies in their efficiency, reliability, and adaptability to different industrial tasks. AC motors form the backbone of these application areas, ensuring smooth operations and enhanced productivity.
Industrial Sector
Manufacturing processes
When delving into the realm of manufacturing processes, the role of AC motors is indispensable. These motors drive machinery essential for production lines, from assembly to packaging. Their key characteristic lies in providing consistent power output, ensuring uninterrupted workflow. The reliability and scalability of AC motors make them a popular choice in manufacturing industries. The unique feature of AC motors in manufacturing processes is their ability to adjust speed and torque according to specific production requirements. This flexibility enhances efficiency and precision, contributing to optimized manufacturing operations.
Conveyor systems
Conveyor systems rely on AC motors to propel, control, and automate the movement of materials along the production line. The key characteristic of AC motors in conveyor systems is their ability to maintain consistent speed and torque, essential for seamless material handling. Their reliability and durability make them a preferred choice, ensuring continuous operation without frequent breakdowns. One unique feature of AC motors in conveyor systems is their energy-saving capabilities, reducing operational costs while maintaining high performance. These motors offer advantages such as precise speed control and minimal maintenance requirements, making them an efficient and cost-effective solution for material transportation.
Pumps and compressors
In the domain of pumps and compressors, AC motors serve as the driving force behind fluid circulation and compression processes. Their key characteristic lies in providing the necessary power to maintain optimal pump and compressor performance. The reliability and robustness of AC motors make them an ideal choice for such critical applications, ensuring consistent operation under varying load conditions. A unique feature of AC motors in pumps and compressors is their ability to adapt to changing operational demands, adjusting speed and output to meet specific requirements. This flexibility enhances system efficiency and overall productivity, highlighting the significance of AC motors in powering essential equipment for fluid management and compression in industrial settings.