Unveiling the Intricacies of Material Requirements Planning: A Comprehensive Exploration
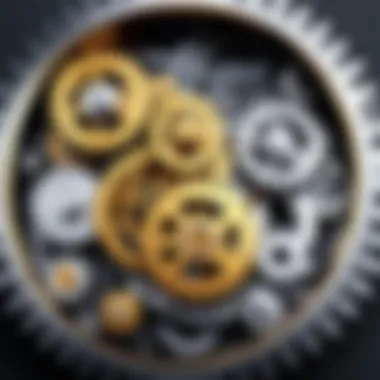
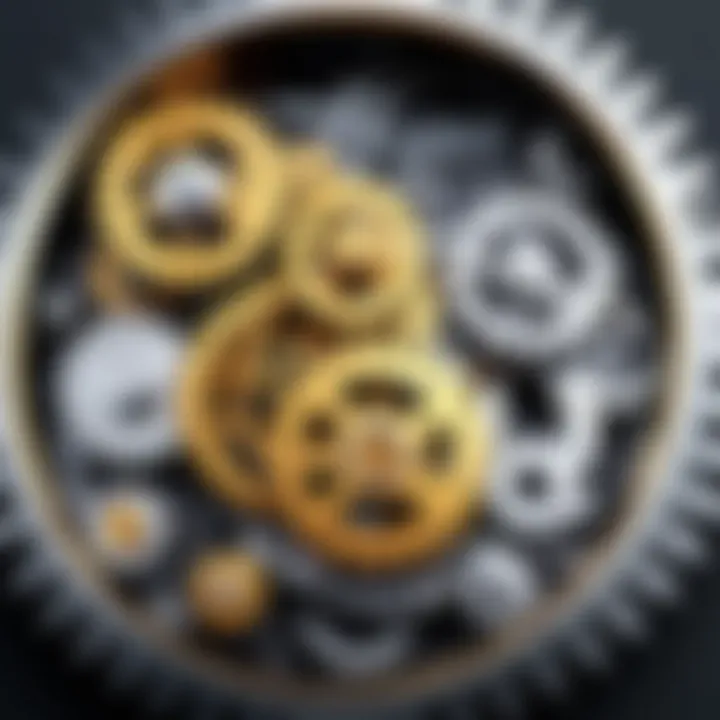
Overview of Topic
Material Requirements Planning (MRP) stands at the forefront of supply chain management and manufacturing processes, playing a pivotal role in ensuring operational efficiency and optimizing resource utilization. Delving into the realm of MRP unveils a complex yet essential system that orchestrates the seamless flow of materials within production facilities and distribution channels. Understanding MRP in its entirety is paramount for businesses aiming to streamline their operations and enhance productivity.
Fundamentals Explained
At its core, Material Requirements Planning operates on the foundational principles of demand forecasting, inventory management, and production scheduling. By analyzing demand patterns and aligning them with inventory levels, MRP facilitates the timely procurement and allocation of materials to meet production requirements. Key terminologies integral to MRP include Bill of Materials (BOM), Master Production Schedule (MPS), and Inventory Status Record (ISR), each playing a distinct role in the synchronized functioning of the system.
Practical Applications and Examples
Real-world applications of MRP span across various industries, showcasing its efficacy in optimizing inventory levels, minimizing stockouts, and improving production lead times. Case studies exemplifying successful MRP implementations reveal significant cost savings, enhanced production agility, and heightened customer satisfaction. Hands-on projects demonstrating the implementation of MRP software solutions provide practitioners with a practical understanding of the system's functionalities and benefits.
Advanced Topics and Latest Trends
The evolution of Material Requirements Planning has led to the emergence of advanced methodologies such as Manufacturing Resource Planning (MRP II) and Enterprise Resource Planning (ERP), expanding its scope beyond traditional manufacturing environments. Latest trends in MRP focus on incorporating artificial intelligence for demand forecasting, leveraging real-time data analytics for precision inventory management, and integrating cloud-based solutions for enhanced scalability. Future prospects for MRP include predictive analytics, IoT integration, and blockchain technology for secure supply chain transactions.
Tips and Resources for Further Learning
Individuals seeking in-depth knowledge on Material Requirements Planning can explore a plethora of resources ranging from academic textbooks to online courses and specialized software tools. Recommended readings include 'Introduction to Materials Management' by Tony Arnold and 'Modern Production/Operations Management' by Elwood S. Buffa, offering comprehensive insights into MRP fundamentals and applications. Online platforms like Coursera and Udemy feature courses on supply chain management and enterprise resource planning, providing hands-on experience with MRP systems. For practical usage, software solutions like SAP ERP, Oracle NetSuite, and Microsoft Dynamics offer robust MRP modules tailored to diverse business requirements.
Preface to Material Requirements Planning
Material Requirements Planning (MRP) holds a pivotal role in the realm of supply chain management and manufacturing. Within the context of this comprehensive guide, the significance of MRP transcends mere logistic operations; it serves as the linchpin for streamlining production processes and inventory management. Understanding the intricacies of MRP is paramount for businesses aiming to achieve operational efficiency and cost-effectiveness. By delving into the essence of MRP, readers will navigate through a labyrinth of concepts to grasp its profound impact on business sustainability and growth.
Definition of MRP
Understanding the Basics of MRP
Unraveling the core principles underlying MRP unveils a systematic approach to material planning and procurement. The essence of comprehending the basics of MRP lies in its ability to forecast and quantify production requirements with precision. This meticulous process empowers businesses to align their resources optimally, fostering a proactive production environment. The distinctive feature of understanding the basics of MRP rests in its capacity to enhance operational agility and responsiveness to market dynamics. However, the potential disadvantage of overreliance on MRP lies in its susceptibility to inaccuracies stemming from unforeseen variables.
Evolution of MRP Systems
The evolution of MRP systems signifies a transition towards sophisticated technological solutions for modern supply chain challenges. Embedded within this evolution is a gradual shift from manual to automated processes, heralding a new era of efficiency and scalability. The key characteristic defining the evolution of MRP systems is their adaptability to dynamic market conditions, marking them as a valuable asset in contemporary business landscapes. Despite their advantages in promoting streamlined operations, these systems may encounter challenges posed by compatibility issues or steep learning curves.
Importance of MRP
Enhancing Production Efficiency
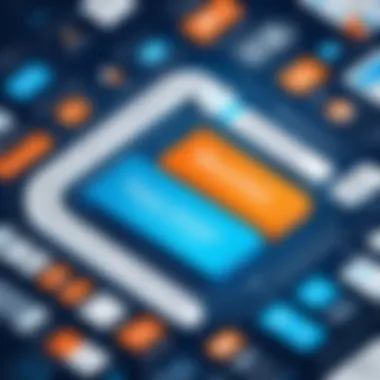
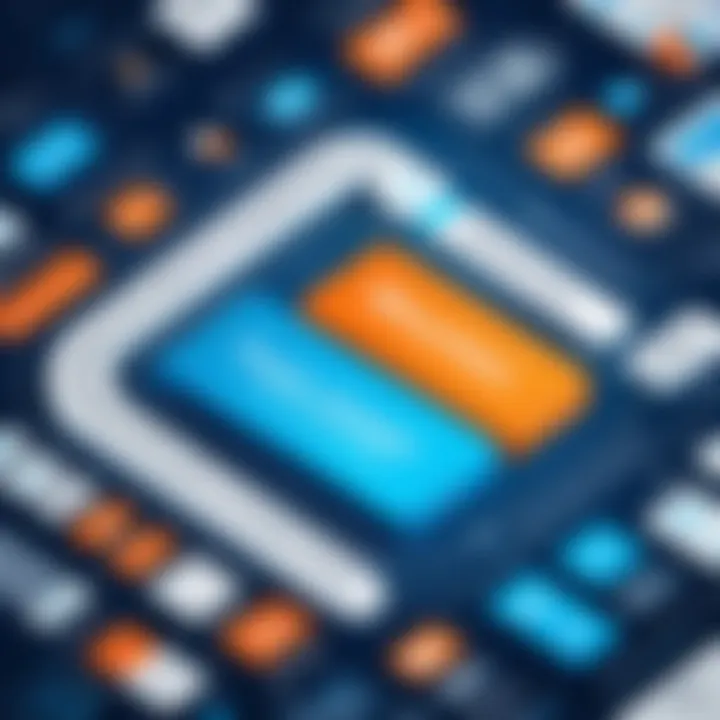
Enhancing production efficiency through MRP entails leveraging tailored strategies to optimize manufacturing processes. This pivotal aspect highlights the significance of synchronized production workflows and resource allocation. The key characteristic of this enhancement lies in its potential to reduce wastage and enhance productivity levels. Implementing this approach proves beneficial for businesses seeking sustainable growth and competitive edge. Nonetheless, a drawback could arise from operational disruptions caused by unexpected variations.
Optimizing Inventory Management
Optimizing inventory management via MRP revolves around maintaining an equilibrium between supply and demand while minimizing carrying costs. The essence of this optimization lies in its ability to prevent stockouts and excess stock accumulation. The key characteristic of this optimization is its role in fostering lean inventory practices, ensuring streamlined warehouse operations. Embracing this approach can empower businesses to streamline their procurement strategies. However, challenges may surface in accurately forecasting demand fluctuations, leading to inventory imbalances.
Key Components of MPR
Bill of Materials (BOM)
The Bill of Materials (BOM) embodies the essence of MRP by delineating the exact components and quantities required for production. This detailed roadmap plays a pivotal role in guiding manufacturing processes and ensuring supply chain integrity. The key characteristic of the BOM lies in its ability to minimize production delays and eliminate material shortages. Embracing BOM facilitates meticulous resource planning and cost optimization. However, pitfalls may emerge from inaccuracies in the BOM, leading to production bottlenecks or cost overruns.
Master Production Schedule (MPS)
The Master Production Schedule (MPS) serves as the strategic blueprint dictating production timelines and capacities. This cornerstone of MRP enables businesses to harmonize production goals with market demands effectively. The key characteristic of the MPS is its role in synchronizing various production factors to meet customer requirements efficiently. Adopting MPS empowers organizations to align production resources judiciously, optimizing output quality. Nevertheless, challenges may arise from unforeseen disruptions impacting the execution of the production plan.
Implementing MRP in Business
Implementing MRP in Business holds a crucial role within the realm of supply chain management and manufacturing. This section sheds light on the essential steps and considerations involved in incorporating Material Requirements Planning in business operations. By focusing on the specifics of Implementing MRP in Business, businesses aim to streamline their production processes, enhance efficiency, optimize inventory levels, and meet customer demand effectively. Emphasizing the significance of MRP implementation aids in achieving synchronized production and material flow, ultimately leading to improved resource utilization and cost savings.
Steps Involved in MRP
Demand Forecasting
Demand Forecasting constitutes a pivotal aspect of Material Requirements Planning, as it involves predicting future demand patterns based on historical data, market trends, and other relevant factors. The key characteristic of Demand Forecasting lies in its ability to anticipate customer needs, enabling businesses to align their production schedules and inventory levels accordingly. Demand Forecasting serves as a valuable tool for businesses, allowing them to strategize production targets, minimize stockouts, and optimize resource allocation based on anticipated demand fluctuations. Despite its advantages, Demand Forecasting may face challenges such as inaccuracies stemming from unforeseen market shifts and changing consumer preferences.
Material Requirements Calculation
Material Requirements Calculation plays a fundamental role in MRP by determining the quantity of raw materials and components needed for production based on demand forecasts and existing inventory levels. The distinctive feature of Material Requirements Calculation lies in its ability to calculate precise material needs while considering lead times, order quantities, and supplier constraints. This process facilitates timely procurement, minimizes excess inventory, and ensures seamless production processes. However, challenges such as inaccurate data inputs or sudden demand variations can impact the accuracy of material requirements calculations, potentially causing disruptions in supply chain operations.
Benefits of MRP
Reduced Lead Times
The concept of Reduced Lead Times focuses on minimizing the time taken from order placement to product delivery, optimizing production efficiency and customer satisfaction. Reduced Lead Times enable businesses to respond swiftly to market demands, reduce waiting periods, and accelerate order fulfillment processes. This benefit is particularly advantageous in fast-paced industries where timely deliveries are critical for maintaining competitiveness and customer loyalty. However, achieving reduced lead times requires streamlined processes, effective resource allocation, and operational agility to adapt to changing market dynamics.
Improved Resource Planning
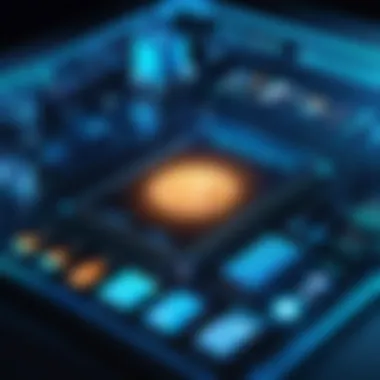
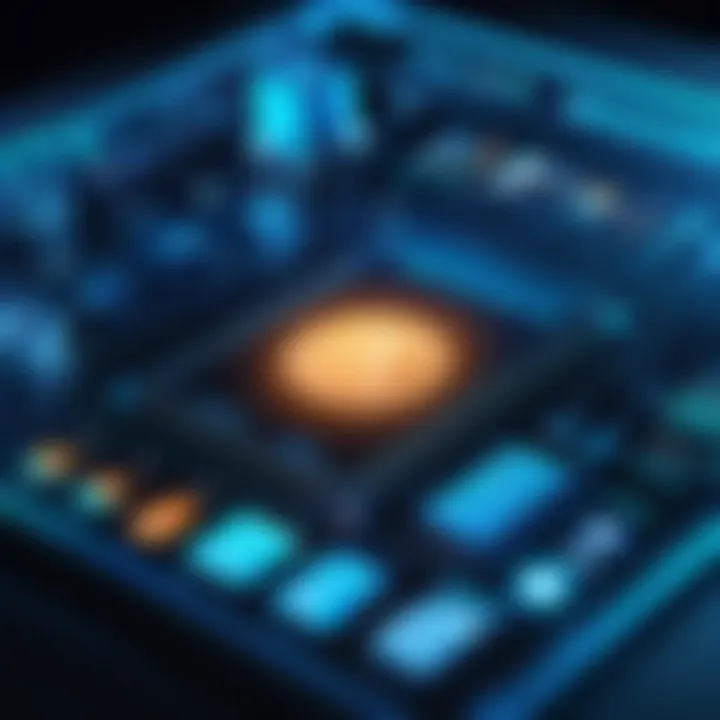
Improved Resource Planning entails optimizing the allocation of resources such as materials, equipment, and labor to meet production requirements efficiently and cost-effectively. By enhancing resource planning through MRP, businesses can avoid under or over-utilization of resources, leading to improved productivity and cost savings. The unique feature of Improved Resource Planning lies in its ability to align production schedules with available resources, reducing wastage and enhancing operational flexibility. Despite its advantages, challenges may arise in resource planning due to unforeseen disruptions, supplier delays, or inaccurate demand forecasts, necessitating continuous monitoring and adjustment.
Challenges in MRP Implementation
Data Accuracy Issues
Data Accuracy Issues present a common challenge in MRP implementation, as inaccurate data inputs can lead to faulty demand forecasts, suboptimal production schedules, and inventory imbalances. Ensuring data accuracy is critical for effective MRP utilization, as it influences decision-making processes, inventory management, and production efficiency. The key characteristic of Data Accuracy Issues revolves around the importance of reliable data sources, data validation procedures, and periodic audits to maintain data integrity and improve planning accuracy. Despite advancements in technology, data accuracy issues may persist due to human errors, system compatibility issues, or data silos within organizations.
Software Integration Challenges
Software Integration Challenges entail the complexities associated with integrating MRP systems with existing software solutions, enterprise resource planning (ERP) systems, and other digital platforms. Seamless integration of MRP software is essential for data synchronization, process automation, and real-time information sharing across departments. The key characteristic of Software Integration Challenges lies in the need for compatibility testing, data mapping, and customization to ensure smooth data flow and system usability. Despite the benefits of software integration, challenges such as system downtime, data migration complexities, and user training requirements may hinder the seamless implementation of MRP software in business operations.
Enhancing MRP Efficiency
Material Requirements Planning (MRP) is the backbone of supply chain management and manufacturing processes, ensuring streamlined operations and optimized resource utilization. In this article, we delve into the critical concept of Enhancing MRP Efficiency to underscore the pivotal role it plays in enhancing organizational productivity and profitability. By focusing on specific elements such as leveraging advanced tools and methodologies, businesses can achieve greater operational effectiveness and cost savings.
Utilizing Advanced MRP Tools
ERP Integration
Delving deeper into Enhancing MRP Efficiency, ERP Integration emerges as a cornerstone in aligning various functional areas of the organization. The integration of Enterprise Resource Planning (ERP) systems with MRP enables seamless data flow and real-time insights across departments, fostering better decision-making capabilities. The key characteristic of ERP Integration lies in its ability to synchronize production planning, inventory management, and financial data, providing a holistic view of the organization's operational landscape. Despite its advantages in streamlining processes, ERP Integration may entail challenges in terms of complex customization and initial setup costs.
Demand Planning Software
Another crucial aspect of Enhancing MRP Efficiency is the utilization of Demand Planning Software, which empowers businesses to forecast demand accurately and adapt production schedules accordingly. The key characteristic of Demand Planning Software lies in its agile forecasting algorithms, enabling proactive adjustments to changing market dynamics. This tool is a popular choice for its ability to optimize inventory levels, reduce stockouts, and improve customer satisfaction. However, the reliance on historical data and market volatility may pose disadvantages in predicting demand shifts accurately.
Continuous Improvement in MRP
Amid the dynamic business environment, Continuous Improvement in MRP practices is essential for sustaining operational excellence and meeting evolving customer requirements. Two paramount strategies, namely Kaizen Principles and Lean Manufacturing Techniques, play a pivotal role in driving operational efficiency and waste reduction within the MRP framework.
Kaizen Principles
Kaizen Principles emphasize a culture of gradual but continuous improvement, promoting employee involvement and empowerment in identifying operational bottlenecks and implementing incremental enhancements. The key characteristic of Kaizen Principles lies in their focus on small, manageable changes that cumulatively lead to significant process enhancements. This approach is beneficial for cultivating a culture of innovation and efficiency within organizations. However, challenges may arise in terms of resistance to change and the need for sustained commitment.
Lean Manufacturing Techniques
In the realm of Continuous Improvement in MRP, Lean Manufacturing Techniques stand out as proven methodologies for eliminating waste and enhancing production efficiency. The key characteristic of Lean Manufacturing Techniques lies in their systematic approach to identifying value-adding processes and minimizing non-value-adding activities. This method is popular for its ability to streamline workflows, reduce lead times, and enhance overall product quality. Nevertheless, implementation hurdles such as workforce training and cultural transformation may pose challenges during adoption.
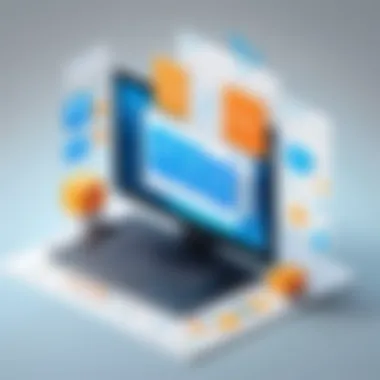
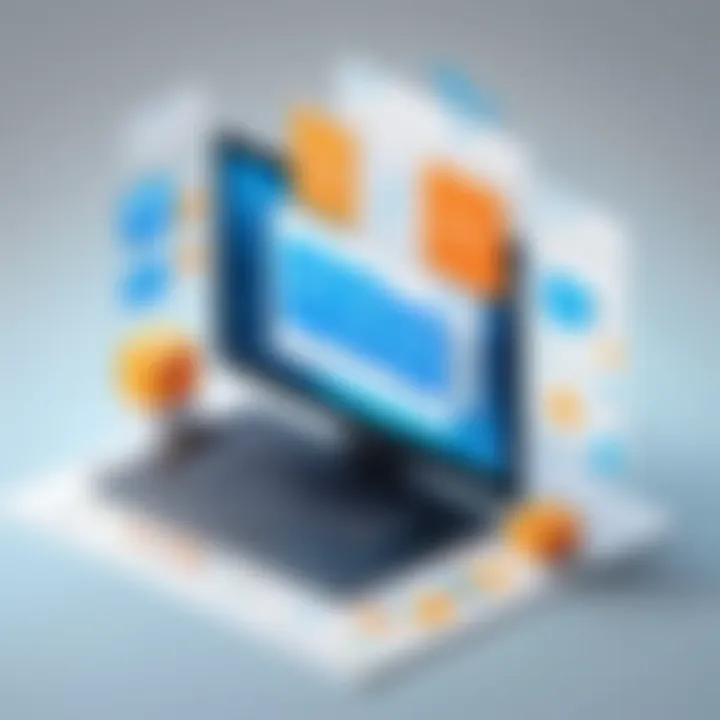
Adapting MRP to Industry 4.
As industries embrace the era of digital transformation, Adapting MRP to Industry 4.0 becomes imperative for leveraging technology advancements and market insights. Integration with IoT and Data Analytics in MRP revolutionize traditional manufacturing paradigms, enabling data-driven decision-making and predictive maintenance strategies for enhanced operational outcomes.
Integration with IoT
Integration with IoT in the MRP landscape enables real-time monitoring of production processes and inventory levels, fostering predictive maintenance and proactive resource management. The key characteristic of Integration with IoT is its ability to interconnect machines, devices, and systems, facilitating data exchange and process automation. This approach is beneficial for improving asset utilization, minimizing downtime, and enhancing overall equipment effectiveness. Despite its advantages, cybersecurity concerns and infrastructure compatibility may pose challenges in IoT integration.
Data Analytics in MRP
Embarking on the journey of Adapting MRP to Industry 4.0 involves harnessing the power of Data Analytics to glean actionable insights and optimize production workflows. Data Analytics in MRP empowers organizations to forecast demand accurately, identify inefficiencies, and drive strategic decision-making based on data-driven evidence. The key characteristic of Data Analytics in MRP lies in its capacity to analyze vast datasets and extract valuable patterns and trends, enhancing operational visibility and agility. However, challenges such as data privacy regulations and skill gaps in data interpretation may hinder seamless adoption of Data Analytics in MRP.
Future Trends in MRP
Material Requirements Planning (MRP) stands at the forefront of supply chain management, consistently evolving to adapt to the changing dynamics of the manufacturing industry. Exploring the future trends in MRP becomes paramount in understanding how businesses can stay ahead in an increasingly competitive market. As technology continues to drive innovation, embracing AI and machine learning within MRP systems becomes not just a choice but a necessity for organizations striving for operational excellence.
AI and Machine Learning in MRP
Predictive Analysis in Material Planning
Diving deeper into the realm of predictive analysis in material planning unveils a key aspect of leveraging AI in MRP. Predictive analysis facilitates forecasting material requirements with enhanced accuracy, aiding businesses in preemptively addressing production needs and potential bottlenecks. The robust predictive capabilities of AI equip organizations with actionable insights, fostering proactive decision-making and optimization of resource utilization. Unlike traditional approaches, predictive analysis offers a data-driven approach to material planning, ensuring efficiency and precision in meeting demand fluctuations.
Automated Inventory Management
Within the domain of MRP, automated inventory management emerges as a transformative element revolutionizing supply chain operations. By incorporating automated inventory management powered by AI, businesses can streamline inventory tracking, replenishment, and allocation processes. The automated system enables real-time monitoring of stock levels, automatic reordering based on preset thresholds, and intelligent categorization of inventory data. This adoption not only mitigates inventory imbalances but also minimizes the likelihood of stockouts, enhancing operational resilience and customer satisfaction.
Blockchain Technology in MRP
Enhancing Supply Chain Transparency
Incorporating blockchain technology into MRP systems amplifies the transparency and traceability aspects within the supply chain. The decentralized nature of blockchain ensures immutable and secure storage of transactional data, enhancing visibility across the supply network. Supply chain stakeholders benefit from increased trust and integrity in data exchanges, reducing instances of fraud and discrepancies. The transparent nature of blockchain bolsters collaboration among partners, fostering a cohesive and reliable supply chain ecosystem.
Immutable Record-Keeping
Immutable record-keeping represents a foundational pillar of blockchain integration in MRP, offering unparalleled data integrity and auditability. The immutability feature guarantees that once data is recorded on the blockchain, it remains tamper-proof and verifiable, establishing a single source of truth for all involved parties. This characteristic not only enhances accountability but also streamlines compliance efforts by providing a comprehensive audit trail of material flows and transactions, reinforcing regulatory adherence and operational efficiency.
Environmental Sustainability in MRP
Green Supply Chain Initiatives
The ascent of environmental sustainability in MRP heralds a paradigm shift towards eco-conscious manufacturing practices. Green supply chain initiatives advocate for the adoption of environmentally friendly strategies, such as sourcing renewable materials, optimizing transportation routes for carbon footprint reduction, and implementing efficient waste management systems. By integrating green initiatives into MRP processes, businesses can align with sustainability goals, mitigate environmental impact, and resonate with environmentally conscious consumers.
Carbon Footprint Reduction Strategies
Addressing carbon footprint reduction within MRP operations underscores a commitment to mitigating climate change and fostering ecological responsibility. Implementing strategies focused on reducing carbon emissions throughout the supply chain entails optimizing energy usage, promoting alternative transportation methods, and embracing eco-friendly packaging solutions. By proactively engaging in carbon footprint reduction efforts, organizations demonstrate corporate citizenship, differentiate themselves in the market, and contribute towards building a greener and more sustainable future.