Unveiling the Diverse Array of Welding Techniques for Various Applications
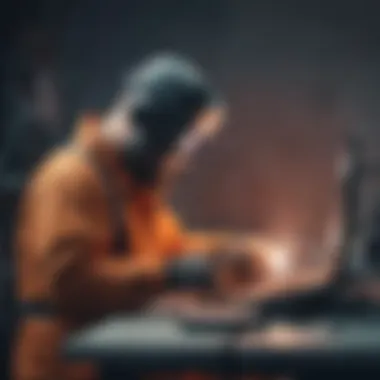
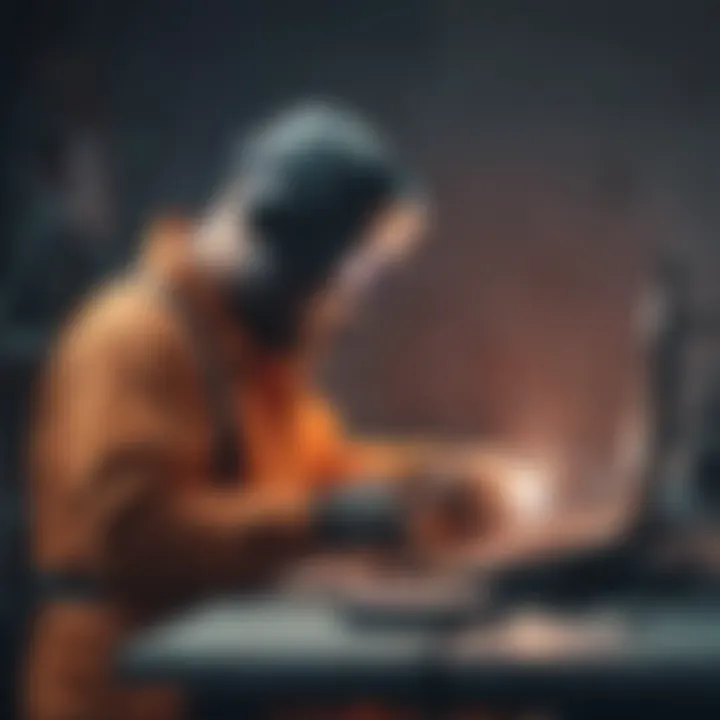
Overview of Topic
Welding techniques are at the forefront of industrial applications, spanning from traditional methods to revolutionary advancements. Understanding the diverse array of welding processes is essential for individuals embarking on a welding journey or seasoned professionals honing their craft. This comprehensive guide aims to shed light on the significance and intricacies of various welding techniques, offering insights into the art and science that underpin this crucial industrial practice.
The evolution of welding throughout history mirrors the development of industries worldwide. From the rudimentary joining of metals in ancient civilizations to the contemporary precision welding technologies employed in aerospace and automotive sectors, the transformation of welding techniques underscores the fusion of innovation and tradition in the tech industry.
Fundamentals Explained
To grasp the essence of welding, one must familiarize themselves with its core principles and terminologies. Fundamental concepts such as heat generation, metallurgy, and joint formation form the bedrock of welding. Key terminologies including arc welding, gas welding, and resistance welding demystify the lexicon of welding, empowering enthusiasts to navigate the technical landscape with confidence.
Exploring the foundational knowledge of welding not only enhances practical application but also cultivates a profound appreciation for the physics and chemistry orchestrating metal fusion. Concepts like weld pool dynamics, electrode selection, and shielding gases constitute the elemental teachings that underpin welding education.
Practical Applications and Examples
The amalgamation of theory and practice is evident in real-world welding applications. Case studies elucidate the utility of welding techniques in diverse sectors ranging from construction to artistry. Hands-on projects serve as an experiential gateway for enthusiasts to immerse themselves in the intricacies of welding, from T-joint assemblies to intricate fillet welds.
Demonstrations showcasing the step-by-step process of welding, alongside implementation guidelines, bridge the gap between theoretical knowledge and practical expertise. Embracing code snippets and operational protocols enriches the learning experience, enabling a seamless transition from theory to application.
Advanced Topics and Latest Trends
The realm of welding is not static, with innovations continually reshaping its landscape. From laser welding to 3D printing technologies, the advancements in welding techniques redefine the boundaries of possibility. Advanced methodologies like friction stir welding and electron beam welding signify the cutting-edge applications that push the boundaries of traditional welding practices.
Exploring the future prospects and upcoming trends in welding unveils a horizon brimming with potential. As industries evolve, so do welding techniques, aligning with the demands of precision engineering, sustainability, and automation. The integration of robotics and artificial intelligence heralds a new era of welding innovation, propelling industrial technologies to unprecedented heights.
Tips and Resources for Further Learning
Embarking on a welding journey necessitates a blend of theoretical knowledge and practical skills. Recommended books, online courses, and resources serve as compass points for individuals eager to delve deeper into the realm of welding. Tools and software cater to the practical implementation of welding techniques, enhancing precision and efficiency in industrial applications.
Introduction to Welding:
In understanding the significance of the "Introduction to Welding" section in this in-depth exploration of welding techniques, it is crucial to grasp the foundational knowledge that underpins the entire welding process. This segment serves as a gateway to unlocking the world of various welding methods and their applications across different industries. By delving into the basics of welding, readers can gain insights into the essential principles that govern the joining of metals, laying a solid groundwork for the subsequent detailed discussions on specific welding techniques. Understanding these core concepts is fundamental for both beginners seeking to embark on a welding journey and seasoned professionals looking to enhance their expertise in the realm of metallurgy and fabrication.
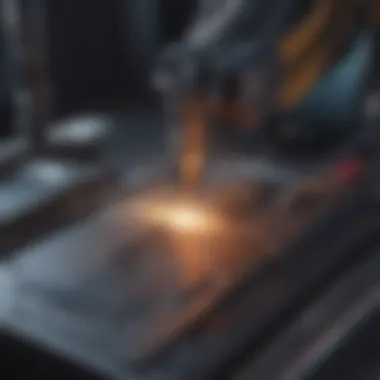

Understanding the Basics:
The Concept of Joining Metals:
Exploring the domain of the concept of joining metals elucidates the fundamental premise of welding - the art of fusing different metal components to create a unified structure. This process entails intricate metallurgical interactions that rely on heat and pressure to forge strong and durable bonds between metal pieces. The concept of joining metals highlights the versatility of welding as a fabrication technique that can seamlessly connect disparate materials, irrespective of their composition or properties. Its adaptability to a wide range of metals and alloys makes it a preferred choice across industries, where structural integrity and reliability are paramount. Despite its inherent strengths, welding's susceptibility to heat-induced deformities and the need for precise control underscore the importance of mastering this technique to achieve consistent and high-quality results.
Importance of Welding in Various Industries:
The paramount role of welding in various industries cannot be overstated, given its indispensable contribution to manufacturing, construction, automotive, and aerospace sectors, among others. Welding serves as the linchpin that holds together modern infrastructure and machinery through the seamless integration of metal components. Its significance lies in providing structural strength, ensuring operational efficiency, and fostering innovation in design and manufacturing processes across a spectrum of applications. The importance of welding in various industries underscores its pivotal role in shaping technological advancements, enhancing product performance, and meeting the ever-evolving needs of a dynamic marketplace. Despite its irreplaceable utility, the challenges of welding technology evolution and skill development pose continuous demands on industry professionals to stay abreast of emerging trends and best practices for sustainable growth and competitiveness.
Historical Evolution:
Early Methods of Joining Metals:
Tracing the origins of welding leads us to the rudimentary practices of joining metals, where early craftsmen employed primitive techniques like forge welding and brazing to create simple structures. The early methods of joining metals revolved around using heat from coal fires and manual hammering to unite metal components, marking the genesis of metallurgical craftsmanship. While these techniques laid the groundwork for modern welding practices, their labor-intensive nature and limited applicability necessitated advancements to meet the expanding industrial demands. The crude yet effective nature of early welding methods highlights the ingenuity and resourcefulness of ancient metallurgists in harnessing fire and metal to fashion tools, weapons, and architectural elements that shaped early civilizations.
Development of Modern Welding Techniques:
The evolution of welding techniques from its primitive roots to sophisticated modern methodologies is a testament to human ingenuity and technological advancement. The development of modern welding techniques marked a paradigm shift in industrial manufacturing, offering precision, efficiency, and scalability previously unimaginable. Innovations such as gas welding, arc welding, and resistance welding revolutionized the welding landscape, enabling mass production and structural fabrication on an unprecedented scale. The versatility and adaptability of modern welding techniques have opened new frontiers in engineering, construction, and aerospace industries, driving innovation and pushing the boundaries of what is achievable in metal joining and fabrication. Despite the transformative impact of modern welding technologies, the quest for continuous improvement and innovation remains a driving force for researchers, engineers, and industry stakeholders seeking to unlock the full potential of welding in the 21st century.
Types of Welding Techniques
Arc Welding
Arc welding is a fundamental welding technique that utilizes an electric arc to create a weld. It includes various methods such as Shielded Metal Arc Welding (SMAW), Gas Metal Arc Welding (GMAW), and Flux-Cored Arc Welding (FCAW). Each method has its unique characteristics, benefits, and considerations that make them suitable for specific welding applications.
Shielded Metal Arc Welding (SMAW)
Shielded Metal Arc Welding (SMAW), also known as stick welding, is a popular welding method due to its simplicity and versatility. It involves using a flux-coated consumable electrode to create the weld. SMAW is widely used in industries that require robust and durable welds, such as construction and pipeline welding. While SMAW is known for its portability and ability to weld outdoors, it has limitations in speed and efficiency compared to other methods.
Gas Metal Arc Welding (GMAW)
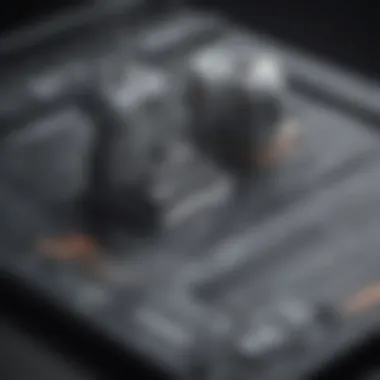

Gas Metal Arc Welding (GMAW), commonly referred to as MIG welding, is favored for its high welding speeds and ease of automation. It utilizes a continuous solid wire electrode and a shielding gas to protect the weld pool from atmospheric contamination. GMAW is suitable for welding thin to thick materials and finds applications in automotive, construction, and manufacturing industries. However, GMAW can be sensitive to wind and drafts, requiring a controlled environment for optimal results.
Flux-Cored Arc Welding (FCAW)
Flux-Cored Arc Welding (FCAW) is a versatile welding process that uses a tubular wire filled with flux to generate the arc. FCAW is known for its high deposition rates and suitability for welding thick materials. This method is commonly used in heavy fabrication and shipbuilding where high weld quality and efficiency are paramount. Despite its advantages, FCAW produces more fumes and requires proper ventilation for safe use.
Gas Welding
Gas welding encompasses techniques like Oxy-acetylene welding and Pressure Gas Welding, which rely on the combustion of gases to generate a weld. These methods offer precision and control, making them suitable for intricate welding tasks.
Oxy-acetylene Welding
Oxy-acetylene welding is a versatile process that uses a combination of oxygen and acetylene gases to produce a high-temperature flame for welding. It is commonly used for repairs, metal sculpture, and brazing operations. Oxy-acetylene welding provides excellent heat control and is easily portable, making it ideal for onsite welding jobs. However, it requires careful handling of flammable gases and proper safety measures.
Pressure Gas Welding
Pressure Gas Welding utilizes flammable gases under pressure to create a weld. This method is efficient for joining thin metal sheets and pipes in industries like plumbing and automotive repair. Pressure Gas Welding offers faster welding speeds compared to other gas welding methods but requires expertise to control the gas flow and pressure accurately.
Choosing the Right Welding Method
In this section, we delve into the critical aspect of selecting the appropriate welding method, a decision that significantly impacts the success and quality of welding projects. Choosing the right welding method entails considering various factors to ensure optimal results. By understanding the specifics of each welding technique, welders can address the unique requirements of different applications and industries effectively.
Factors to Consider
Material Compatibility
Material compatibility is a key consideration when selecting a welding method. Ensuring that the materials to be welded are compatible is essential for achieving strong and durable welds. Different welding techniques are suitable for specific types of materials, such as ferrous or non-ferrous metals. Factors like melting points, chemical composition, and structural integrity play a crucial role in determining material compatibility. Welders must carefully evaluate the materials involved to choose the most appropriate welding method for the job.
Joint Strength Requirements
Understanding the required strength of the weld joint is paramount in choosing the right welding method. Different applications demand varying levels of joint strength, depending on factors like load-bearing capacity, environmental conditions, and structural stability. Welders must assess the specific requirements of each project to select a welding technique that can deliver the necessary strength and durability. Factors such as weld penetration, bonding strength, and reinforcement methods influence the overall joint strength achieved through welding.
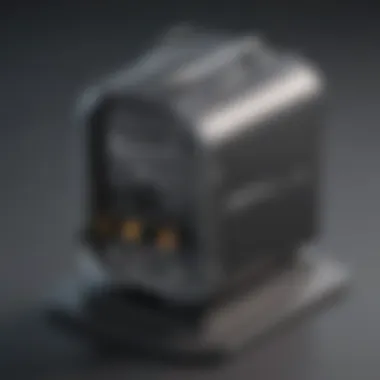
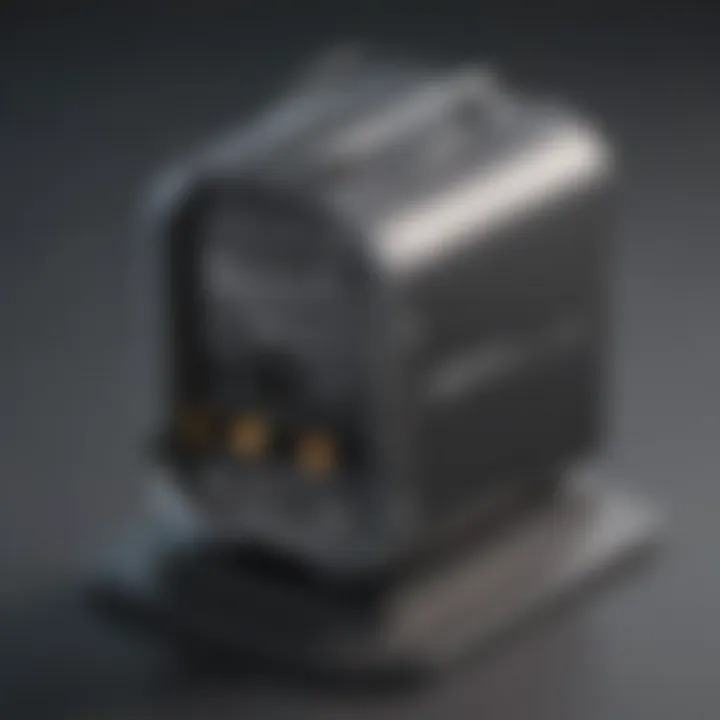
Ease of Use
The ease of use of a welding method is another significant factor to consider, especially for welders looking to optimize efficiency and productivity. Some welding techniques are more user-friendly and require less skill and setup time, making them ideal for rapid deployment and quick project completion. Factors like accessibility, equipment complexity, and training requirements contribute to the ease of use of a welding method. Welders must weigh the trade-offs between ease of use and other critical factors like joint quality and project complexity when selecting a welding technique.
Application Specifics
Structural Welding
Structural welding plays a fundamental role in various construction and manufacturing industries as it involves joining components to create stable and durable structures. The choice of welding method for structural applications must ensure high weld integrity, load-bearing capacity, and resistance to mechanical stresses. Factors like weld placement, heat distribution, and material compatibility are essential in structural welding to guarantee the structural integrity of the final product.
Automotive Industry
Welding techniques in the automotive industry are tailored to the specific demands of vehicle manufacturing, focusing on precision, efficiency, and aesthetics. Welding methods used in automotive applications must meet stringent quality standards to ensure vehicle safety and performance. Factors such as weld quality, seam consistency, and corrosion resistance are critical considerations in automotive welding, influencing factors like assembly line speed, production costs, and overall vehicle quality.
Aerospace Applications
Aerospace welding plays a vital role in the production of aircraft and spacecraft, where safety, reliability, and performance are paramount. Welding methods for aerospace applications must meet stringent quality assurance standards and regulatory requirements. Factors like weld integrity, material fatigue resistance, and weight considerations are crucial in aerospace welding, influencing decisions on joint design, material selection, and welding process control. Attention to detail and precision are essential in aerospace welding to ensure the structural integrity and performance of aerospace components.
Mastering Welding Techniques
Training and Skill Development
Certified Welding Programs
Certified Welding Programs play a pivotal role in the journey of mastering welding techniques. These programs offer structured curriculums designed to impart a comprehensive understanding of welding principles, safety measures, and practical skills. By enrolling in certified welding programs, individuals can benefit from expert guidance, hands-on training, and exposure to industry best practices. The key characteristic of certified welding programs lies in their focus on ensuring participants acquire the necessary knowledge and skills to excel in the field. With a rigorous curriculum and assessments, these programs significantly enhance the credibility and competence of welders, empowering them to tackle complex welding tasks with confidence.
Practice and Hands-On Experience
Practice and hands-on experience form the cornerstone of skill development in welding. While theoretical knowledge is essential, applying that knowledge in practical scenarios is equally crucial. Engaging in hands-on practice allows welders to hone their techniques, improve precision, and troubleshoot common challenges effectively. The unique feature of hands-on experience lies in its ability to bridge the gap between theory and application, providing invaluable insight and confidence to welders. Hands-on experience equips individuals with the muscle memory and spatial awareness necessary to execute welds with precision and consistency, setting a strong foundation for mastering welding techniques.
Advanced Training
Specialized Welding Certifications
Specialized Welding Certifications serve as a valuable asset in the quest for mastering welding techniques. These certifications validate the expertise and proficiency of welders in specific welding processes or industries. The key characteristic of specialized welding certifications is their specialized focus on niche areas such as underwater welding, aerospace welding, or advanced techniques like robotic welding. By obtaining specialized certifications, welders can demonstrate their commitment to continuous improvement and specialization in their craft. While the advantages of specialized certifications include enhanced career prospects and industry recognition, potential disadvantages may include the need for periodic renewal and specific experience requirements.
Robotics and Automation in Welding
The integration of robotics and automation in welding signifies a significant advancement in the field, revolutionizing traditional welding practices. Robotics and automation offer precise control, greater repeatability, and increased efficiency in welding operations. The key characteristic of robotics and automation lies in their ability to perform intricate welds with consistent quality, speed, and accuracy. By leveraging robotic technology, welders can optimize production processes, reduce labor costs, and enhance overall productivity. Despite its advantages, the adoption of robotics and automation in welding may pose challenges such as initial investment costs, maintenance requirements, and the need for specialized training. However, the benefits of improved output quality and production efficiency outweigh these challenges, making robotics and automation a compelling choice for those aiming to master welding techniques.