The Critical Role of Certified Electrical Safety Gear in Workplace Protection
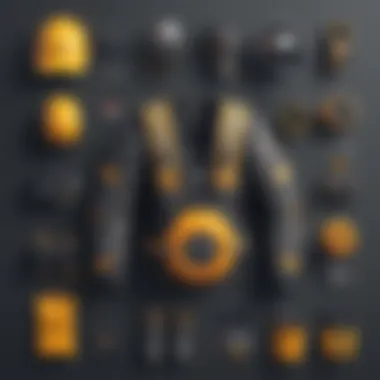
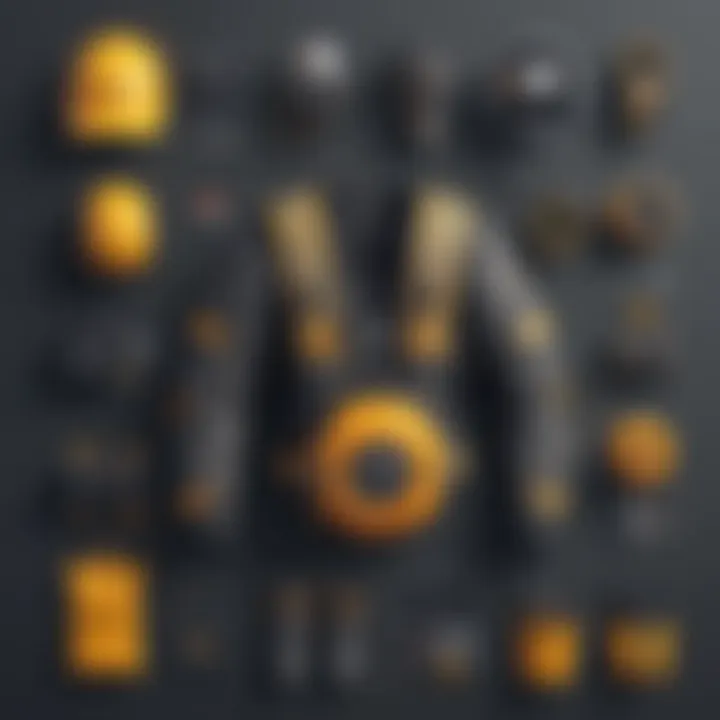
Overview of Topic
In delving into the essentiality of employing verified electrical safety equipment, it becomes apparent how crucial it is to prioritize individual well-being when dealing with electrical currents. From protective gear like insulated gloves to voltage detectors, each component plays a vital role in averting potential hazards in diverse workplaces. The intrinsic value of such gear lies in mitigating risks and upholding safety standards within the tech industry, safeguarding personnel from unwanted electrical mishaps.
Fundamentals Explained
Practical Applications and Examples
Real-world scenarios exemplify the critical role that certified electrical safety gear plays in preventing accidents and ensuring occupational well-being. Through case studies detailing incidents where protective gear mitigated potential electrical harms, individuals can grasp firsthand the impact of utilizing certified equipment. Hands-on demonstrations further reinforce the importance of proper gear selection and usage, offering practical insights for implementing safety measures effectively in different settings.
Advanced Topics and Latest Trends
As technology advances, so too does the realm of certified electrical safety gear. Stay abreast of cutting-edge developments in equipment design and safety protocols. Explore advanced methodologies for enhancing electrical safety practices in the workplace, ensuring future prospects align with the evolving landscape of electrical safety standards and innovative trends within the industry.
Tips and Resources for Further Learning
For individuals keen on expanding their knowledge of certified electrical safety gear, a plethora of resources await. From recommended readings on industry standards to online courses focusing on electrical safety protocols, ample opportunities exist for further learning and skill development in the realm of electrical safety. Discover essential tools and software aimed at enhancing practical application of safety guidelines, propelling individuals toward a holistic understanding of electrical safety practices.
Introduction
In the realm of working with electricity, one cannot underestimate the paramount importance of utilizing certified electrical safety gear. These safety measures are not merely optional accessories but serve as vital shields that safeguard individuals against potential electrical hazards that lurk in various work environments. The significance of this topic lies in its potential to avert catastrophic consequences and ensure the well-being of those exposed to electrical risks. Understanding the essential role of certified safety gear is fundamental in creating a secure working atmosphere where individuals can execute their tasks with minimized threats to their safety and health.
Understanding Electrical Hazards
In this section, we will delve into the pivotal aspect of understanding electrical hazards, which is crucial in comprehending the essence of employing certified electrical safety gear. Understanding electrical hazards provides individuals with the knowledge needed to identify, mitigate, and prevent potential risks related to electricity. By grasping the types of electrical hazards and their underlying causes, individuals can adopt proactive measures to safeguard themselves and others in the work environment.
Types of Electrical Hazards
Electric Shock
Electric shock is a prevalent electrical hazard characterized by the flow of electric current through a person's body. This phenomenon can result in severe injuries or even death, underscoring its significance in the realm of electrical safety. Electric shock is a primary concern in this article due to its immediate and profound impact on individuals exposed to electricity.
Electrocution
Electrocution, in contrast to electric shock, involves a fatal outcome caused by the passage of electricity through the body. Its portrayal as a distinct hazard serves to highlight the irrevocable consequences of disregarding electrical safety protocols. Clearly outlining the risks associated with electrocution reinforces the imperative nature of prioritizing safety measures.
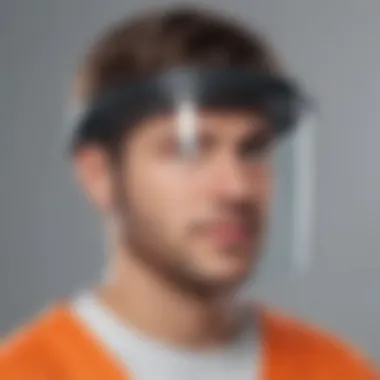
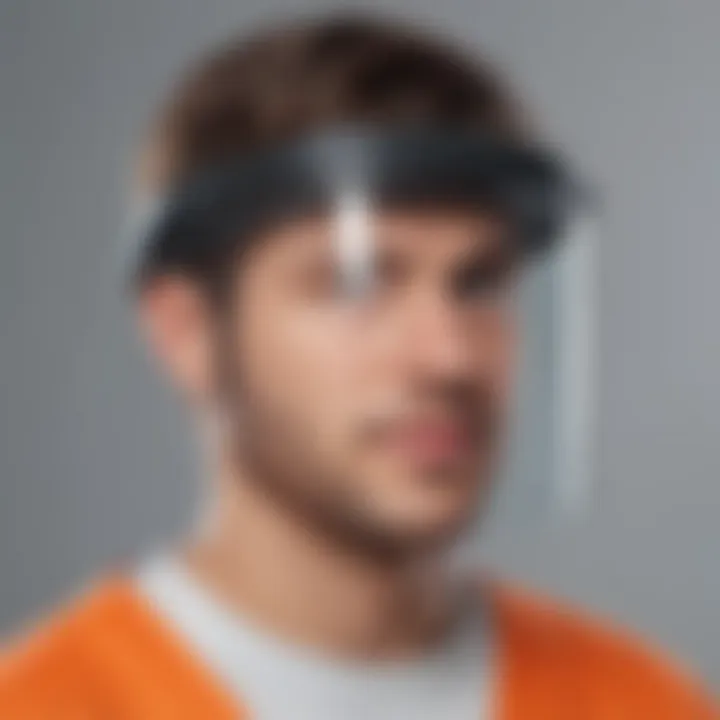
Arc Flash
Arc flash pertains to the release of intense radiant energy during an electrical fault, capable of causing severe burns and other grave injuries. Its feature as a sudden and violent event accentuates the criticality of implementing preventative strategies to avert such occurrences. Exploring the specificities of arc flash elucidates the measures necessary for mitigating its hazardous outcomes.
Arc Blast
Arc blast is characterized by the high-pressure wave generated during an arc flash event, posing additional dangers to individuals in proximity. Its distinct nature underscores the comprehensive approach required in addressing electrical hazards, encompassing not only the initial flash but also its consequential effects. Understanding the dynamics of arc blast fosters an encompassing grasp of electrical safety protocols and risk mitigation strategies.
Common Causes of Electrical Accidents
Contact with Energized Parts
Contact with energized parts accounts for a significant portion of electrical accidents, emphasizing the paramount importance of adhering to safety regulations and utilizing proper gear. Its prevalence underscores the need for in-depth understanding and effective prevention measures to mitigate associated risks.
Overloaded Circuits
Overloaded circuits pose a constant threat within electrical environments, with the potential to ignite fires or cause equipment damage. An exploration of the intricacies surrounding overloaded circuits enhances awareness and emphasizes the critical role of preventative maintenance and gear utilization.
Faulty Equipment
Faulty equipment stands as a common catalyst for electrical accidents, showcasing the repercussions of neglecting maintenance and quality control. Highlighting the risks tied to faulty equipment underscores the necessity of regular inspections and adherence to safety standards for safeguarding against potential mishaps.
Importance of Certified Safety Gear
Certified electrical safety gear holds paramount importance in ensuring the well-being of individuals tasked with handling electricity. In this article, we delve into the intricate details of why utilizing such gear is crucial in maintaining a safe working environment. By focusing on the specific elements, benefits, and considerations of certified safety gear, we aim to underscore its significance in mitigating the risks associated with electrical work.
Ensuring Personal Safety
Protection from Electric Shock
Protection from electric shock is a pivotal aspect of certified electrical safety gear. Its role in safeguarding individuals from potentially life-threatening electric shock incidents cannot be understated. The key characteristic of this safety feature is its ability to act as a barrier between the electrical current and the individual, thereby preventing electricity from passing through the body. This characteristic makes it a popular choice due to its effectiveness in reducing the severity of shock injuries. Additionally, the unique feature of insulation in protection from electric shock provides insulation against electric current, minimizing the risk of accidents.
Prevention of Arc Flash Incidents
Prevention of arc flash incidents is another crucial facet of certified safety gear. By mitigating the risks associated with arc flashes, this feature significantly reduces the probability of severe injuries in the workplace. The key characteristic lies in its capacity to withstand and dissipate the heat and energy generated during an arcing fault, thereby preventing the escalation of an arc flash. This proactive measure is highly beneficial, considering the devastating impact arc flashes can have on individuals. Despite its significance, one must be aware of the limitations in preventing all arc flash incidents, underscoring the need for comprehensive safety protocols.
Compliance with Regulations
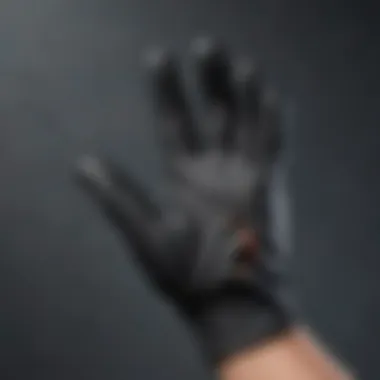

OSHA Standards
Adhering to Occupational Safety and Health Administration (OSHA) standards is imperative in the realm of electrical safety gear. OSHA standards set forth the guidelines and requirements that employers must follow to ensure a safe working environment for employees. The key characteristic of OSHA standards is their meticulous focus on various aspects of electrical safety, from equipment specifications to training mandates. This commitment to detail makes OSHA standards a popular choice for organizations seeking to prioritize worker safety. However, it is essential to note that adherence to these standards requires continuous monitoring and updates to align with evolving safety practices.
NFPA Requirements
Following the National Fire Protection Association (NFPA) requirements is crucial for enhancing workplace safety. NFPA requirements offer comprehensive directives on fire protection and electrical safety, aiming to prevent accidents and injuries. The key characteristic of NFPA requirements is their holistic approach to safety, encompassing various elements such as risk assessment, safety protocols, and emergency response measures. This all-encompassing nature makes NFPA requirements a favored choice for organizations seeking robust safety frameworks. Nevertheless, incorporating NFPA requirements necessitates diligence in implementation and regular reviews to ensure compliance and effectiveness.
Types of Certified Electrical Safety Gear
In this section, we delve into the crucial topic of Types of Certified Electrical Safety Gear, examining the significance and impact of utilizing appropriate gear in ensuring workplace safety. Certified safety gear plays a pivotal role in safeguarding individuals working with electricity, mitigating potential risks, and preventing accidents. By understanding the distinct types of safety gear available, individuals can make informed decisions to protect themselves adequately.
Insulating Gloves
Insulating gloves are a fundamental component of electrical safety gear, providing insulation and protection against electric shock when working on energized equipment.
Class Gloves
Class 0 gloves are designed to withstand up to 1,000 volts, offering reliable protection for low-voltage applications. Their unique feature lies in their ability to provide adequate insulation while allowing dexterity for intricate tasks. Class 0 gloves are a popular choice for their balance of protection and maneuverability, making them essential for tasks requiring precision in a potentially hazardous environment.
Class Gloves
Class 1 gloves are crafted to endure voltages up to 7,500 volts, catering to a broader range of electrical work with medium voltage requirements. The key characteristic of Class 1 gloves is their enhanced insulation properties, ensuring a high level of protection for users. Their durability and reliability make them a favored option for tasks that involve moderate electrical risks.
Class Gloves
With the capacity to withstand voltages up to 17,000 volts, Class 2 gloves offer robust protection for high-voltage operations. The key feature of Class 2 gloves is their ability to shield users from significant electrical hazards, making them indispensable for tasks involving substantial risks. While providing enhanced protection, these gloves may slightly compromise dexterity due to their increased insulation thickness, balancing safety and practicality effectively.
Protective Clothing
Additionally, protective clothing such as arc-rated clothing and flame-resistant coveralls are essential elements of certified electrical safety gear, further ensuring the well-being of individuals working in hazardous electrical environments.
Arc-Rated Clothing
Arc-rated clothing is inherently flame-resistant and designed to prevent ignition and provide thermal protection during arc flash incidents. Its key characteristic lies in its ability to self-extinguish, reducing the risk of burn injuries. Arc-rated clothing is a vital choice for individuals exposed to arc flash dangers, offering unparalleled protection and peace of mind in high-risk scenarios.
Flame-Resistant Coveralls
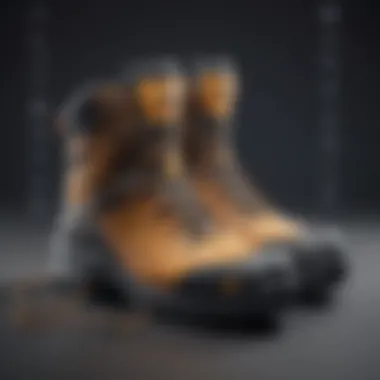
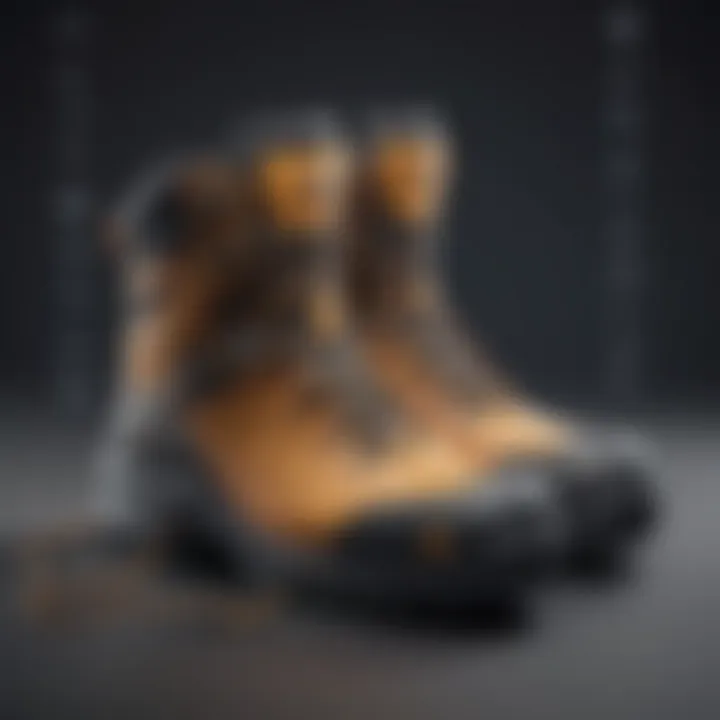
Flame-resistant coveralls are engineered to resist ignition and protect users from flames and heat. The primary feature of flame-resistant coveralls is their ability to shield the wearer from intense heat and flames, maintaining a safe environment in volatile settings. Their durability and effectiveness in preventing burn injuries make them a highly favored option for individuals working in environments prone to fire hazards.
Eye and Face Protection
Moreover, eye and face protection, including face shields and safety glasses, are indispensable components of certified electrical safety gear. These protective elements offer crucial defense against flying debris, electrical arcs, and other hazards that pose risks to the eyes and face.
Face Shields
Face shields provide a clear protective barrier against various impacts and electrical hazards, safeguarding the face from potential injuries. Their key characteristic is the full-face coverage they offer, ensuring comprehensive protection for users. Face shields are a preferred choice for tasks where the face is vulnerable to hazards, providing an additional layer of safety in high-risk environments.
Safety Glasses
Safety glasses are designed to shield the eyes from flying particles, sparks, and impact hazards, preserving optical clarity and protecting against injuries. The primary feature of safety glasses is their impact resistance and clarity, ensuring enhanced visual acuity and safety. Safety glasses are an essential choice for tasks requiring eye protection without compromising visibility, offering a reliable solution for minimizing eye-related risks in diverse work settings.
Maintenance and Inspection of Safety Gear
In the realm of electrical safety, the maintenance and inspection of safety gear play a pivotal role in safeguarding individuals working with electricity. It is paramount to ensure that safety gear remains in optimal condition to provide adequate protection against potential hazards. Regular maintenance and inspection routines not only extend the lifespan of safety equipment but also enhance their effectiveness in mitigating risks. By focusing on the maintenance and inspection of safety gear, organizations can uphold a culture of safety and adherence to established protocols, promoting a secure working environment for all personnel.
Regular Inspection Procedures
Visual Checks
Visual checks serve as a fundamental aspect of safety gear maintenance, enabling a quick assessment of the gear's physical integrity. These checks involve scrutinizing the equipment for any visible signs of damage, wear, or contamination. The key characteristic of visual checks lies in their ability to detect surface-level issues that may compromise the gear's functionality. By promptly identifying and addressing visual discrepancies, organizations can prevent potential accidents and uphold the reliability of safety gear. While visual checks are essential for routine maintenance, it is crucial to supplement them with more comprehensive testing methods to ensure thorough equipment assessment.
Electrical Testing
Electrical testing constitutes a crucial component of safety gear inspection procedures, especially for gear designed to withstand electrical currents. This testing method involves subjecting the gear to controlled electrical currents to assess its insulation effectiveness and electrical resistance capabilities. The key characteristic of electrical testing is its ability to simulate real-world conditions, allowing organizations to gauge the gear's performance under duress accurately. While electrical testing provides valuable insights into safety gear functionality, it requires specialized equipment and trained personnel to execute effectively. Organizations must execute electrical testing in adherence to industry standards and manufacturer guidelines to ensure accurate results and uphold optimal safety levels.
Storage and Care Practices
Proper Cleaning
Proper cleaning is a critical aspect of safety gear maintenance, ensuring that protective equipment remains free from contaminants and debris. This practice involves using appropriate cleaning agents and techniques to sanitize gear surfaces and maintain their integrity. The key characteristic of proper cleaning is its role in preventing material degradation and preserving the gear's protective properties. By adhering to regular cleaning routines, organizations can prolong the lifespan of safety gear and minimize the risk of bacterial or chemical contamination. While proper cleaning enhances the durability of safety equipment, it is essential to follow manufacturer recommendations to avoid damaging gear components.
Secure Storage
Secure storage practices are essential for preserving safety gear when not in use, safeguarding it from environmental elements and physical damage. This practice involves storing gear in designated areas away from moisture, heat, or direct sunlight to prevent degradation. The key characteristic of secure storage lies in its ability to maintain safety gear's structural integrity and protective qualities over time. By adopting secure storage practices, organizations can ensure that safety gear remains readily accessible and in optimal condition for use. While secure storage minimizes potential risks associated with gear damage or contamination, it is vital to inspect storage facilities regularly and address any issues promptly to uphold safety standards.
Conclusion
Certified safety gear goes beyond mere compliance; it serves as a proactive measure in mitigating risks associated with electrical work. Protection from electric shock and prevention of arc flash incidents are paramount, and insulating gloves, protective clothing, eye, and face protection form the frontline defense against these hazards. Choosing the appropriate class of gloves and ensuring the quality of protective clothing can mean the difference between a safe work environment and a potential catastrophe.
Moreover, through regular inspection procedures like visual checks and electrical testing, users can actively monitor the condition of their safety gear, identifying any signs of wear or damage that could compromise their effectiveness. Proper storage and care practices further contribute to extending the lifespan of safety equipment, ensuring that it remains reliable and durable over time.
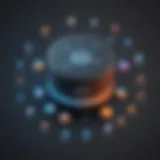
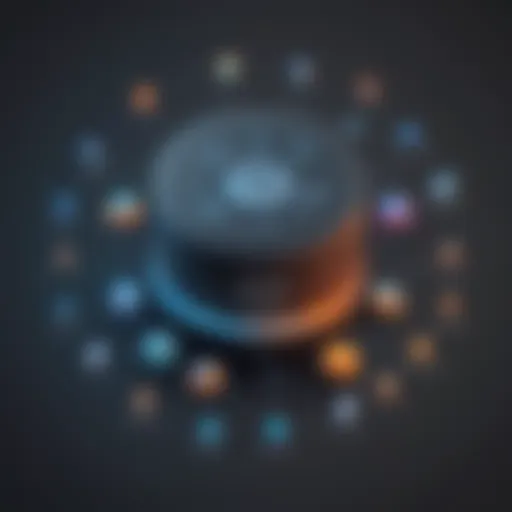