Unlocking Logistics Efficiency with MRP Systems: A Comprehensive Guide
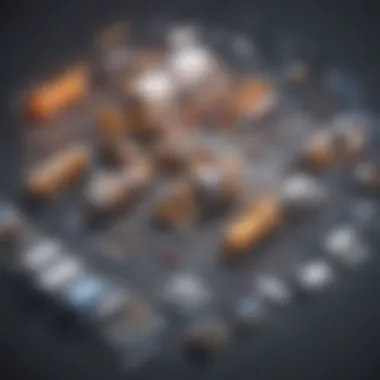
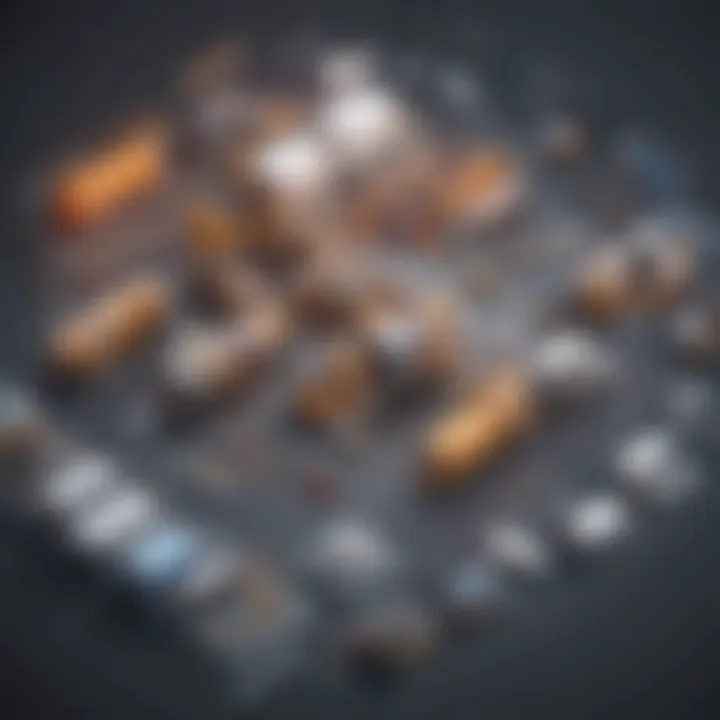
Overview of Topic
In the realm of logistics optimization, the integration of Material Requirements Planning (MRP) systems plays a pivotal role. A fundamental understanding of how MRP systems streamline inventory management, production planning, and resource allocation is crucial for enhancing operational efficiency within various industries, particularly in the tech sector. The historical evolution of MRP systems showcases a paradigm shift in supply chain management, laying the groundwork for contemporary logistics optimization strategies.
Fundamentals Explained
Practical Applications and Examples
Real-world case studies offer compelling narratives of how MRP systems have revolutionized logistics operations. From large corporations to small businesses, the implementation of MRP systems has yielded tangible benefits, streamlining supply chains and mitigating operational inefficiencies. Hands-on projects provide a practical demonstration of how organizations can leverage MRP systems to optimize resource utilization and enhance overall productivity.
Advanced Topics and Latest Trends
The landscape of logistics optimization is continuously evolving, with cutting-edge developments reshaping traditional paradigms. Advanced techniques such as predictive analytics and machine learning algorithms are spearheading a new era of data-driven decision-making in supply chain management. By exploring these innovative methodologies, professionals can stay abreast of the latest trends and anticipate future prospects within the realm of logistics optimization.
Tips and Resources for Further Learning
Introduction
Optimizing logistics through Material Requirements Planning (MRP) systems is a critical aspect of efficient supply chain management. In this article, we will delve into how MRP systems streamline inventory management, production planning, and resource allocation. By integrating logistics with MRP systems, companies can achieve operational excellence and enhance overall performance in a rapidly evolving market.
Understanding Logistics
Concept of Logistics
Logistics encompasses the process of planning, implementing, and controlling the efficient flow of goods, services, and information from the point of origin to the point of consumption. Its crucial role lies in optimizing operations and reducing costs across the supply chain. The meticulous coordination of logistics elements ensures seamless delivery processes and customer satisfaction. Despite its complexity, logistics serves as a strategic tool for businesses to gain a competitive edge in the market.
Importance in Supply Chain Management
Logistics holds paramount importance in supply chain management by facilitating the movement of products from suppliers to consumers. Its integration with MRP systems ensures synchronized operations and effective utilization of resources. By focusing on logistics, organizations can minimize delays, reduce inventory costs, and enhance customer service levels. The strategic management of logistics in the supply chain enables companies to respond promptly to market demands and complexities.
Exploring MRP Systems
Definition of MRP
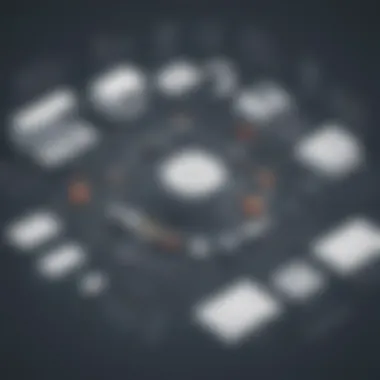
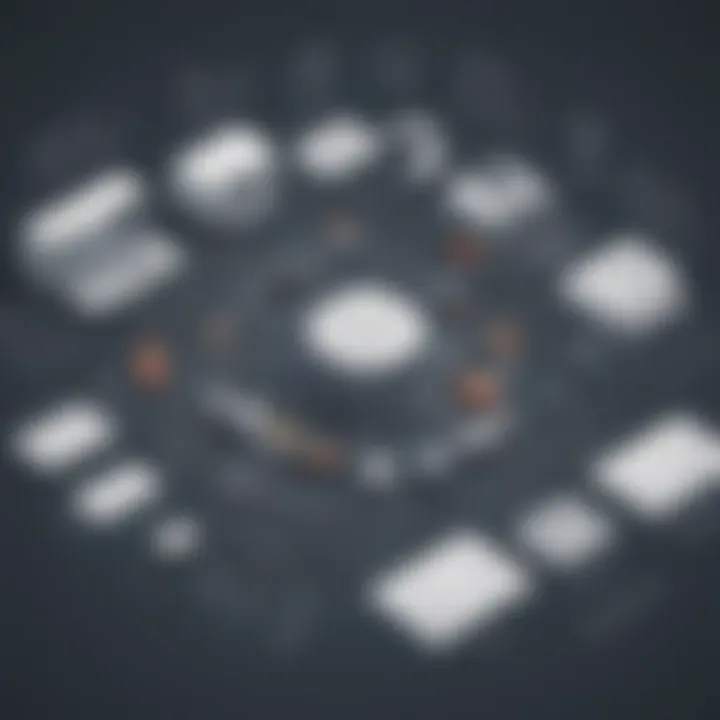
MRP is a software-based solution used in manufacturing industries to plan production activities, schedule orders, and manage inventory levels efficiently. By automating production processes, MRP systems enable companies to optimize manufacturing operations, reduce lead times, and improve productivity. The accurate calculation of material requirements in real-time is a key feature of MRP that enhances inventory management and resource allocation.
Functions and Benefits in Manufacturing
MRP systems play a vital role in coordinating manufacturing activities such as material procurement, production planning, and demand forecasting. By integrating MRP systems, manufacturers can enhance production efficiency, minimize wastages, and meet customer demands effectively. The visibility into production processes provided by MRP systems enables companies to make informed decisions and streamline their manufacturing operations.
Significance of Integration
Aligning Logistics with MRP
Aligning logistics with MRP systems allows companies to synchronize supply chain activities with production requirements seamlessly. The integration of logistics data with MRP systems enhances visibility into inventory levels, order fulfillment, and transportation processes. This alignment streamlines operations, minimizes bottlenecks, and improves overall supply chain performance.
Enhancing Operational Efficiency
Integrating logistics with MRP systems enhances operational efficiency by optimizing resource utilization and minimizing production lead times. Companies can leverage data insights from the combined system to reconfigure manufacturing processes, improve inventory turnover ratios, and respond agilely to market fluctuations. The synergy between logistics and MRP systems leads to enhanced operational agility and cost savings.
Logistics Optimization
Logistics optimization plays a pivotal role in the integration of logistics and MRP systems. It serves as a fundamental aspect in enhancing operational efficiency and streamlining supply chain processes. By focusing on optimizing logistics operations, businesses can achieve cost savings, improve accuracy, and enhance overall customer satisfaction. Logistics optimization encompasses various elements such as inventory management, production planning, and resource allocation, all of which are crucial for seamless operations and sustainable growth.
Inventory Management
Just-in-Time (JIT) Approach
The Just-in-Time (JIT) approach is a key component of inventory management that emphasizes minimizing inventory levels to reduce waste and improve efficiency. This approach involves synchronizing production with demand, ensuring that materials are received only when needed for the manufacturing process. JIT minimizes holding costs and helps in maintaining a lean inventory system, allowing businesses to respond quickly to market fluctuations. While JIT offers benefits such as cost reduction and improved inventory turnover, it also poses challenges in terms of demand forecasting accuracy and supplier reliability.
Role of MRP in Inventory Optimization
The Role of MRP in Inventory Optimization focuses on utilizing Material Requirements Planning systems to optimize inventory levels. MRP systems help in forecasting demand, planning production schedules, and managing inventory levels effectively. By integrating MRP into inventory optimization strategies, businesses can streamline their procurement processes, reduce lead times, and enhance overall operational efficiency. MRP assists in maintaining optimal inventory levels, avoiding stockouts, and minimizing excess inventory costs. However, the implementation of MRP requires accurate data input, continuous monitoring, and regular system updates to ensure its effectiveness.
Production Planning
Forecasting Techniques
Forecasting techniques play a crucial role in production planning by predicting future demand and ensuring adequate inventory levels. These techniques include quantitative and qualitative methods to anticipate market trends, customer demands, and production requirements accurately. By using forecasting techniques, businesses can optimize production schedules, prevent stockouts, and align manufacturing processes with anticipated demand. However, challenges such as demand volatility and external factors can impact the accuracy of forecasting results.

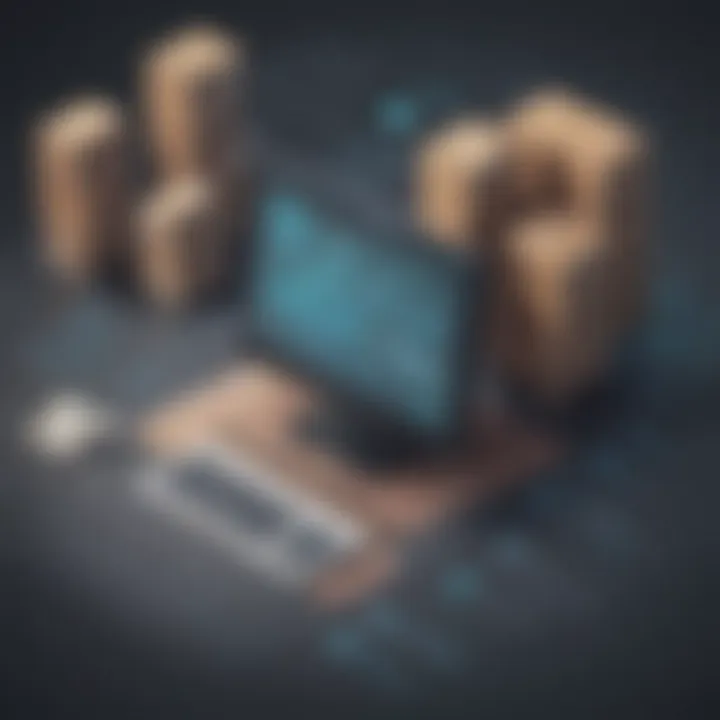
Syncing Manufacturing with Demand
Syncing manufacturing with demand involves aligning production activities with customer requirements to meet market demands effectively. By synchronizing manufacturing processes with demand forecasts, businesses can avoid underproduction or overproduction scenarios, optimize resource utilization, and enhance customer satisfaction. This approach helps in balancing supply and demand dynamics, improving production efficiency, and reducing lead times. Despite its benefits, syncing manufacturing with demand requires robust coordination between different departments and close monitoring of production workflows.
Resource Allocation
Optimizing Resource Deployment
Optimizing resource deployment focuses on efficiently allocating resources to meet production requirements and operational needs. By optimizing resource deployment, businesses can maximize the utilization of assets, minimize production costs, and improve productivity. This process involves analyzing capacity constraints, identifying resource bottlenecks, and ensuring a balanced allocation of resources across different operational areas. However, challenges such as resource scarcity, changing demand patterns, and technological constraints can impact the effectiveness of resource allocation strategies.
Balancing Demand and Capacity
Balancing demand and capacity entails managing production activities to align with fluctuating demand levels and production capacities. By maintaining a balance between demand and capacity, businesses can avoid underutilization or overutilization of resources, optimize production output, and reduce inventory carrying costs. This process involves capacity planning, demand forecasting, and production scheduling to ensure efficient resource utilization. However, variations in demand patterns, unpredictable market conditions, and supply chain disruptions can hinder the seamless balancing of demand and capacity.
Challenges and Solutions
Integration Complexity
Data Synchronization Challenges
Delving into the realm of Data Synchronization Challenges reveals a fundamental aspect of streamlining logistics through MRP systems. The unique characteristic of these challenges lies in their disruptive potential, affecting the overall synergy between logistics and manufacturing processes. By highlighting the necessity of real-time data accuracy and alignment across various departments, this article underscores the critical role of overcoming Data Synchronization Challenges in optimizing logistics operations. Despite posing certain disadvantages such as initial implementation costs and system integration complexities, the advantages of improved data integrity and operational visibility far outweigh the challenges.
Interdepartmental Coordination
Another essential component in enhancing the integration of logistics and MRP systems is Interdepartmental Coordination. The key characteristic of this aspect is its ability to foster collaboration and communication among different segments of an organization. By emphasizing the importance of shared goals and transparent information sharing, Interdepartmental Coordination plays a pivotal role in avoiding silos and promoting a holistic approach to logistics optimization. While this coordination may entail certain disadvantages like potential conflicts of interest or decision-making delays, its advantages in terms of enhanced efficiency and productivity are paramount for achieving seamless integration.
Technological Innovations
AI and Analytics in Logistics
The adoption of Artificial Intelligence (AI) and Analytics in Logistics brings a revolutionary dimension to the optimization of logistics through MRP systems. The key characteristic of AI and Analytics lies in their ability to leverage data insights for predictive analysis and decision-making. By facilitating automated route optimization, demand forecasting, and inventory management, AI and Analytics offer unparalleled benefits in enhancing operational efficiency and customer satisfaction. Although there may be challenges related to data privacy and system complexity, the advantages of improved agility and cost reduction make AI and Analytics indispensable in modern logistics optimization.
Automation in Supply Chain
Automation in the Supply Chain represents a transformative technological innovation that streamlines logistics processes and boosts overall productivity. The key characteristic of automation is its capability to reduce manual intervention in repetitive tasks, thereby freeing up human resources for value-added activities. By integrating automated systems for inventory tracking, order processing, and shipment handling, organizations can achieve greater accuracy and speed in their logistics operations. While there may be initial investment costs and adaptation challenges, the advantages of increased throughput and error reduction validate automation as a vital component of logistics optimization.
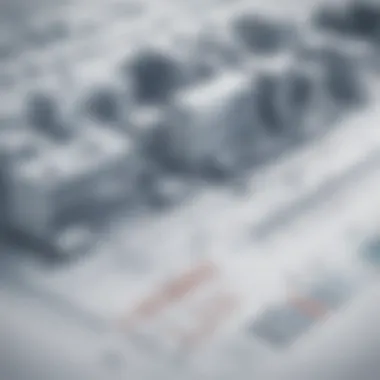
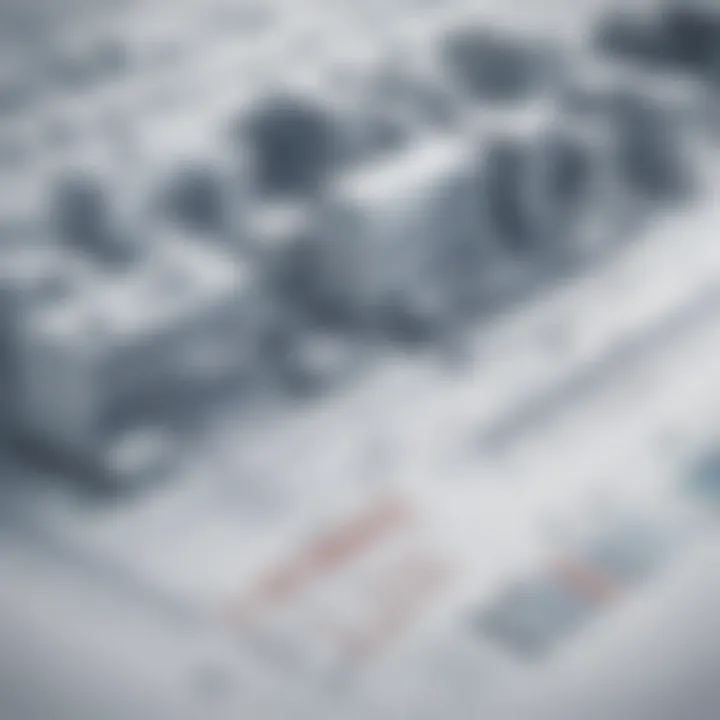
Operational Efficiency
Streamlining Processes
The optimization of logistics through MRP systems hinges on the efficient streamlining of processes within an organization's supply chain. The key characteristic of streamlining processes is eliminating bottlenecks and redundancies to enhance workflow efficiency. By implementing lean principles and continuous process improvement, organizations can achieve optimal resource utilization and cost savings. While streamlining processes may pose challenges in terms of change management and resistance to new workflows, its advantages in reducing lead times and improving service quality outweigh the initial hurdles.
Continuous Improvement Strategies
Continuous Improvement Strategies play a paramount role in sustaining and enhancing operational efficiency within logistics systems integrated with MRP. The key characteristic of these strategies is their focus on iterative enhancements and problem-solving approaches. By encouraging employee participation in identifying inefficiencies and implementing solutions, organizations can drive continuous performance enhancements and adapt to evolving market demands. While continuous improvement may require organizational culture shifts and ongoing commitment, its advantages in fostering innovation and competitiveness make it an indispensable element in logistics optimization efforts.
Future Trends
Data-driven Decision Making
Predictive Analytics in Logistics
Predictive analytics in logistics is a pivotal tool that leverages historical data and statistical algorithms to forecast future trends and outcomes. By analyzing past performance, predictive analytics enables businesses to make informed decisions, optimize processes, and mitigate risks. Its ability to identify patterns, trends, and potential issues in real-time empowers organizations to streamline operations, reduce costs, and enhance customer satisfaction. One key characteristic of predictive analytics is its predictive power, which allows companies to anticipate demand fluctuations, manage inventory efficiently, and optimize transportation routes. Although predictive analytics offers numerous benefits, such as improved forecast accuracy and resource optimization, challenges like data accuracy and model complexity may arise.
Real-time Monitoring Solutions
Real-time monitoring solutions play a vital role in optimizing logistics operations by providing instant visibility into supply chain activities and performance metrics. By tracking key performance indicators in real-time, organizations can quickly identify bottlenecks, inefficiencies, and areas for improvement. The key characteristic of real-time monitoring solutions is their ability to offer actionable insights promptly, enabling timely decision-making and proactive problem-solving. This instant access to critical data helps enhance responsiveness, agility, and overall operational effectiveness. While real-time monitoring solutions offer benefits such as improved tracking and traceability, as well as enhanced decision-making capabilities, challenges like data integration and system compatibility need to be addressed for seamless implementation.
Supply Chain Resilience
Risk Management Strategies
Risk management strategies are integral to building supply chain resilience and ensuring business continuity in the face of unforeseen challenges. By identifying, assessing, and mitigating risks proactively, organizations can safeguard their operations, customers, and bottom line. The key characteristic of risk management strategies is their preventive approach, which helps prevent disruptions, minimize losses, and maintain supply chain efficiency. Implementing robust risk management strategies not only protects against potential threats but also fosters a culture of preparedness and adaptability. While the advantages of risk management strategies include improved crisis response and reduced downtime, challenges like risk assessment accuracy and changing risk landscapes require ongoing attention.
Adapting to Market Dynamics
Adapting to market dynamics is crucial for organizations seeking to stay relevant and competitive in a rapidly changing business environment. By flexibly adjusting strategies, products, and operations in response to market trends, companies can capitalize on opportunities and address emerging challenges effectively. The key characteristic of adapting to market dynamics is the ability to embrace change, drive innovation, and meet evolving customer needs. This adaptive approach fosters agility, resilience, and sustainable growth in volatile market conditions. While the benefits of adapting to market dynamics include increased market share and customer loyalty, challenges like market uncertainty and competitive pressures necessitate strategic planning and continuous monitoring.
Sustainable Practices
Green Logistics Initiatives
Green logistics initiatives are driving the transformation of the supply chain landscape towards sustainability, environmental responsibility, and social impact. By integrating eco-friendly practices, renewable energy sources, and green technologies into logistics operations, organizations can reduce their carbon footprint, minimize waste, and support ecological conservation efforts. The key characteristic of green logistics initiatives is their focus on environmental stewardship, resource efficiency, and long-term sustainability. Embracing green logistics not only yields environmental benefits but also enhances brand reputation, stakeholder relations, and operational efficiency. While the advantages of green logistics initiatives include cost savings and regulatory compliance, challenges like initial investment costs and infrastructure upgrades require strategic planning and stakeholder engagement.
Eco-friendly Supply Chain Models
Eco-friendly supply chain models are revolutionizing the way businesses design, manage, and optimize their supply chains with sustainability in mind. By integrating eco-conscious practices, circular economy principles, and ethical sourcing strategies, companies can create value, drive innovation, and promote social responsibility. The key characteristic of eco-friendly supply chain models is their holistic approach to sustainability, balancing economic viability, environmental impact, and social considerations. Adopting eco-friendly supply chain models not only fosters a culture of environmental responsibility but also positions organizations as leaders in sustainability practices. While the benefits of eco-friendly supply chain models include reduced carbon emissions and enhanced brand differentiation, challenges like supply chain traceability and supplier collaboration warrant collaborative efforts and industry partnerships.