Mastering SMAW Welding: Techniques and Insights
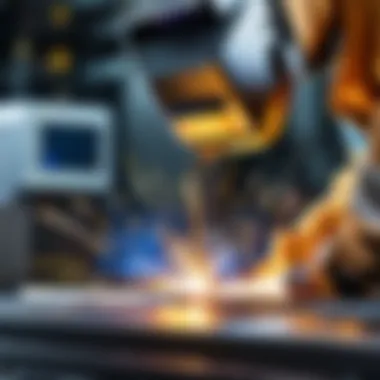
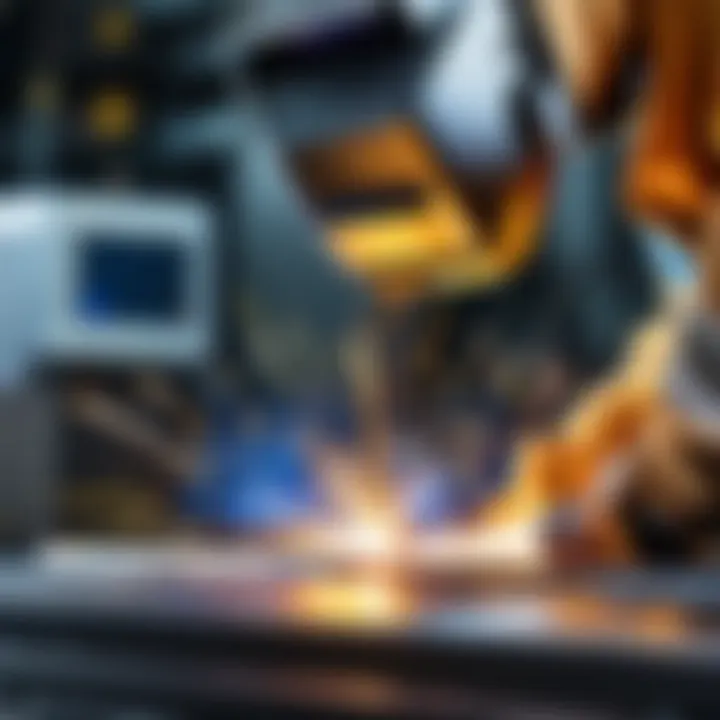
Overview of Topic
Preface to the main concept covered
Shielded Metal Arc Welding, or SMAW, stands as a cornerstone in the welding sector. This technique, often referred to as stick welding, harnesses an electric arc between a coated electrode and the base metal. The arc generates enough heat to melt the electrode, creating a filler that, along with the parent material, forms a robust joint. This method's simplicity and adaptability make it a popular choice in various applications, ranging from construction sites to shipbuilding.
Scope and significance in the tech industry
SMAW's significance stretches beyond mere metal joining; it integrates deeply within the industrial fabric. Emerging industries increasingly rely on this method due to its flexible nature and effectiveness in outdoor environments, where access to power might be limited. Furthermore, as manufacturers strive for increased efficiency, SMAW remains a go-to choice for many due to its relatively low cost and straightforward setup.
Brief history and evolution
The roots of SMAW trace back to the early 20th century, when welding technologies began to evolve rapidly. Initially developed during World War I, the process grew in popularity as both the military and civilian sectors recognized its potential. The evolution continued into the post-war era, when advancements led to enhanced techniques, electrodes, and protective gases, refining the process into what it is today.
Fundamentals Explained
Core principles and theories related to the topic
Understanding SMAW requires a grasp of its core principles. At the heart of the technique is the electric arc principle. When the electrode is brought close to the workpiece, an electric arc forms, reaching temperatures over 3,000 degrees Celsius - hot enough to melt steel! This process not only fuses the base materials but also provides a protective slag as it burns off, shielding the molten pool from contaminants.
Key terminology and definitions
- Electrode: A metallic rod coated with material that provides filler metal as it melts.
- Arc length: The distance between the electrode and the surface being welded, which directly affects the weld quality.
- Slag: A byproduct formed during welding that protects the molten weld pool as it cools.
Basic concepts and foundational knowledge
To start SMAW, one must be familiar with certain basic concepts such as:
- Maintaining proper arc length
- Controlling travel speed
- Adjusting amperage based on materials utilized
Understanding these facets is crucial for producing stable, high-quality welds.
Practical Applications and Examples
Real-world case studies and applications
SMAW finds itself in various industries, from fabricating structural steel in construction to welding pipes in oil and gas sectors. A notable example is its application in repair work; welding technicians often utilize SMAW for its ability to operate in windy conditions, making it ideal for on-site repairs.
Demonstrations and hands-on projects
For individuals eager to get hands-on, starting a small project such as constructing a metal bench can offer a practical introduction to SMAW.
- Materials Needed: Mild steel plates, SMAW electrode, protective gear, and a welding machine.
- Steps:
- Set your equipment for the correct amperage.
- Prepare the edges of the steel for welding.
- Start with short, consistent welds.
Code snippets and implementation guidelines
While SMAW doesn’t lend itself to coding as some tech topics might, the technique shares principles with coding such as precision and attention to detail. Just as a programmer must ensure quality code, a welder must ensure consistent arc length and proper material preparation for high-quality welds.
Advanced Topics and Latest Trends
Cutting-edge developments in the field
The landscape of welding technology continues to change. New innovations, like enhanced electrode coatings and power sources that offer greater control over weld characteristics, enhance traditional SMAW. When paired with automation in factories, it's possible to achieve consistent and repeatable welds.
Advanced techniques and methodologies
Techniques such as weaving patterns and using different welding positions (flat, horizontal, vertical) showcase the depth of SMAW applications. Furthermore, combining SMAW with other welding methods, such as MIG or TIG, creates hybrid processes that offer improved results.
Future prospects and upcoming trends
As industries advance, the future of SMAW lies in further automation, the integration of sensing technology, and improved training methods. Efforts to create more environmentally friendly welding practices are also on the rise, aiming to minimize the carbon footprint while maintaining efficiency.
Tips and Resources for Further Learning
Recommended books, courses, and online resources
For those looking to delve deeper into SMAW, numerous resources exist:
- Books: "Welding Principles and Applications" by Larry Jeffus provides an excellent foundation.
- Courses: Institutions like Lincoln Electric offer training programs tailored to different skill levels.
- Online resources: Websites like Wikipedia provide foundational information, while Reddit has communities like r/Welding where enthusiasts share tips and experiences.
Tools and software for practical usage
When practicing SMAW, having the right tools is key:
- Welding machine: Choose a reliable SMAW welder suitable for your applications.
- Protective gear: Prioritize safety with a helmet, gloves, and protective clothing.
- Accessories: Keep a wire brush and chipping hammer handy for cleaning welds post-application, ensuring readiness for quality inspection.
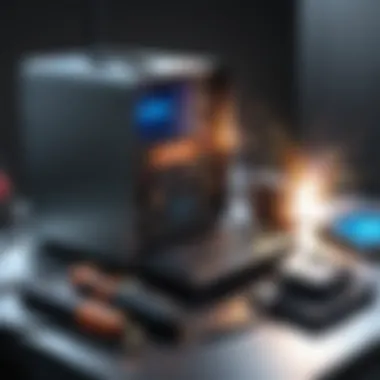
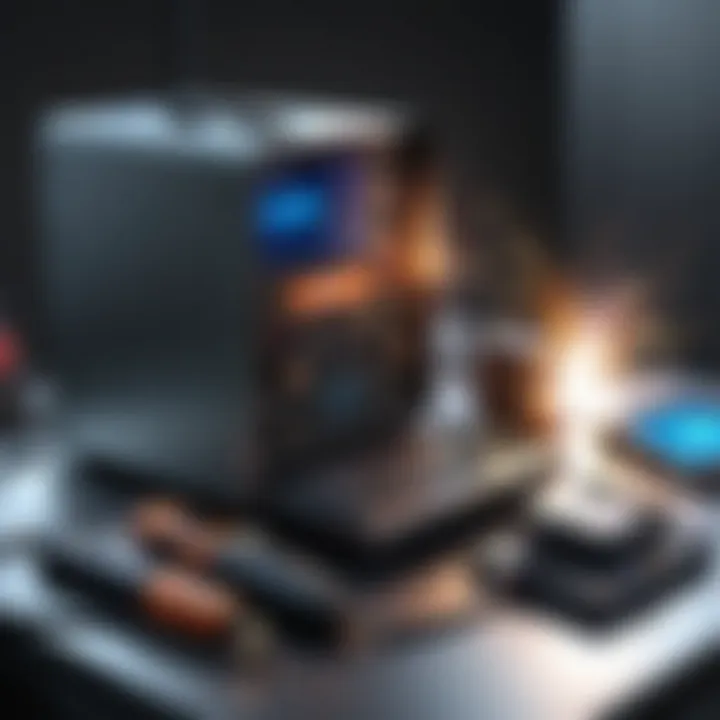
In summary, understanding SMAW welding is vital for anyone entering the welding field, promising versatility and practical applications in countless environments. Armed with this knowledge, you're on your way to mastering not just a technique, but an essential skill in modern craftsmanship.
Prelude to SMAW Welding
Shielded Metal Arc Welding (SMAW), often referred to as stick welding, stands as a cornerstone in the welding domain. It is a method that has carved out a niche not only due to its versatility but also its simplicity. This section aims to highlight the features and benefits of understanding SMAW welding, laying a solid foundation for the subsequent discussions within the article.
SMAW is favored across various industries for its ability to weld different types of metals. Its significance resonates particularly in construction, manufacturing, and repair sectors. As a result, employees with knowledge in SMAW are often sought after. Grasping the fundamental techniques of SMAW can lead to improved job prospects, making it a valuable skill in the industrial landscape.
Moreover, understanding SMAW incorporates recognizing the main benefits and considerations of the process. Not only does it offer a cost-effective solution for joining materials together, but it also requires relatively minimal equipment, making it accessible for both novices and experienced welders alike. The learning curve, while present, isn’t steep, allowing many to pick it up swiftly.
To put it succinctly, this introduction serves an essential purpose in guiding readers through the intricacies of SMAW welding. It stresses the method's relevance, underscoring the optimal practices and techniques that will be explored in more detail throughout the article. 🛠️
Definition of SMAW
SMAW, or Shielded Metal Arc Welding, is defined by its process of using a coated consumable electrode to create an electric arc between the electrode and the base metal. The arc generates enough heat to melt both the electrode and the workpiece, resulting in a molten pool that, upon cooling, forms a solid joint. The coating on the electrode plays a vital role, as it produces slag and shielding gas during the process that protect the weld from atmospheric contamination. These aspects culminate in a strong and durable weld.
Historical Background
Although the roots of welding stretch back to ancient civilizations, the formal evolution of SMAW took shape during the early 20th century. In the 1920s, engineers began exploring the potential of electric arc welding as a means of joining metal. Fast-forwarding to the 1930s, the process was refined, and SMAW began to gain popularity, especially in the post-World War II industrial boom. Its ease of use and low cost made it attractive for many manufacturing and construction projects.
The method evolved with time, incorporating various advances in technology and materials. Today, SMAW is utilized in a variety of applications, from fabricating heavy machinery to performing maintenance on pipelines. This historical context not only highlights the evolution of SMAW but also underscores its enduring significance in welding practices.
Principles of SMAW
In the world of welding, understanding the principles of Shielded Metal Arc Welding (SMAW) is akin to knowing the foundation of a building before it’s constructed. These principles serve as the bedrock for every welder, shaping their techniques and influencing outcomes. It’s not just about melting two pieces of metal; it’s about employing methodical processes that yield strong and durable joints. By grasping these foundational ideas, welders, whether novices or experienced hands, can significantly enhance their skills and results.
Basic Welding Process
At its core, SMAW is a pretty straightforward process, but it’s the nuances that turn it from simple to sophisticated. The process itself involves the use of an electrode that is coated in flux. Here’s how it typically goes:
When the electrode contacts the workpiece, an electric arc is created. This arc generates intense heat, instantly melting both the electrode and the base metal. As the electrode melts away, the coating helps maintain the stability of the arc while simultaneously releasing gases to shield the molten weld pool from contaminants and oxidation in the air.
The welder must move the electrode in a precise manner—sometimes in a straight line, other times in a zigzag—to ensure even heat distribution. This meticulous movement not only controls the heat input but also dictates the penetration and the profile of the bead. What seems simple on the surface is layered with art and technique, underscoring the importance of practice and skill.
Types of Electrodes Used
The choice of electrodes is more than a mere preference; it’s a critical factor that can influence the quality of a weld significantly. Different electrodes serve different purposes, and knowing their classifications can be the difference between a successful project and a failed one. Here are several common types:
- E6010: Common in root passes on piping and maintenance work, it provides good penetration and is often used in flat and vertical positions.
- E6011: Similar to E6010 but can be used with alternating current, making it versatile for different applications.
- E7018: Considered the go-to for structural applications, this type is favored for its smoothness and low hydrogen content, which minimizes cracking.
Understanding these electrode characteristics is crucial for selecting the correct type based on the particular material being welded and the overall project aims.
Arc Formation Mechanism
The mechanism of arc formation is vital for anyone venturing into SMAW. When the welder strikes the electrode against the workpiece, a short circuit occurs between the electrode tip and the base metal. This results in a rapid increase of temperature, causing metal at the tip to melt. The arc is maintained by the continual flow of electricity, creating a highly streamlined transfer of energy.
Welders need to regulate the distance between the electrode and the weld pool. If the electrode is too far, the arc may extinguish; too close, and it can short circuit. The ideal distance leads to a steady arc that is both controllable and productive.
The success of SMAW hinges not only on the technique but also on mastering the dynamics of arc formation—a skill that takes practice to perfect.
To become adept in SMAW, one must not only learn these principles theoretically but also apply them consistently. Welding isn't solely about hardware; it's an interplay of physics and artistry, demanding both precision and creativity. For those diving into programming or technical fields, this level of detail in mastering principles can translate into a greater understanding of systems and processes, making each of them not just a communicator but a creator.
Equipment for SMAW
When it comes to Shielded Metal Arc Welding, having the right equipment is not just a luxury; it’s an absolute necessity. The equipment you choose directly influences the quality of the welds, the efficiency of the work, and ultimately, the safety of the operator. Understanding the individual components and how they interact can make all the difference in practical applications.
Welding Machines
Welding machines are the heart of the SMAW process. There are different types of machines available, and each has its unique features, suitable for various applications.
- Transformer-based machines offer a simple, reliable way to convert high voltage to low voltage, ideal for many welding jobs, especially in the construction industry.
- Inverter-based machines are more sophisticated. They are lighter, more efficient, and can handle a wider range of input voltages. This flexibility makes them highly sought after.
One important aspect is to consider the output current and voltage settings. A machine must be able to accommodate the electrode specifications and the welding position. As a practical tip, always consult the manufacturer's guidelines to ensure the right settings for the task at hand. Whether you are in a shop or on-site, a well-chosen machine can significantly enhance your welding performance.
Welding Rods and Accessories
The choice of welding rods can significantly affect the weld’s integrity. Welding rods come in various types, each with its own specifications and uses. Basic things to keep in mind include:
- Type of metal being welded determines the flux coating of the rod.
- Diameter of the rod influences the penetration and bead size. Thicker rods may lead to wider welds but can also require more power.
- Accessories such as clamps and holders are critical for maintaining stability during the weld. Unstable placement can lead to disappointments in the final product.
Always store rods in a dry place. Moisture can interfere with the welding process, leading to an inferior weld quality. It's easy to overlook the rods, but they're just as crucial as the welding machine itself.
Personal Protective Equipment
Safety should never be an afterthought in welding operations. Personal protective equipment (PPE) is essential to prevent injuries. Here are some key components:
- Welding helmets are designed to protect the face and eyes from harmful rays and sparks. Choose a helmet with proper shading to match the welding process.
- Gloves should be heat-resistant and provide a good grip. The last thing a welder wants is losing control of the rod during a delicate operation.
- Protective clothing made from flame-resistant materials can prevent burns and other injury from hot spatter.
- Respiratory protection is important in confined spaces. Fumes from welding can be hazardous, so proper ventilation or masks should be used.
"Remember, the equipment does not work if you do not use it correctly and safely. Get yourself kitted out properly, or you might be in for a world of hurt."
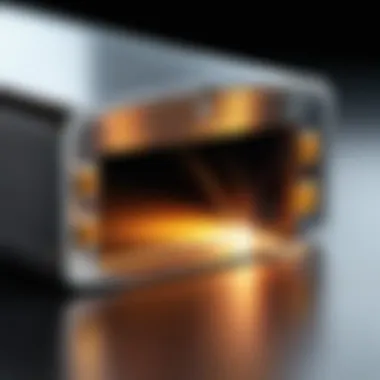
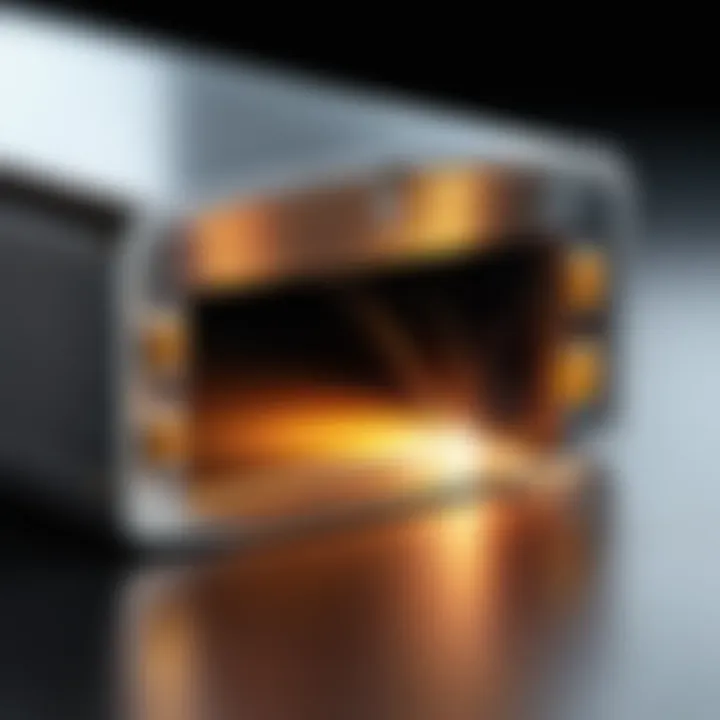
In the end, being well-equipped means not just having the best machines and rods but also prioritizing safety gear at all times. Your comfort and health should take precedence over everything else, allowing you to focus on perfecting your skill in SMAW welding.
Techniques in SMAW Welding
The realm of Shielded Metal Arc Welding (SMAW) is not just about merging metals; it's a delicate dance of techniques that can dictate the quality and strength of the weld. Understanding these techniques is vital for anyone who aims to master SMAW, whether you're new to the field or an experienced hand looking to brush up on your skills. In this section, we will explore the critical techniques used in SMAW welding, enhancing both performance and safety.
Basic Welding Techniques
When it comes to SMAW, the approach to welding can influence the final outcome significantly. Two foundational techniques stand out: stringer beads and weave patterns.
- Stringer Beads: This method involves a steady, straight motion along the joint. It allows for deeper penetration, making it ideal for thick materials. The most suitable positions for this technique include flat and horizontal.
- Weave Patterns: This technique is akin to painting with a brush, as it involves a side-to-side movement. It is particularly helpful when working with wider joints or on thinner materials, ensuring proper coverage and minimizing burn-through.
The choice between these basic techniques often hinges on the specific job requirements and material thickness. Mastery of these techniques lays the groundwork for greater complexity in SMAW.
Welding Positions
Welding positions are another essential aspect of SMAW techniques. There are four primary positions, each presenting its own set of challenges and advantages:
- Flat (1G): This is where most beginners start. The workpieces are horizontal, and the welder works from above. It typically demands less skill and provides excellent penetration.
- Horizontal (2G): Here, the workpieces are horizontal, but the welder must maneuver in a slightly different manner compared to the flat position. This position often leads to vertical welds and requires additional skill to manage puddle control effectively.
- Vertical (3G): In this position, the workpieces are vertical and finally positioned as the welder applies the electrode from bottom to top. It tests the welder’s ability to control heat and move accurately, making it more challenging than the previous two.
- Overhead (4G): Arguably the most technically demanding position, the overhead weld position requires exceptional skills. It involves welding in an upside-down manner, demanding precise control to prevent dripping and excessive pooling of molten metal.
Each of these positions influences the choice of electrode and technique, underscoring the need for adaptability in skills.
Travel Speed and Angle Considerations
The nuances of travel speed and angles in SMAW can have a profound impact on the quality of the weld. The speed at which a welder moves the electrode can affect the heat input, penetration, and overall bead profile. Here are key factors to consider:
- Travel Speed: Too fast, and you risk insufficient penetration; too slow, and you might overheat the material, resulting in distortion. Striking a harmonious balance is key to achieving a strong weld. It's essential to practice and find a rhythm that promotes both speed and quality.
- Angle of the Electrode: The angle at which the electrode is held is just as critical. Typically, a slight angle towards the direction of travel is optimal. This angle helps in forging a better arc and provides support in the molten pool. In some cases, like in vertical welding, an angle adjustment might be needed to control the flow of the weld metal.
The right technique is not merely a choice; it's an evolution of practice and experience.
Applications of SMAW
Shielded Metal Arc Welding (SMAW) is not just another technique in the vast welding toolbox; it’s one that plays a critical role across various industries. Understanding where and how SMAW is applied will help one appreciate its relevance and versatility. This section explores key areas where SMAW is indispensable, touching upon technical benefits and practical considerations.
Construction Industry
In the construction sector, SMAW is a go-to process for joining heavy structural steel components. The durability and strength achieved through SMAW make it perfect for projects that endure substantial loads and stresses. When a skyscraper is built or a bridge is erected, SMAW provides the sturdy joints needed to keep everything in place. The ability to work in various positions, whether the welder is standing on a scaffold or crouched in a tight corner, gives SMAW a unique edge.
- Key Points:
- High strength welds for structural integrity
- Versatility in different positions (flat, horizontal, vertical, and overhead)
- Robustness against environmental factors, especially in outdoor settings
Another aspect worth noting is the economic feasibility of SMAW. Equipment and consumables are often more accessible than other methods, making it a preferred choice for many construction firms operating on a budget. With the abundance of skilled welders trained in this technique, projects can proceed without major delays.
Manufacturing Sector
SMAW also finds its place in the manufacturing sector. From fabricating machinery to assembling industrial equipment, SMAW allows for swift and effective welding of different metals. This is especially true for iron and steel, which are common materials in manufacturing processes. Moreover, the controlled arc and the simplicity of this technique enable precise and consistent welding.
- Benefits in Manufacturing:
- Quick adaptability to diverse materials
- Efficiency in producing complex assemblies
- Cost-effective for smaller productions or repairs
Within the manufacturing space, one notable application is in the automotive industry. Welding components like chassis, frames, or engine parts requires precision and strength; SMAW can provide that reliably. Additionally, with innovations in electrode technology, welds are cleaner and yield better results, thus enhancing final product quality.
Repair and Maintenance Work
Repair and maintenance tasks are another domain where SMAW excels. Often, equipment and machinery may fail or suffer wear and tear, and the ability to quickly fix these issues is vital. SMAW allows for effective repairs on-site and in some cases, can even restore components to their original specifications. The portability of SMAW equipment makes it easy to transport to various locations, whether in a factory or a job site.
- Importance of SMAW in Repairs:
- Quick setup and portability provide on-the-spot solutions
- Capability to weld dissimilar metals, which is common in repairs
- Strong welds contribute to the longevity of repaired equipment
In these situations, the ability to weld without the need for external shielding gas makes SMAW particularly useful, as it circumvents the need for specialized environments. This characteristic also allows maintenance professionals to work efficiently under varied conditions.
SMAW is truly a jack-of-all-trades, adapting to the needs of construction, manufacturing, and maintenance alike, bringing strength and reliability wherever it is applied.
Advantages and Limitations of SMAW
Understanding the advantages and limitations of Shielded Metal Arc Welding (SMAW) is crucial for professionals and students alike. This section sheds light on why SMAW is so widely used in various industries, while also addressing its inherent challenges. Knowing both sides enables welders to make informed choices when selecting this method for their projects.
Benefits of SMAW
SMAW offers numerous benefits, making it a preferred choice in many welding applications. A few notable advantages include:
- Simplicity: The SMAW process is straightforward compared to some other welding techniques. It doesn't require complex equipment or extensive training, making it accessible for beginners.
- Cost-effectiveness: Unlike other welding methods that may require high setup costs or specialized equipment, SMAW has low initial investment. The equipment is relatively affordable, and the electrodes are inexpensive as well.
- Versatility: SMAW can be employed on various materials, including carbon steel, stainless steel, and some non-ferrous metals. This broad application spectrum allows welders to tackle diverse projects.
- Portability: The equipment involved in SMAW is comparatively lightweight and portable. This ease of transport makes it suitable for fieldwork, where mobility is often a concern.
- Effectiveness in Windy Conditions: The shielding from the electrode provides a degree of protection against wind and drafts. This factor enables SMAW to be effectively used in outdoor environments, which is a significant advantage in construction and repair work.
In summary, SMAW's simplicity, cost-effectiveness, versatility, portability, and resistance to outdoor conditions solidify its standing as a go-to method in various welding scenarios.
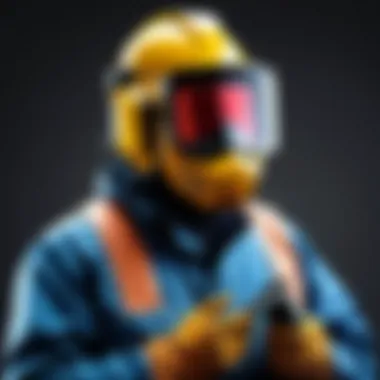
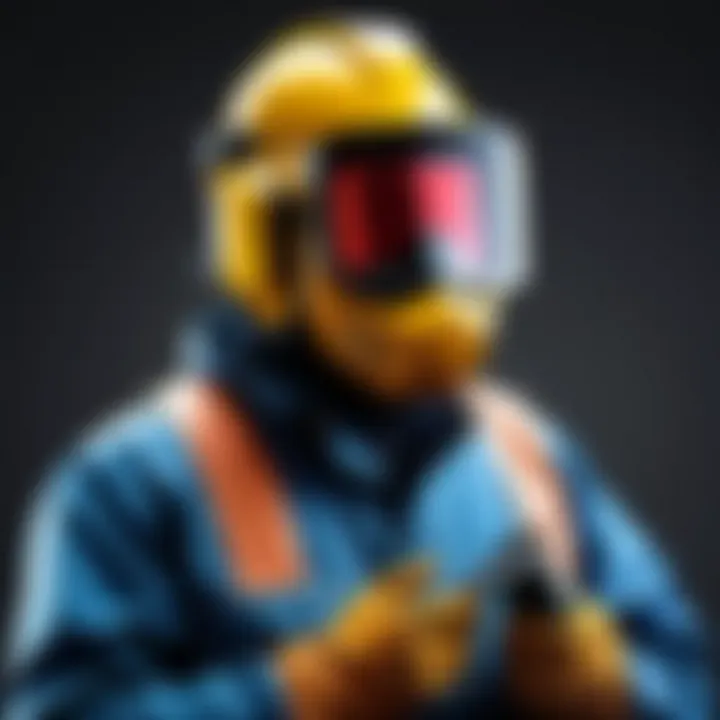
Drawbacks of SMAW
Despite its many benefits, SMAW has its share of drawbacks. Understanding these limitations allows welders to anticipate challenges and plan accordingly. Key drawbacks include:
- Slower Process: Compared to other methods like MIG or TIG welding, SMAW generally takes longer to complete. This slower pace can become a significant factor when working on large projects or under tight deadlines.
- Limited Control: While SMAW provides a solid weld, achieving precision can sometimes be difficult. Factors such as electrode size and position can affect the final result, requiring welders to possess a precise skill set.
- Fume and Slag Generation: The process generates a notable quantity of fumes and slag, which can pose health risks. Proper ventilation and protective equipment are necessary to mitigate these issues.
- Surface Preparation: SMAW requires a clean surface for optimal results. Contaminants can lead to subpar weld quality, meaning more time must be spent on surface preparation compared to some other welding procedures.
- Position Limitations: Welding in certain positions can complicate the process, making it difficult to maintain an effective arc or achieve a good finish. Skills in various positions are essential to mitigate this issue.
These limitations, while significant, can be managed with appropriate training, tools, and techniques. Ultimately, knowing both advantages and drawbacks equips welders with the necessary knowledge to navigate their respective projects confidently.
"Understanding the pluses and minuses of your welding methods leads to stronger results and safer practices."
By keeping these benefits and drawbacks in mind, individuals can make astute decisions about using SMAW in their welding endeavors.
Safety Considerations in SMAW
In the realm of Shielded Metal Arc Welding, or SMAW, safety isn't just an afterthought; it's an integral part of the craft. The process involves intense heat, bright arcs, and the potential release of harmful fumes. So, understanding and implementing safety protocols can prevent accidents and, ultimately, save lives.
Understanding Hazards
One of the first steps in maintaining safety in SMAW is recognizing the specific hazards involved. Here, hazards can range from physical injuries to exposure to hazardous materials. Common hazards include:
- Electrical Shock: Due to high voltages present in the welding machine, electrical shocks can occur if precautions aren't taken.
- Burns: The molten metal and arcs generated during welding can cause serious burns.
- Fumes and Gases: The welding process releases fumes that may contain harmful materials, leading to respiratory issues if inhaled.
- UV Radiation: Prolonged exposure to ultraviolet rays emitted from the arc can damage skin and eyes.
It's vital for welders to always be on alert for these hazards. A single lapse in attention can have grave consequences. For instance, if someone doesn’t shield their eyes properly with a suitable helmet, they run the risk of developing ‘arc eye’—a painful condition caused by exposure to the welding arc.
Preventative Measures
Once welders are aware of the hazards, the next step is to implement preventative measures. This can be the difference between a safe work environment and a hazardous one. Some key preventative measures include:
- Wear Appropriate Personal Protective Equipment (PPE): This includes gloves, protective clothing, helmets with appropriate filters, and steel-toed boots. Each item plays a critical role in shielding the welder from potential injuries.
- Maintain Equipment: Regular checks on welding machines and rods can prevent malfunctions that might lead to accidents. Ensuring that cables are intact and connections are secure is crucial.
- Ensure Proper Ventilation: Since welding creates fumes that can be harmful, working in well-ventilated areas helps mitigate inhalation risks. Using exhaust fans can further reduce fume accumulation.
- Train and Educate: Regular training programs for all welding personnel are essential. These programs should cover hazard awareness and proper equipment handling. A workforce that understands safety is a workforce that operates efficiently and with caution.
"An ounce of prevention is worth a pound of cure." When it comes to welding, this old adage rings especially true.
Despite taking all these precautions, accidents can still happen. Striving for a culture of safety where everyone looks out for one another ensures that the workplace stays secure. Every welder is part of a larger ecosystem, where their awareness can contribute to the collective safety of the group.
By being vigilant, wearing proper gear, and maintaining equipment, the industry can continue to thrive without sacrificing the well-being of its workers.
Future of SMAW Welding
The progress of Shielded Metal Arc Welding (SMAW) cannot be taken lightly. With the continuous evolution of technology and the growing demand for improved welding methods, it's vital to examine what lies ahead for SMAW. Keeping an eye on future trends allows us to adapt to advancements while fully understanding their implications.
Technological Advancements
Technological changes are shaping industries at a lightning pace. In SMAW, advancements primarily focus on equipment enhancements, automation, and welding materials.
For instance, the introduction of inverter-based power sources has provided welders with a more lightweight and efficient option, changing the game for portable welding applications. The old bulky machines that once dominated job sites are now being replaced by compact, high-tech alternatives. Not only do these inverter machines save space, but they also enhance performance and energy efficiency.
Furthermore, digital displays and smart features on welding machines enable precise control and monitoring. This is especially crucial for skilled welders looking to fine-tune their techniques. With remote diagnostics, maintenance becomes a breeze, allowing for timely interventions and preventing costly downtime.
Another notable advancement is the development of high-performance electrodes that have superior arc stability. These rods can handle a variety of materials and positions, expanding the capabilities of welders. The evolution in electrode technologies means fewer defects and a higher quality finish, meeting demanding industry standards.
Integration in Modern Industries
SMAW's future is also tied to its integration into various modern sectors. With its versatility, it's becoming increasingly relevant in industries ranging from construction to renewable energy. As construction projects increasingly adopt sustainable practices, SMAW finds its place with materials like high-strength steels that require specialized welding techniques.
Moreover, in the manufacturing sector, SMAW continues to play a significant role in fabricating heavy machinery and vehicles. As industries lean toward automation, the demand for skilled SMAW operators who can integrate traditional techniques with modern technology is growing.
The renewable energy sector, particularly the wind industry, is also seeing SMAW applications. Many wind turbines require robust welds that SMAW can deliver effectively due to its adaptability across various environmental conditions. Additionally, as governments push for more green energy initiatives, this will likely spur demand for skilled welders ready to tackle these challenging projects.
To sum it up, the future of SMAW welding is not just about keeping up with technology; it's about blending the old with the new. Practitioners need to adapt to emerging tools while maintaining the core techniques that have defined the craft. This dual approach will ensure that SMAW remains relevant for years to come, supported by both tradition and innovation.
"As technology advances, the need for skilled, adaptable welders is more important than ever."
Equipped with insights into these trends, welders and industry stakeholders can position themselves at the forefront of the SMAW sector, harnessing opportunities that arise from these changes.
End
The conclusion of an in-depth discussion on Shielded Metal Arc Welding (SMAW) plays a crucial role in reinforcing the understanding of its significance in the welding landscape. By wrapping up the concepts laid out in earlier sections, readers can better appreciate the breadth of SMAW's applications. This section not only revisits key details but also hones in on the profound implications and future possibilities for this welding method.
Summary of Key Points
To summarize the pivotal elements discussed:
- Definition and Principles: SMAW is a widely-used welding technique that relies on an electric arc to melt metals, facilitating strong joints between materials.
- Equipment: Understanding the role of welding machines, electrodes, and protective gear is crucial for safe and effective welding practices.
- Techniques: Mastery of travel speed, angles, and positions enhances the quality of the weld and overall performance.
- Applications: From construction to repair work, the versatility of SMAW makes it a go-to option across varied industries.
- Safety Considerations: Awareness of hazards and mitigative strategies is essential to protect welders and ensure workplace safety.
- Future Trends: Technological advancements continue to evolve SMAW, integrating it further into modern industrial practices.
This recap encapsulates the important threads woven throughout the article, reminding readers of why SMAW stands out among welding methods.
Final Thoughts on SMAW
As we reflect on SMAW welding, its relevance in today's industrial landscape cannot be overstated. This technique, with its robust simplicity and adaptability, caters to both novice welders and seasoned professionals. The blend of art and science embedded in SMAW showcases not only the foundational skills required but also a pathway for innovation and improvement.
Embracing SMAW involves understanding its methodologies and developing a robust safety culture. For those venturing into this field, continuous learning about best practices and emerging technologies can elevate one's proficiency. With a solid grasp of SMAW, welders can tackle a myriad of projects, contributing to advancements in engineering, manufacturing, and beyond.
As we move forward, the integration of SMAW into modern applications will serve as a testament to its enduring power and efficacy in the welding domain. The journey of mastering it is ongoing, presenting fertile ground for further exploration and growth.