Unlocking Operational Excellence: The Power of Production Order Forms
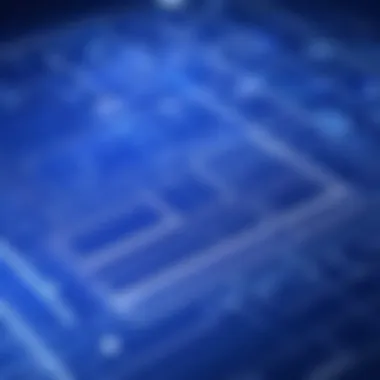
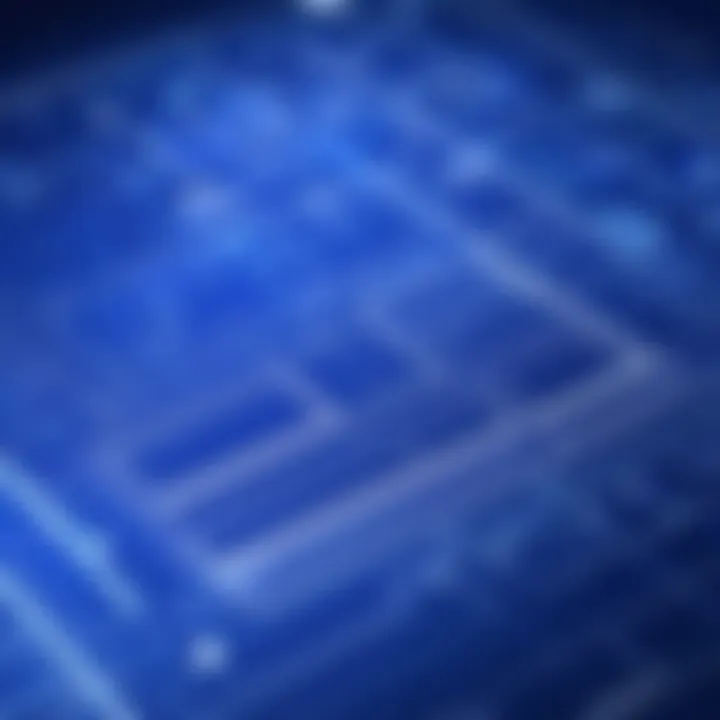
In the realm of business operations, the utilization of production order forms stands as a paramount aspect contributing to operational excellence. These forms serve as instrumental tools in enhancing operational efficiency for businesses operating in the manufacturing sector. By delving into the intricate details of production order forms, organizations can streamline their manufacturing processes, optimize resource allocation, mitigate errors, and elevate overall productivity metrics.
Fundamentals of Production Order Forms
The core principles underpinning production order forms revolve around creating a systematic and structured approach to managing manufacturing workflows. Key terminologies such as order quantities, production timelines, material requirements, and work instructions are fundamental components interwoven within these forms. Understanding these essential elements is imperative for individuals aiming to grasp the significance of production order forms within the manufacturing landscape. These foundational concepts lay the groundwork for deploying efficient production order form strategies.
Practical Applications in Manufacturing
Embarking on real-world case studies, we witness the tangible impact of production order forms on enhancing operational efficiencies across diverse manufacturing environments. Through hands-on projects and demonstrations, we gain insights into leveraging production order forms to orchestrate seamless production processes. Practical implementation guidelines, including code snippets and best practices, enable individuals to grasp the practical applications of production order forms within manufacturing settings. These examples illuminate the transformative capabilities of production order forms in optimizing resource utilization and reducing operational bottlenecks.
Advanced Strategies and Emerging Trends
As the manufacturing landscape evolves, embracing advanced techniques and methodologies becomes imperative in maximizing the efficiency of production order forms. Cutting-edge developments within this domain encompass sophisticated automation integrations, data-driven decision-making, and predictive analytics to bolster manufacturing outcomes. Exploring these advanced strategies equips professionals with the foresight to harness the full potential of production order forms in driving operational excellence. Furthermore, gaining insights into the latest trends forecast the future prospects in production order form optimization, paving the way for continuous improvements in manufacturing efficiency.
Resources for Deeper Understanding
Introduction
In the realm of business operations, the utilization of production order forms holds a pivotal position in driving efficiency and enhancing overall productivity. These forms serve as the blueprint for manufacturing processes, encapsulating vital details and instructions that streamline operations. By delving into the intricacies of production order forms, companies can revolutionize resource allocation, diminish errors, and optimize manufacturing workflows to achieve peak operational performance.
Understanding the Essence of Production Order Forms
The Purpose of Production Order Forms
Production order forms serve as the cornerstone of efficient manufacturing processes by outlining the specific requirements and instructions for production units. They facilitate a systematic approach to managing production tasks by detailing essential information such as product specifications and required quantities. The key characteristic of production order forms lies in their ability to provide a structured framework for coordinating production activities, ensuring clarity and precision in executing manufacturing tasks effectively.
Moreover, the unique feature of production order forms resides in their capacity to serve as a reference point for tracking production progress and monitoring resource utilization. By leveraging these forms, businesses can enhance operational transparency, facilitate effective communication among departments, and adhere to stringent quality standards, thus amplifying operational efficiency in the long run.
The Significance of Streamlining Processes
The significance of streamlining processes within production order forms cannot be overstated in the quest for operational excellence. By integrating streamlined procedures into production order forms, companies can minimize redundant activities, eliminate bottlenecks, and accelerate the pace of production cycles. This key characteristic fosters a culture of efficiency and agility within manufacturing operations, enabling businesses to adapt swiftly to evolving market demands.
An invaluable advantage of incorporating streamlined processes in production order forms is the optimization of resource utilization. By eliminating wasteful practices and enhancing operational efficiency, organizations can maximize their production output while minimizing costs, thereby gaining a competitive edge in the market.
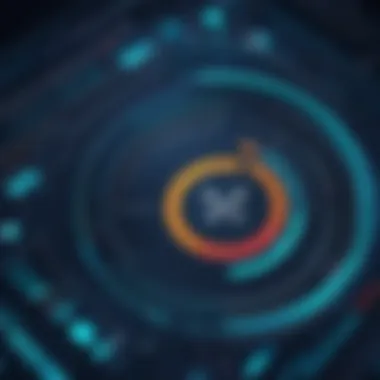
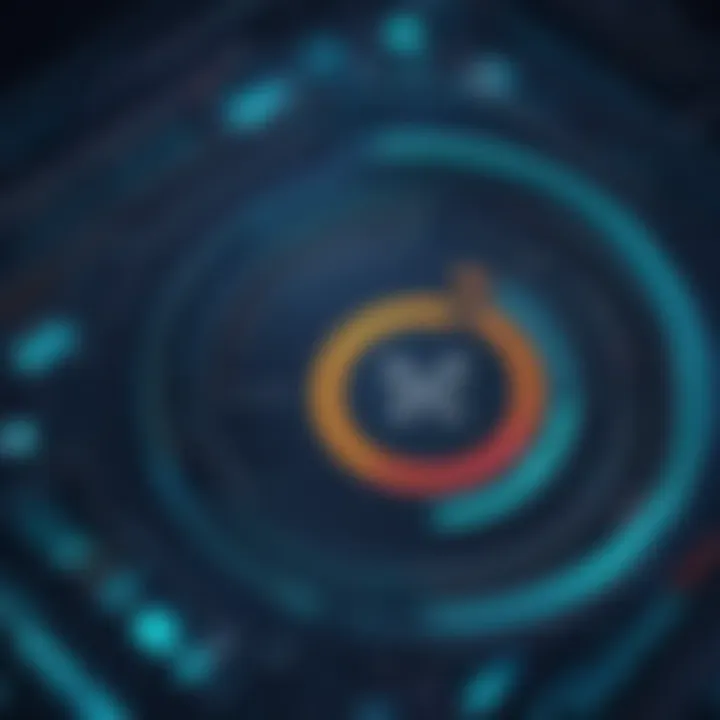
Importance of Operational Efficiency
Enhancing Resource Utilization
Enhancing resource utilization through efficient production order forms entails optimizing the allocation of materials, manpower, and machinery to maximize productivity. This specific aspect emphasizes the strategic deployment of resources based on production requirements, demand forecasts, and inventory levels. By adhering to meticulous resource allocation strategies outlined in production order forms, businesses can mitigate wastage, enhance operational flexibility, and bolster their bottom line.
Furthermore, the key characteristic of resource utilization in production order forms lies in its ability to foster a culture of sustainability and responsible resource management. By implementing practices that prioritize resource efficiency, organizations can minimize their environmental footprint, comply with regulatory standards, and build a reputation as a socially responsible entity.
Reducing Lead Times
Reducing lead times is a crucial element in enhancing operational efficiency through streamlined production order forms. This specific aspect focuses on expediting the processing of production tasks, from the initiation of orders to the final delivery of goods. By minimizing lead times, businesses can meet customer demands promptly, capitalize on market opportunities, and optimize their production capacity.
The key characteristic of reducing lead times lies in its impact on inventory management and cash flow optimization. By reducing the time taken to convert raw materials into finished products, organizations can maintain lean inventories, minimize storage costs, and improve cash flow cycles. This transformation enhances operational agility, minimizes production bottlenecks, and fosters a dynamic manufacturing ecosystem that drives sustained growth.
Elements of a Production Order Form
In the realm of manufacturing, the meticulous handling of production order forms plays a pivotal role in optimizing operational efficiency. These forms serve as the bedrock on which seamless production processes are built. By delving into the intricacies of production order forms, businesses can enhance resource utilization, minimize errors, and elevate overall productivity. The fundamental elements encapsulated within a production order form are of paramount importance, shaping the trajectory of manufacturing operations.
Essential Information
Product Specifications
Product specifications within a production order form define the core characteristics and requirements of the items to be manufactured. These specifications act as a blueprint, guiding every step of the production process with precision. By detailing aspects like materials, dimensions, and quality standards, product specifications eliminate ambiguities and pave the way for standardized production practices. Embracing detailed and accurate product specifications ensures uniformity in output, streamlines manufacturing activities, and promotes consistency in quality.
Quantity Required
The quantity required section of a production order form quantifies the exact number of units needed for production. This information is vital as it dictates resource allocation, production timelines, and inventory management. By specifying the required quantity with clarity, businesses can optimize their manufacturing processes, prevent overproduction or underproduction, and maintain efficient inventory levels. Accurate quantity requirements facilitate cost-effective production, reduce wastage, and streamline operational workflows.
Instructions and Guidelines
Production Deadlines
Production deadlines outlined in a production order form determine the timeframes within which manufacturing tasks must be completed. Efficient management of production deadlines is paramount for meeting customer demands, optimizing production schedules, and aligning processes with business objectives. By setting realistic and achievable deadlines, companies can enhance operational efficiency, ensure timely order fulfilment, and foster customer satisfaction. Adhering to production deadlines fosters discipline within the production environment, boosts productivity, and sustains a competitive edge.
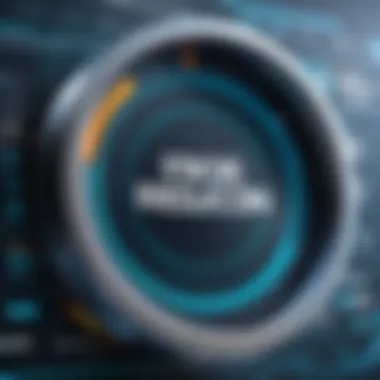
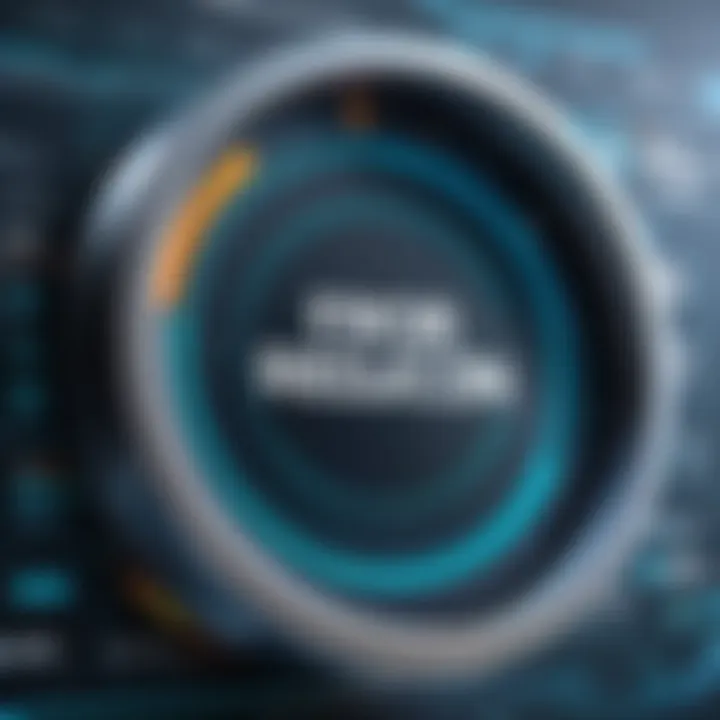
Quality Standards
Quality standards specified in a production order form establish the expected level of excellence that products must meet during manufacturing. These standards encompass criteria related to materials, workmanship, and final product attributes. By adhering to stringent quality standards, businesses can uphold their reputation, meet regulatory requirements, and elevate customer trust. Emphasizing quality standards in production processes instills a commitment to excellence, drives continuous improvement, and sets the foundation for long-term success.
Benefits of Utilizing Production Order Forms
In the realm of business operations, the significance of utilizing production order forms cannot be overstated. These forms serve as essential tools in optimizing various aspects of manufacturing processes, enhancing efficiency, and driving towards overall productivity. By implementing production order forms, companies can ensure meticulous record-keeping, streamlined communication channels, and improved coordination among different departments. Moreover, the systematic use of these forms leads to enhanced resource allocation, minimized errors, and a substantial reduction in operational costs. Embracing production order forms is not merely a choice but a strategic decision that paves the way for operational excellence and sustained growth.
Enhanced Communication
Clarity in Requirements
One of the pivotal aspects of utilizing production order forms is the clarity it provides in outlining requirements for each manufacturing task. This clarity ensures that all stakeholders involved in the production process have a crystal-clear understanding of what needs to be accomplished, the standards to be met, and the deadlines to be adhered to. By maintaining a concise and structured format for detailing requirements, production order forms facilitate seamless communication and mitigate the risks of misunderstandings or ambiguous instructions. This adherence to clarity not only expedites the production cycle but also fosters a coherent work environment where everyone is aligned towards common objectives.
Improved Coordination
Another prime benefit of incorporating production order forms is the improvement in coordination across different operational facets. These forms act as a central point of reference that enables various teams to synchronize their efforts, share critical information, and align their activities towards a unified goal. By enhancing coordination through standardized processes and clear guidelines, organizations can steer away from bottlenecks, duplications, and delays that typically impede efficiency. The improved coordination fostered by production order forms cultivates a culture of collaboration, mutual support, and collective responsibility, thereby enhancing overall operational effectiveness.
Error Reduction
Minimizing Mistakes
One of the key advantages of utilizing production order forms is the significant reduction in errors and inaccuracies throughout the manufacturing process. These forms create a structured framework for documenting specifications, instructions, and quality standards, leaving little room for interpretation or oversight. As a result, the likelihood of mistakes such as material wastage, rework, or faulty output is greatly minimized, leading to enhanced product quality and customer satisfaction. The meticulous nature of production order forms acts as a safeguard against human errors, ensuring that operations run smoothly and seamlessly.
Avoiding Misinterpretation
In addition to minimizing mistakes, production order forms play a crucial role in averting misinterpretations that often arise due to unclear or incomplete communication. By providing detailed guidelines, references, and explicit instructions, these forms leave little to no room for ambiguity or subjective understanding. This proactive approach towards avoiding misinterpretations not only safeguards the integrity of the production process but also cultivates a culture of precision, attention to detail, and accountability. Through the comprehensive nature of production order forms, organizations can mitigate the risks associated with miscommunication, fostering a work environment that thrives on accuracy and reliability.
Implementing Production Order Forms Effectively
Implementing production order forms effectively is a crucial component of enhancing operational efficiency within businesses. By focusing on this aspect, organizations can streamline their manufacturing processes, optimize resource utilization, and minimize errors. This section delves into the specific elements, benefits, and considerations associated with implementing production order forms effectively.
Training and Education
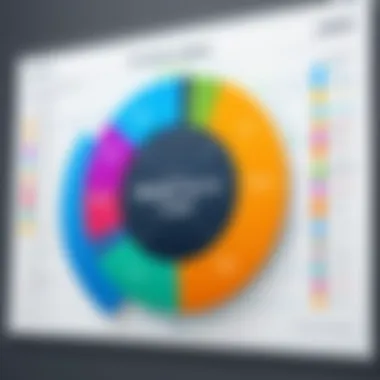
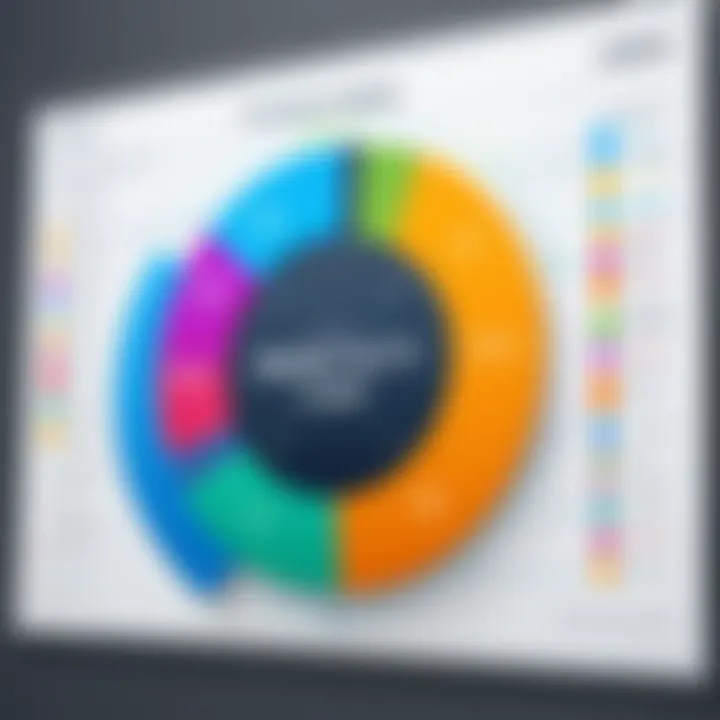
Staff Familiarization:
Staff familiarization plays a pivotal role in ensuring the successful implementation of production order forms. This process involves training employees on how to correctly fill out the forms, understand the information required, and adhere to established protocols. The key characteristic of staff familiarization lies in its ability to empower employees with the knowledge and skills necessary to execute production orders accurately and efficiently. It is a beneficial choice for this article as it directly contributes to reducing errors and enhancing overall productivity. Staff familiarization's unique feature is its capacity to instill a sense of responsibility and proficiency among workers, ultimately leading to improved operational outcomes.
Continuous Learning:
Continuous learning in the context of production order forms revolves around ongoing training and development opportunities for employees. It aims to keep staff updated on new processes, technologies, and best practices related to production orders. The key characteristic of continuous learning is its commitment to fostering a culture of growth and improvement within the organization. This approach is a popular choice for this article as it ensures that employees are equipped with the latest knowledge and skills to handle production order tasks effectively. Continuous learning's unique feature is its capacity to adapt to evolving industry standards and technologies, providing companies with a competitive edge in the market.
Integration with Technology
Digital Platforms:
Digital platforms offer a sophisticated solution for managing production order forms in a digitized environment. These platforms streamline the entire order process, from submission to fulfillment, enhancing efficiency and accuracy. The key characteristic of digital platforms is their user-friendly interface and integration capabilities with other business systems. They are a popular choice for this article as they enable seamless communication and data sharing across departments, leading to improved coordination and productivity. The unique feature of digital platforms is their ability to provide real-time insights and analytics, empowering organizations to make data-driven decisions and optimize their production processes.
Automation Tools:
Automation tools revolutionize the way production order forms are processed by automating repetitive tasks and workflows. These tools increase efficiency, reduce manual errors, and speed up the overall order fulfillment process. The key characteristic of automation tools is their ability to streamline complex procedures and minimize human intervention. They are a beneficial choice for this article as they ensure consistency and precision in executing production orders. The unique feature of automation tools is their capacity to integrate with existing software systems seamlessly, creating a cohesive digital ecosystem that maximizes operational performance.
Conclusion
Optimizing Production Processes
Driving Efficiency
Driving Efficiency within production processes is a key aspect explored in this article. By focusing on enhancing the speed and productivity of operations, Driving Efficiency aims to streamline workflows and eliminate wastage, thus bolstering organizational output and profitability. The notable characteristic of Driving Efficiency lies in its ability to identify and eliminate bottlenecks, allowing for seamless and swift progress within manufacturing systems. This aspect of the production process is indispensable for maximizing output while minimizing costs, making it a highly sought-after strategy in the realm of operational management. Despite its advantages in fueling productivity, Driving Efficiency may sometimes face challenges related to over-optimization, which could lead to potential resource constraints or quality trade-offs.
Ensuring Quality
Ensuring Quality is another fundamental aspect discussed in this article concerning production order forms. Quality assurance measures are essential in upholding product standards and meeting customer expectations. The key characteristic of Ensuring Quality lies in its commitment to meeting predefined benchmarks and specifications, thereby ensuring that end products comply with designated quality criteria. This factor is indispensable for building consumer trust and loyalty while enhancing the reputation of the brand. The unique feature of Ensuring Quality is its ability to foster long-term customer relationships and sustain competitive advantage. However, challenges may arise in balancing quality assurance with cost-efficiency, where stringent quality standards could potentially inflate production expenses.
Continuous Improvement
Adapting to Changes
The concept of Adapting to Changes plays a significant role in driving continuous improvement within production processes. By embracing adaptability, organizations can respond proactively to market fluctuations, technological advancements, and consumer preferences. The key characteristic of Adapting to Changes is its agility and flexibility in realigning strategies and operations according to evolving circumstances. This aspect is a valuable choice for this article as it underscores the importance of remaining agile in a dynamic business environment. Adapting to Changes enables companies to capitalize on emerging opportunities while mitigating risks associated with stagnation. Nevertheless, challenges may arise in managing rapid changes effectively, necessitating robust change management protocols.
Innovating Practices
Innovating Practices represent a strategic approach towards fostering continuous improvement and competitive advantage within manufacturing operations. By promoting innovation, organizations can revolutionize existing processes, products, and services to stay ahead of the curve. The key characteristic of Innovating Practices is their potential to spark creativity, efficiency, and market differentiation. This aspect is particularly beneficial for this article as it highlights the importance of innovative thinking in modern production frameworks. Innovating Practices introduce novel solutions, technologies, and methodologies to optimize operational efficiencies and drive sustainable growth. However, challenges may emerge in balancing experimentation with stability, where radical innovations could disrupt established workflows or market perceptions.
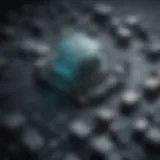
