Comprehensive Guide to Quality Control Practices
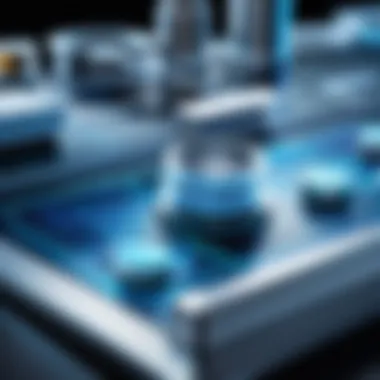
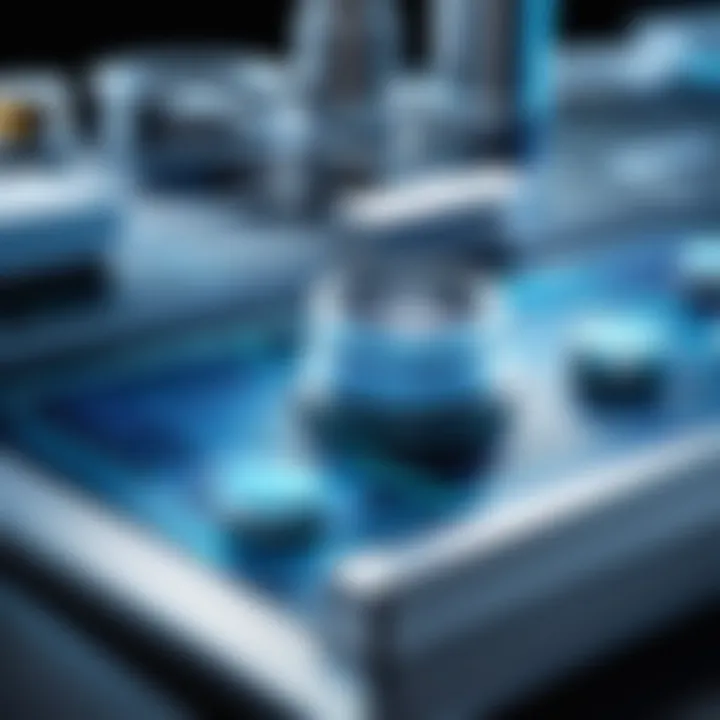
Overview of Topic
Quality control stands as a fundamental pillar in various industries, crucial for ensuring that products and services meet not just predefined standards but also customer expectations. Today, as businesses push the envelope with innovative technologies, the significance of quality control is magnified. It’s not simply a checklist of compliance; it's a strategic advantage. The journey of quality control has evolved considerably, from rudimentary inspection processes to a sophisticated amalgamation of methodologies that integrate data analytics.
From manufacturing to software development, quality control engages with a broad spectrum of sectors. The introduction of continuous improvement models and statistical process control has paved the road for heightened productivity while preventing defects from cropping up down the line. Understanding the evolution of this practice is more than just an academic exercise; it offers insight into how choices made today will shape the operational effectiveness tomorrow.
Fundamentals Explained
When diving into quality control, it’s essential to grasp its core principles. At its heart, quality control is about verifying that a product or service is produced according to predetermined standards. Here are several core principles:
- Prevention Over Inspection: It is more efficient to prevent errors than to find them post-production.
- Process Focus: Quality comes from processes; optimizing them yields better products.
- Continuous Improvement: No process is without flaws; committing to improvement is critical.
Key terminology includes:
- Defect: Any instance where a product fails to meet specifications.
- Benchmarking: Comparing processes and performance metrics to best practices from other organizations.
This foundational knowledge sets the stage for effective quality control practices in any organization.
Practical Applications and Examples
Various real-world examples showcase the practical applications of quality control methodologies. A notable illustration is Toyota’s production system. By employing just-in-time processes and rigorous quality control checks, Toyota consistently minimizes waste. This framework has become an industrial gold standard.
For those looking for hands-on experience, consider the implementation of Six Sigma in a service-oriented business. Organizations often utilize tools like DMAIC (Define, Measure, Analyze, Improve, Control) to refine their processes. A simple demonstration could involve:
- Identify a problem in service delivery.
- Measure affected metrics (like customer wait times).
- Analyze root causes.
- Implement targeted improvements.
- Control ongoing processes to maintain gains.
Advanced Topics and Latest Trends
Quality control is not stagnant; it’s an ever-evolving field. Recent advancements include:
- AI and Machine Learning: Used to predict defects before they occur based on historical data.
- Real-time Monitoring Systems: Providing immediate feedback during the production processes.
Futuristic quality assurance methods hint at a shift towards more integrated systems, relying on predictive analytics to not just respond to issues but anticipate them before they materialize.
Tips and Resources for Further Learning
For those eager to deepen their understanding of quality control, there are various resources available:
- Recommended Reading: "The Quality Toolbox" by Nancy R. Tague.
- Online Courses: Coursera offers a plethora of courses on quality management principles.
- Community Engagement: Participating in forums like Reddit can provide insights and experiences that textbooks may overlook.
Tools like Minitab for statistical analysis or ASQ templates for quality control charts can be invaluable in implementing these concepts effectively.
Understanding Quality Control
Quality control stands as a critical component in any organization aiming to uphold high standards in products and services. It acts like a safety net, ensuring that every item passing through the production line meets the desired specifications. In this fast-paced world, where consumer expectations are soaring, the stakes have never been higher. Quality control isn't just about avoiding defects; it's about cultivating trust and delivering reliability.
When we delve into quality control, it's vital to appreciate its multifaceted nature. It's not merely a set of rules imposed from on high; rather, it engages multiple aspects of a business. Every department, from manufacturing to customer service, has a role to play. Quality control encourages a unified approach to maintaining excellence. It encourages teams to communicate and collaborate effectively. This interdepartmental synergy is foundational; the left hand needs to know what the right hand is doing, after all.
The benefits of a solid quality control framework are numerous:
- Enhanced Customer Satisfaction: Happy customers tend to stay loyal.
- Cost Efficiency: Fixing defects at the production stage is often less expensive than addressing them post-sale.
- Brand Reputation: A company known for quality gains a competitive edge.
Conversely, neglecting quality control can result in dire consequences. Failing to catch defects can lead to costly recalls or worse, damage to a brand's reputation. This delicate balance of maintaining standards, while also seeking continuous improvement, makes quality control a vital focus area for every organization.
To truly grasp the importance of quality control, one must explore its definition, significance, and historical context.
Definition of Quality Control
Quality control is often defined as the process through which a business seeks to ensure that its products or services meet a certain level of quality. This involves identifying inconsistencies, measuring them against predetermined standards, and taking corrective actions when deviations occur. Whether it’s a tech startup rolling out a new app or a car manufacturer producing vehicles by the hundreds, quality control strategies come into play.
More specifically, it encompasses:
- Establishing benchmarks for quality at various stages of production.
- Conducting tests to assess adherence to these standards.
- Implementing feedback loops to refine processes.
Importance of Quality Control
The significance of quality control cannot be overstated. It transcends mere defect detection, functioning instead as a lens through which an organization views its entire operation. Robust quality control measures help organizations seize opportunities for improvement, leading to optimized processes and, ultimately, better products.
Let’s not forget that quality control is about more than just the bottom line. It also fosters a culture of accountability among employees. When everyone is involved in maintaining standards, the overall atmosphere in the workplace shifts. Team members take pride in their contributions, knowing that their work directly affects customer satisfaction.
Historical Overview
Early Practices
In the early days of manufacturing, quality control largely revolved around trial and error. Craftsmen relied on their own experiences and intuition, often leading to inconsistent product quality. However, those early practices laid the groundwork for more systematic approaches. The craftsmanship of the past had key characteristics: it was hands-on and personalized.
The lack of standardized methods meant that products varied greatly in quality. This was a disadvantage, but it also provided insights for future developments. As industrialization took over, the need for quality assurance became apparent. Companies had to find a way to scale up production while maintaining some level of consistency, thus giving rise to quality control as we know it today.
Evolution of Standards
As industries grew, so did the complexity of quality control. The evolution of standards emerged as a direct response to these complexities. Organizations began to recognize the need for uniformity, leading to the development of guidelines such as the ISO (International Organization for Standardization). This evolution has been beneficial for fostering a sense of commonality, especially in global markets.
One unique feature of evolving standards is that they are adaptable. They can be revised to accommodate new technologies and methods, ensuring relevance. This adaptability is a double-edged sword; while it allows for growth, it can also lead to confusion among organizations trying to keep up.
Impact of Globalization
In today’s world, globalization has left a profound mark on quality control practices. Companies now operate in an interconnected environment, where suppliers and customers may be oceans apart. The global marketplace necessitates stringent quality controls to maintain product integrity across different regions.
A key characteristic of this global landscape is the competition among businesses, pressing them to uphold high standards continually. Adopting universally accepted quality standards has become essential for market entry. However, this globalization presents unique challenges, such as differing regulations and expectations from various countries. Such complexities require organizations to be astute and adaptable in their approaches to quality control.
The realities of quality control, illustrated through historical practices and trends, reveal its evolution in tandem with manufacturing and market needs. Understanding this context sets the stage for further exploration into the principles, methodologies, and future of quality control.
Key Principles of Quality Control
Quality control is not merely a tick-box exercise; it stands at the heart of ensuring that products meet or exceed standards, enhancing overall operational efficiency. Understanding its key principles is critical for anyone aiming to implement or improve quality control processes in any industry. Below, we will explore three fundamental principles: consistency, customer focus, and continuous improvement.
Consistency
Consistency in quality control means maintaining a standard of excellence across all products and processes. It is about ensuring that each item or service produced meets the established criteria without significant variation. For instance, think of a bakery that produces bread. If every loaf has the same texture and flavor, customers will know what to expect and grow loyal to the brand.
To achieve consistency:
- Standard Operating Procedures (SOPs) should be established. SOPs guide employees on how to execute tasks uniformly.
- Regular training sessions are crucial. Consistent education helps workers understand updated procedures.
- Quality audits should be a regular occurrence, ensuring adherence to set standards.
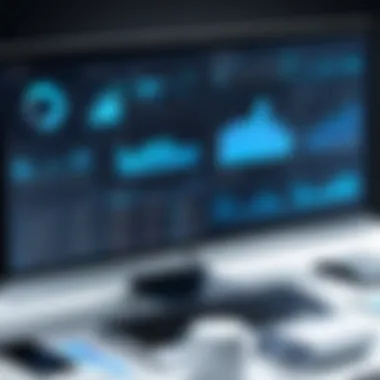
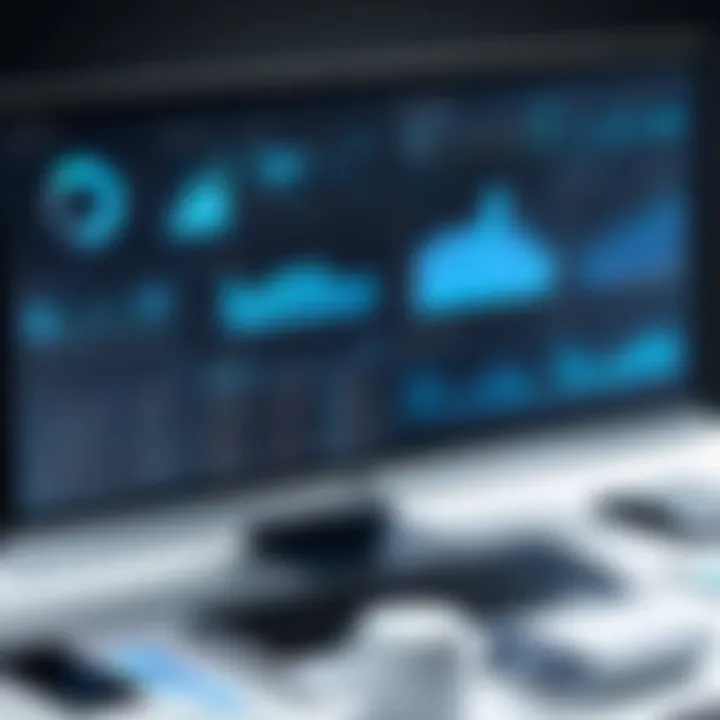
By aiming for consistency, businesses not only enhance their brand reputation but also mitigate risks, reduce waste, and improve profitability, creating a reliable environment where stakeholders know what to expect.
Customer Focus
In the realm of quality control, customer focus embodies the philosophy that the ultimate measure of quality is the satisfaction of the customer. Considering customer needs and expectations should affect every decision related to quality. This principle manifests through understanding market demands, gathering feedback, and adjusting processes based on consumer experiences.
- Engaging in direct feedback channels such as surveys and focus groups gives insights into customer perceptions.
- Implementing a customer relationship management (CRM) system keeps track of complaints, which highlights areas needing improvement.
- Organizations might consider a customer advisory board to gain diverse perspectives from the clientele.
When a company prioritizes customer focus, they often see increased loyalty and repeat business, which ultimately translates into greater sales and a more robust market presence.
Continuous Improvement
Continuous improvement is a philosophy where organizations constantly seek ways to enhance their processes, products, and services. This doesn’t mean making radical changes all the time; instead, it focuses on small, incremental changes that cumulatively make a significant impact over time. A well-known approach is the Plan-Do-Check-Act (PDCA) cycle:
- Plan: Identify an opportunity and plan for change.
- Do: Implement the change on a small scale.
- Check: Use data to analyze the results of the change.
- Act: If the change is successful, implement it on a wider scale.
Incorporating continuous improvement can lead to:
- Enhanced quality and operational efficiency.
- A culture that embraces innovation and challenges the status quo.
- Reduced costs over time as unnecessary expenditures are identified and eliminated.
"Quality is not an act, it is a habit." – Aristotle
Embracing the principle of continuous improvement can differentiate a company in a saturated market, thus ensuring long-term success.
Overall, the key principles of quality control play a critical role in shaping how organizations function. Harnessing the power of consistency, centering efforts around customer focus, and fostering a culture of continuous improvement can significantly enhance the quality management processes, yielding not just operational success, but also customer satisfaction that drives businesses forward.
Quality Control Methodologies
Quality control methodologies serve as the backbone of any quality management system, offering structured approaches to ensure products and services meet predefined standards. They lay the groundwork for continuous improvement, address inefficiencies, and bolster customer satisfaction. Understanding these methodologies can significantly enhance an organization’s efficiency and responsiveness to market demands.
Choosing the right methodology is crucial for identifying potential defects early, which ultimately saves time and resources. Knowing the strengths and weaknesses of various methodologies can help businesses tailor processes to their unique needs, allowing them to navigate challenges effectively.
Statistical Process Control
Statistical Process Control (SPC) is a data-driven methodology widely used across various industries to monitor and control processes. At its core, SPC employs statistical methods to observe and analyze variability in production, offering insights into process performance.
Control Charts
Control charts are a pivotal aspect of Statistical Process Control. They visually depict process data over time, allowing teams to identify trends and variations. The key characteristic of control charts is their ability to distinguish between common cause variation and special cause variation, enabling businesses to react appropriately.
Control charts are a beneficial choice for this article because they provide real-time feedback about process performance. This predictive feature can aid organizations in preemptively addressing issues before they escalate.
One unique feature of control charts is their capacity to provide clear visual evidence regarding process stability. The advantage of this is straightforward: it facilitates immediate understanding among team members, fostering quicker decision-making. However, using control charts requires a solid foundation of data collection and proper training. If teams lack quality data or misinterpret the charts, it could lead to incorrect conclusions, thus counteracting their intent.
Process Capability Analysis
Process Capability Analysis evaluates how well a process can produce products that meet specifications. This analysis is instrumental in determining whether a process is capable of generating output within defined limits consistently. The key characteristic of process capability is its reliance on historical data to gauge a process’s inherent variability.
Its popularity in this article is largely due to its critical role in ensuring quality by comparing the process’s output with customer specifications. When a process is capable, it minimizes waste and rework, directly impacting cost-effectiveness.
A unique feature of process capability analysis is its ability to quantify process performance using indices like Cp and Cpk. These indices provide tangible measures that management can use to advocate for improvements. Conversely, if the process capability is below expectations, it signals a clear need for process reassessment and improvement initiatives, making it an invaluable tool in the quality arsenal.
Six Sigma
Six Sigma is a methodology that seeks to improve quality by removing the causes of defects and minimizing variability in manufacturing and business processes. It is structured around a set of quality management tools and techniques that support the identification and resolution of problems systematically.
Define, Measure, Analyze, Improve, Control
The DMAIC framework—Define, Measure, Analyze, Improve, Control—forms the cornerstone of Six Sigma. It provides a systematic approach to process improvement and is highly regarded for its structured nature. The main strength of DMAIC lies in its focus on quantifying the problem before diving into solutions, ensuring that improvements are based on solid data.
DMAIC is a beneficial component in this article as it encourages a culture of continuous improvement. Its systematic phases guide teams through problem identification to resolution, thereby promoting better team coherence.
A unique feature of DMAIC is its flexibility; it can be applied to virtually any process, making it a favorite in diverse sectors. However, a potential drawback is the time commitment required in data collection and analysis. If teams rush through the Analyze phase, they risk implementing permanent changes for issues that may not be as pressing.
Tools and Techniques
In Six Sigma, various tools and techniques support the problem-solving process. From root cause analysis to process mapping, these tools offer structured approaches to enhance understanding. The key characteristic of Six Sigma tools is their emphasis on data-driven decision-making, ensuring that actions taken are informed and reliable.
These tools are a popular choice in this article as they empower teams to conduct thorough analyses and implement targeted improvements. A distinct feature is their adaptability across industries, allowing companies to customize their approach depending on specific challenges. However, one downside is that mastering these tools requires investment in training, and teams that lack proper knowledge may struggle to implement them effectively.
Total Quality Management
Total Quality Management (TQM) is a holistic approach aimed at long-term success through customer satisfaction. It involves all members of an organization in improving processes, products, and services.
Principles of TQM
The principles of TQM focus on a customer-centric approach while emphasizing continuous improvement and teamwork. The inherent key characteristic is its pervasive nature, as TQM principles apply to every level of the organization, promoting comprehensive quality culture.
This approach is beneficial in the context of this article because it fosters a shared responsibility for quality across departments. This creates a stronger alignment between business goals and customer expectations, significantly enhancing product delivery.
A unique feature of these principles is their focus on employee engagement. When employees feel empowered to contribute to quality initiatives, it not only boosts morale but can lead to improved outcomes. The challenge, however, is that implementing TQM may require significant shifts in company culture and structure, which can be daunting for some organizations.
Implementation Challenges
While the TQM approach is advantageous, several implementation challenges often arise. These include resistance to change, lack of managerial support, and resource constraints. The key characteristic of these challenges is that they can significantly hinder the successful adoption of TQM practices.
Understanding the challenges is critical for this article, as it allows businesses to be proactive. If organizations are aware of high-risk areas, they can devise strategies to address them ahead of time.
One unique aspect of these challenges is that they encourage organizations to foster a culture of openness. By recognizing potential roadblocks early on, teams can work collaboratively to find solutions rather than let problems fester. Nevertheless, organizations must be prepared to invest time and resources into mitigating these challenges for TQM to be truly effective.
Technological Innovations in Quality Control
The realm of quality control has witnessed a seismic shift with the introduction of cutting-edge technologies. This evolution is not just a passing trend; it represents a paradigm shift that enhances efficiency, accuracy, and overall outcomes in various industries. By leveraging technologies such as Artificial Intelligence (AI), automation, and the Internet of Things (IoT), organizations can not only streamline their quality control processes but also gain deeper insights into their operations.
Technological innovations in quality control serve a dual purpose: they increase the reliability of quality assurance processes while reducing the burden on human resources. Consider the benefits and considerations tied up with these advancements. They empower businesses to prevent errors before they happen rather than merely detecting them post-factum. This proactive stance is particularly invaluable in sectors where quality can make or break a reputation.
Artificial Intelligence
Predictive Analytics
Predictive analytics harnesses historical data and algorithms to forecast outcomes, transforming how organizations approach quality control. By examining patterns, it enables companies to anticipate potential issues before they escalate into significant problems. This ability to foresee challenges is what makes predictive analytics a sought-after tool in the industry.
One of the unique features of predictive analytics is its reliance on statistical models that continuously learn from new data, thereby refining the insights it provides. However, it is important to consider that its effectiveness is directly tied to the quality of the data fed into the system. Poor data can yield unreliable predictions, which might mislead decision-making. This aspect makes predictive analytics both a powerful ally and a double-edged sword in quality management.
Machine Learning Applications
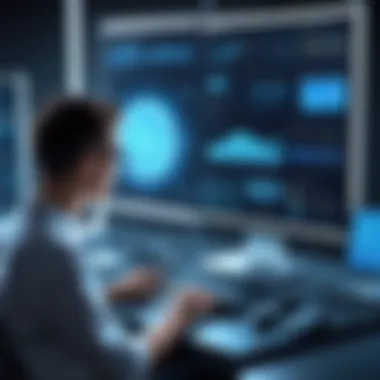
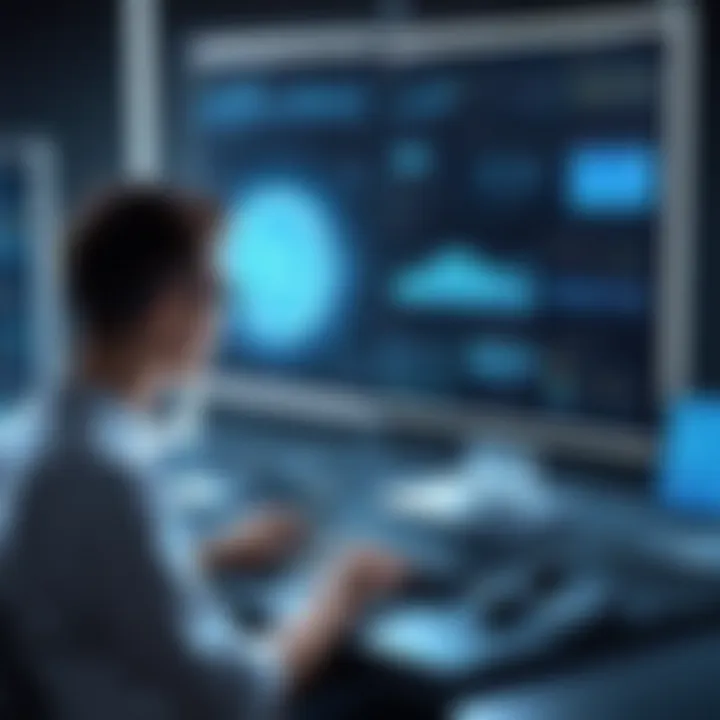
Machine learning (ML) pushes the envelope of predictive analytics by not just analyzing past data but actively learning from it to improve its algorithms over time. This technology finds particular strength in anomaly detection and performance optimization. Industries are increasingly adopting machine learning applications because they can reveal hidden insights that conventional methods might miss.
The unique feature of machine learning is its capacity to process vast amounts of data quickly, making it a robust choice for fast-paced environments. That said, the challenge lies in the fact that implementing machine learning systems requires significant investment in infrastructure and talent. When considering costs against benefits, it can be a balancing act for organizations aiming to innovate within their quality control frameworks.
Automation
Robotic Process Automation
Robotic Process Automation (RPA) represents a game-changer in managing repetitive and mundane quality control tasks. By employing software robots to handle these processes, organizations can free up human resources for more strategic endeavors. RPA enhances efficiency and minimizes the risk of human error, leading to more consistent outputs.
A key characteristic of RPA is its ability to function continuously without breaks, vastly improving the throughput of quality control operations. However, the implementation process can be complex, requiring detailed mapping of existing workflows. Additionally, while RPA excels in routine tasks, it may struggle with decisions that require human judgment, forcing organizations to find the right balance between automated and manual processes.
Integration with Quality Tools
The integration of automation with existing quality tools allows for a seamless flow of information among various systems, improving the overall efficiency of the quality control process. Good integration means less hassle, faster response times, and more accurate data analysis. This feature is crucial for organizations seeking a comprehensive view of their quality metrics.
Nevertheless, businesses must remain mindful of the potential hurdles during integration. Misalignment of systems can lead to data silos that sap productivity and disrupt workflows. Therefore, careful planning and alignment of business objectives with technological capabilities become vital for success.
Internet of Things
Data Collection in Real-time
Data collection in real-time through IoT devices helps organizations gather continuous insights into their production processes. Sensors can monitor variables such as temperature, humidity, and pressure instantaneously, enabling quality control teams to act on deviations promptly. What sets this approach apart is its ability to provide insights that were once unattainable without extensive manual monitoring.
A major advantage of real-time data collection is its potential for immediate corrective actions, ensuring that quality standards are maintained consistently. However, the challenge lies in managing the massive influx of data generated. Organizations need to have robust data management strategies in place to effectively utilize this wealth of information.
Enhancing Quality Monitoring
The IoT aims to enhance quality monitoring by giving stakeholders visibility across the entire production line. With interconnected devices, quality issues can be detected and rectified much faster than before. This level of monitoring allows for a proactive rather than reactive approach in quality control.
One unique feature is the capacity to create alerts for deviations from accepted quality standards, instantly notifying the relevant teams about possible issues. This characteristic makes IoT devices particularly beneficial for maintaining product integrity. Despite these gains, the complexity and costs associated with implementing IoT solutions can be substantial and may require a reevaluation of existing protocols and infrastructures.
Challenges in Quality Control
Quality control isn’t just a repetitive task on an assembly line or a checkbox for compliance in a manual. It's a crucial component that drives operational success across industries. However, the road to effective quality control is often peppered with obstacles that can hinder progress. Understanding these challenges is pivotal for organizations aiming to enhance their quality management systems. Whether it’s a matter of getting everyone on the same page or ensuring the necessary resources are in place, these hurdles can affect overall productivity, profitability, and even compliance with regulations. Let’s dissect these challenges further.
Resistance to Change
Implementing quality control enhancements often stumbles due to resistance from employees. This reluctance can stem from a fear of the unknown or simply from being set in old habits. When new methodologies or technologies are introduced, teams might respond with skepticism. They may view new procedures as extra work rather than an improvement. Engaging employees early in the process and highlighting the benefits they stand to gain is crucial.
For instance, instead of insisting on a top-down approach in changing quality standards, organizations can foster an environment of collaboration where team members feel their input is valued. Training sessions can be used not just for instruction but also for generating enthusiasm around the change. It’s akin to trying to get a cat into a bath; you have to ease them in somehow.
Resource Allocation
Another considerable challenge lies in the allocation of resources. When dealing with quality control, materials, time, and skilled personnel are all essential. Insufficient investment in quality assurance can lead to overlooked factors that affect product integrity. Just as a garden requires the right amount of water, sunlight, and nutrients, quality control needs an adequate supply of resources to flourish.
Organizations must evaluate where their resources are going and whether these allocations support their quality objectives. For example, underfunding training programs may yield a workforce that lacks the skills to uphold quality standards. Smart budgeting towards technology upgrades or continuous training could lead to more consistent outcomes and higher efficiencies down the line.
Regulatory Compliance
Staying compliant with regulatory standards is another weighty concern. Industries like pharmaceuticals and food production are tightly regulated, and the penalties for non-compliance can be steep. Regulatory bodies frequently update their requirements, and a failure to adapt can not only lead to fines but also tarnish a company’s reputation. It’s essential to stay abreast of evolving regulations to avoid pitfalls.
Organizations might need to establish dedicated teams that focus solely on keeping up with compliance issues. Regular audits and checks can help in maintaining adherence to these regulations, ensuring that the quality management system is aligned with legal requirements.
"A stitch in time saves nine." Keeping ahead of regulatory changes can save organizations from larger issues, such as costly recalls or public relations disasters. Committing some of your time and resources to compliance preparation is a pivotal practice.
Ultimately, navigating through these challenges requires a strategic and thoughtful approach. Tackling resistance to change involves thoughtful communication and employee engagement. Managing resource allocation demands a keen eye on operational efficiency. Lastly, being proactive about regulatory compliance safeguards not just the organization’s bottom line, but it also builds trust with consumers. Addressing these factors will help ensure a robust quality control system.
The Role of Data in Quality Control
In today’s fast-paced environment, the effective use of data in quality control processes is both critical and transformative. Data acts as the backbone for identifying issues, tracking performance, and optimizing processes within various industries. By employing data-driven decision-making, organizations can significantly enhance their quality control strategies. This is particularly vital as industries grapple with increased customer expectations and regulatory requirements, making the role of data more essential than ever.
One specific element of data's role is its ability to give real-time insights into quality metrics, allowing businesses to respond swiftly to any deviations. When organizations utilize data effectively, they not only improve product quality but also bolster customer satisfaction. The numerous benefits associated with integrating data into quality control include better prediction of trends, timely adjustments in processes, and maintaining compliance with industry standards. It is this flexibility and adaptability that marks data as an invaluable resource in quality management strategies.
Data Collection Methods
Surveys and Audits
Surveys and audits represent a proactive approach to gathering valuable information. These tools provide firsthand insights from customers and frontline employees, thus bridging the gap between management and operational reality. The key characteristic of surveys is their ability to capture subjective opinions that can shed light on areas needing improvement. Audits, on the other hand, analyze processes against established standards, making them a robust methodology for ensuring compliance and performance.
Surveys are a popular choice in this article due to their versatility—ranging from customer satisfaction polls to employee feedback forms. They empower organizations to gather collective opinions and identify trends without drowning in subjective narratives. However, while surveys can provide a wealth of information, the risk lies in potential bias or misinterpretation of data. Adding to this dynamic, audits are systematic, minimizing conjecture and ensuring a more objective overview of operational efficacy.
Quality Checklists
Quality checklists serve as another cornerstone in the data collection toolkit. These documents systematically outline criteria that must be met for a process or product to be deemed acceptable. Their main ability is to bring clarity and structure to quality inspections, ensuring that no significant detail slips through the cracks.
A key feature of quality checklists is their straightforward format which can enhance compliance rates across diverse teams. They are particularly beneficial in environments where adherence to defined standards is paramount, like in the pharmaceutical or manufacturing sectors. However, one unique aspect of checklists could also be a double-edged sword: while they provide guidance, an over-reliance on them may lead teams to miss nuanced issues not captured by mere checkboxes.
Data Analysis Techniques
Descriptive Statistics
Descriptive statistics delivers powerful insights through the summarization of data collected. Its contribution lies in translating raw data into understandable metrics, helping organizations gauge trends and patterns effectively. This method is crucial for determining averages, variances, and other summarization techniques that support informed decision-making.
One appealing aspect of descriptive statistics is its ability to make complex data manageable, hence a favored choice for analyzing quality control information. Utilizing tools like mean, median, and standard deviation allows organizations to process statistics quickly and accurately. However, the downside is that it only tells part of the story; it lacks the depth to uncover underlying causes of discrepancies or quality issues.
Data Visualization
Data visualization takes the insight gained from analysis and presents it in visual formats, like charts or graphs. This technique helps stakeholders grasp intricate data at a glance, fostering more informed discussions and strategic planning. Its illustrative nature plays a significant role in quality control by making metrics readily digestible.
Key to data visualization's strength is its appeal; visuals can elucidate information that raw data often obscures. This makes it a popular choice in this article because it encourages engagement and understanding among team members. Yet, there's a cautionary note: an oversimplification might lead to misinterpretation if critical data points are omitted or glossed over in the quest for clarity.
Feedback Loops
Feedback loops serve as a mechanism through which organizations can continuously assess and improve their quality control processes. These loops help ensure that the lessons learned from data_COLLECTION methods and analysis techniques are not merely noted, but actively incorporated into ongoing practices. The process typically involves collecting data, analyzing results, implementing changes, and then re-evaluating the impacts. With every cycle, organizations become more adept at responsive quality management.
Consequently, feedback loops are often characterized as an iterative process of enhancement, driving quality improvement into the organizational culture. By establishing strong feedback systems, businesses can rapidly adapt to shifts in market demands and expectations while fostering a proactive rather than reactive approach to quality control.
In summary, the strategic integration of data collection methods, analysis techniques, and robust feedback loops presents an effective formula for elevating quality control standards across industries. Data not only informs but also propels organizations towards operational excellence.
Quality Control in Different Industries
Navigating the complex world of quality control reveals its crucial role in various industries. Each sector has unique demands, yet the principles of quality control serve a unifying purpose — enhancing product and service delivery. This section explores how different industries adapt quality control to their specific needs, ensuring not only compliance but also remarkable customer satisfaction. Consistent quality is the cornerstone of any thriving business, making this discussion imperative for anyone looking to grasp the multifaceted nature of quality control across sectors.
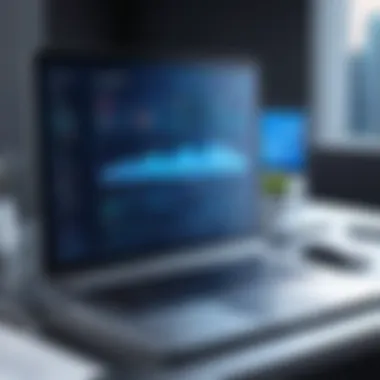
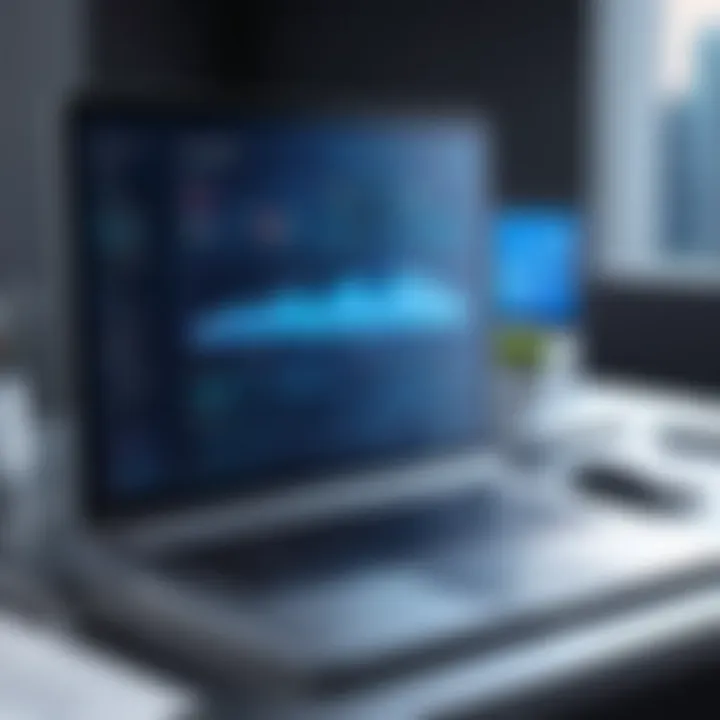
Manufacturing Sector
The manufacturing industry stands as one of the most traditional landscapes for quality control application. In essence, this sector embodies the need for rigorous quality standards due to the high stakes involved. A lapse in quality not only jeopardizes production efficiency but can also lead to safety risks for consumers.
Implementing quality control in manufacturing typically encompasses:
- Quality Assurance: Ensures that manufacturing processes meet designated standards.
- Statistical Process Control (SPC): Uses statistical methods to monitor and control processes, minimizing variation.
- Lean Manufacturing Principles: Focus on waste reduction while maintaining quality.
By monitoring equipment performance and conducting regular inspections, manufacturers can catch defects early. This proactive approach is akin to taking preventative medicine to avoid major health issues down the road. Regular training and adherence to documented protocols further bolster quality assurance efforts.
"Quality is not an act; it is a habit." — Aristotle
Pharmaceutical Industry
In the pharmaceutical industry, quality control transcends basic manufacturing principles. It's intertwined with regulatory compliance, given the direct impact of product safety on public health. The processes employed must meet strict guidelines from global regulatory bodies such as the FDA.
Key components of quality control in this sector include:
- Good Manufacturing Practices (GMP): Enforces consistent quality in production and testing.
- Validation Processes: Ensures that pharmaceutical products meet safety and efficacy criteria before reaching the market.
- Quality Risk Management: Identifies potential risks in the production process, analyzing their impact on patient safety.
With developments in biotechnology and customized medications, quality control must also adapt to newer methodologies. Continuous monitoring and rigorous testing throughout the drug development cycle illustrate the industry's acknowledgment of quality as a fundamental aspect.
Information Technology
Quality control in the information technology field presents unique challenges and opportunities. Unlike tangible products, IT deliverables often revolve around software and system services. Here, quality control focuses on functionality, usability, and security — areas critical to user satisfaction and data integrity.
Strategies for quality control in IT include:
- Agile Methodologies: Encourages iterative development and constant feedback, ensuring that the final product meets user expectations.
- Automated Testing: Tools are employed to carry out repetitive testing tasks, greatly improving efficiency.
- DevOps Practices: Integrates development and operations, allowing for rapid and reliable software delivery.
In the age of fast-paced technological advancements, ensuring the quality of software applications has become paramount. A bug-riddled application can lead to data breaches or user frustration, emphasizing the critical need for robust quality assurance protocols.
By understanding the distinct quality control demands across these industries, professionals can better navigate their own roles within their respective sectors, ultimately enhancing both compliance and consumer trust.
Best Practices for Quality Control
Quality control is not just a regulatory obligation; it’s a commitment to delivering products and services that meet or exceed customers’ expectations. Implementing best practices in quality control is pivotal for organizations looking to maintain their reputation and enhance operational efficiency. Through adhering to effective methodologies, businesses can nip problems in the bud, optimize processes, and ultimately foster a culture of continuous improvement.
Training and Development
Having a well-trained team is the backbone of quality control. Knowledge is power, and in the context of quality management, the more informed your team is, the better the quality of output. Training staff on quality control processes and practices ensures everyone understands their role in maintaining standards.
Consider integrating various training methods, like workshops, online courses, or on-the-job training, enabling employees to grasp both the theoretical and practical aspects of quality control. More often than not, when staff feel empowered and educated, they are more likely to take ownership of their work. Not only does this reduce errors, it also leads to higher job satisfaction.
"Teams that have undergone effective training improve their performance exponentially, and that reflects in the quality of the product."
Fostering an environment where continuous learning is encouraged can also help employees stay updated with recent developments in quality management practices. Frequent refresher courses can keep skills sharp and quality principles top of mind.
Documentation and Standardization
When it comes to quality control, documentation is key. By clearly documenting procedures, organizations create a roadmap for quality practices, which helps in standardizing operations across various levels. This isn’t just about filling out forms, but rather about defining processes that are crucial for consistency and traceability.
Standard operating procedures (SOPs) should be established for every task that contributes to quality. Here are the benefits of keeping solid documentation:
- Consistency: Ensures tasks are performed uniformly every time.
- Accountability: Provides a reference point if standards are not met.
- Efficiency: Streamlines retraining or onboarding new employees.
Moreover, this documentation enables organizations to better comply with regulatory standards and facilitates easier audits. When everything is written down, the likelihood of miscommunication decreases significantly.
Regular Audits and Assessments
Conducting regular audits and assessments is an indispensable practice in quality control. This is not just about checking off items on a list but diving deep into processes to identify inefficiencies and areas for enhancement. Audits can be internal or external and should be scheduled consistently to maintain accountability.
Regular assessments help in:
- Identifying Gaps: Uncovers weak spots in quality control processes.
- Performance Measurement: Evaluates whether current methods are yielding expected results.
- Continuous Improvement: Facilitates a proactive approach to refine practices over time.
Future Trends in Quality Control
Understanding the evolving landscape of quality control is crucial in ensuring organizations can not only keep pace with industry standards but also exceed them. As we stand on the brink of further disruptions brought by technology and changing consumer expectations, it becomes evident that adapting to these future trends is not just beneficial but essential. This section will shed light on three significant trends shaping quality control: the influence of artificial intelligence, the push for sustainability, and the rise of remote audits and inspections. Each of these elements brings distinct benefits and considerations which organizations must navigate to thrive.
Influence of AI on Quality
Artificial Intelligence is poised to revolutionize quality control by streamlining processes, enhancing accuracy, and providing valuable insights into performance metrics. With AI at play, companies can automate routine tasks, such as data collection and reporting, freeing up human resources for tasks that require critical thinking and innovation. This shift can substantially increase efficiency.
Moreover, AI enables predictive analytics, allowing organizations to foresee potential quality issues before they escalate. By analyzing historical data, AI algorithms can identify patterns that might elude human analysis. This capability doesn't just focus on problems after they occur but anticipates and mitigates them proactively. The deployment of these technologies results in improved product consistency and boosts customer trust.
"Using AI in quality control is like having a crystal ball that helps predict challenges before they even arise."
Sustainability and Quality Control
As environmental awareness grows, the concept of sustainability in quality control cannot be ignored. Companies are increasingly realizing that integrating sustainable practices can enhance their brand image and resonate well with conscious consumers.
Integrating sustainability into quality management may involve re-evaluating supply chains, reducing waste, and choosing eco-friendly materials. Not only does this approach appeal to environmentally-minded customers, but it also often leads to cost savings in the long run. By minimizing waste and enhancing resource efficiency, organizations can maintain quality while also caring for the planet.
Industries that embrace sustainability can also gain a competitive edge. Regulatory bodies are beginning to emphasize the importance of sustainable practices, which makes it vital for firms to stay ahead of the curve. As customers grow more conscientious, they expect businesses to uphold environmental responsibilities while delivering top-tier quality.
Remote Audits and Inspections
The shift towards remote working has birthed a new trend in quality control—the implementation of remote audits and inspections. This development is especially relevant in the wake of global challenges that restrict physical presence. Organizations can leverage technology to conduct thorough audits with minimal disruption.
Remote inspections utilize video conferencing, drones, and digital documentation, enabling a more flexible and efficient method of maintaining quality standards. This not only saves time but significantly reduces travel costs associated with traditional audits. However, it does require teams to invest in the right technology and training to ensure effective implementation.
Closure
The conclusion serves as a cornerstone in understanding the intricate web of quality control practices outlined in this article. By summarizing the essence of what was discussed, it emphasizes the direct correlation between effective quality control and the overall success of any organization. The takeaway is clear: failing to prioritize quality not only compromises consumer trust but can severely disrupt operational efficiency.
Summary of Key Points
- Importance of Quality Control: Throughout the article, we highlighted how quality control acts as a safety net, ensuring that products and services meet certain standards before reaching customers.
- Methodologies and Innovations: The discussion covered various methodologies like Six Sigma and Total Quality Management, along with emerging technologies such as AI and IoT, which are reshaping the landscape of quality control.
- Challenges and Solutions: We explored significant hurdles organizations face, including resistance to change and regulatory compliance, while also offering strategic solutions that can aid in overcoming these challenges.
As we navigate through the complexities of a rapidly-evolving market, these key insights offer a roadmap for professionals dedicated to mastering quality control.
The Path Ahead for Quality Control
Looking forward, it becomes apparent that the field of quality control is not stagnant; it is an evolving entity that mirrors advancements in technology and shifts in consumer expectations. Organizations will increasingly tap into data-driven strategies, harnessing analytics to gain insights and optimize their quality processes. This will not only enhance product reliability but also elevate customer satisfaction.
Moreover, the prospect of remote audits will gain traction as organizations adapt to global challenges. The agility of remote quality assessments ensures that companies can maintain quality standards without physically being on-site.
"Quality is not an act, it is a habit." This statement encapsulates the essence of quality control initiatives. Moving ahead, cultivating a culture where quality is the cornerstone of every task will be crucial. People will need ongoing training, and employers must foster an environment where quality thrives and continuously improves.
In summary, the path ahead is layered with both challenges and rewarding opportunities. Professionals in the field must remain adaptable, proficient, and committed to quality excellence. With the right approach, the organizations will not just meet the standards but set them.